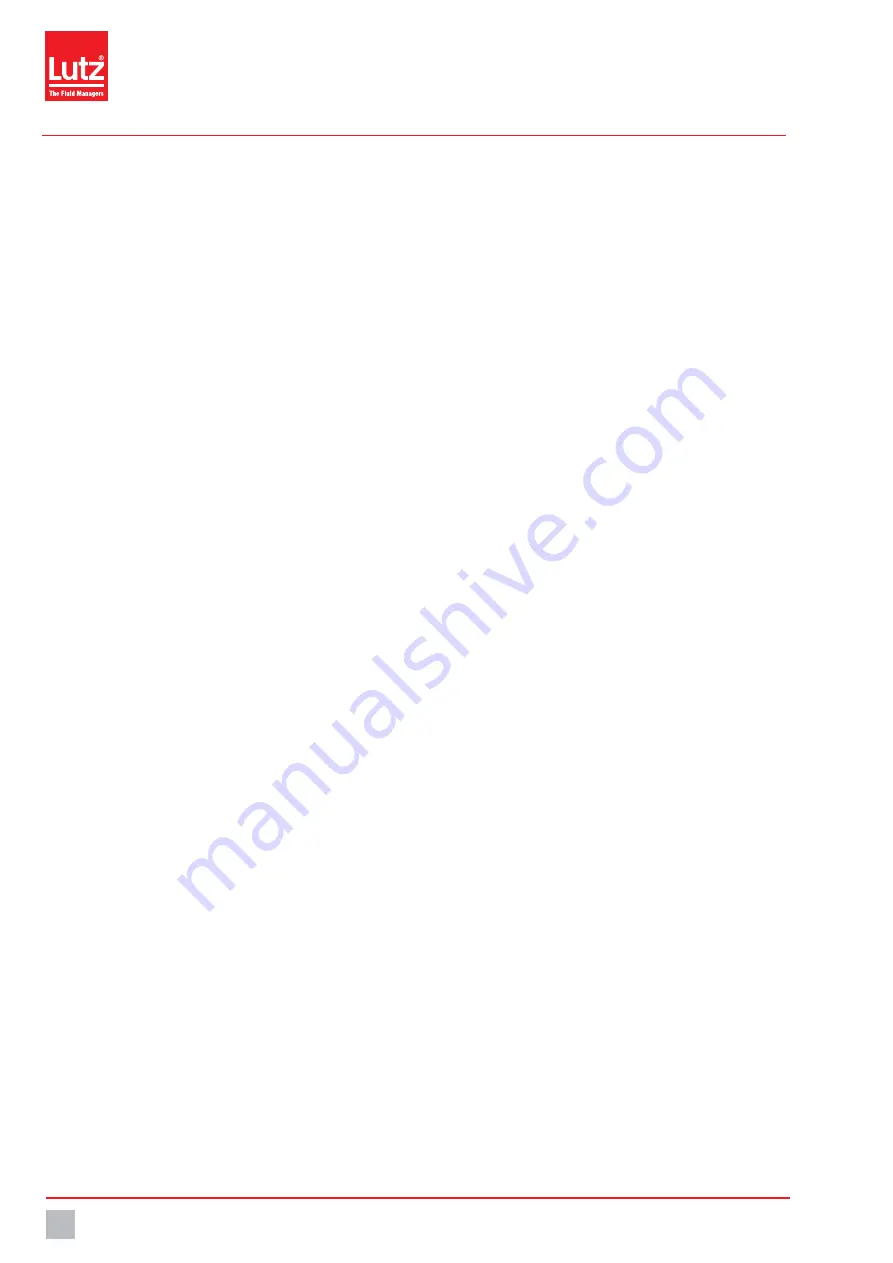
Intended use
Foreseeable misuse
10
© Lutz-Jesco GmbH 2014
BA-10103-02-V01
Stepper Motor-driven Diaphragm Dosing Pump
MEMDOS SMART LK
Operating instructions
suction and discharge valves
Through-suction at installation without back-pressure valves
Damage due to undamped acceleration mass forces
Exceeding the admissible pressure on the suction and discharge sides
Using damaged parts
3.6.3 Incorrect electrical installation
Connecting the mains voltage without a protective earth
Unsecured mains or one that does not conform to standards
Not possible to immediately or easily disconnect the power supply
Wrong connecting cables for mains voltage
Dosing pump accessories connected to wrong sockets
Diaphragm monitoring not connected or defective
Protective earth removed
3.6.4 Incorrect commissioning
Commissioning with damaged plant
Shut-off valves closed at commissioning
Closed suction or pressure line, e.g. due to blockages
Personnel was not informed before commissioning
System was recommissioned after maintenance without all the
protective equipment and fi xtures, etc. being reconnected.
Inadequate protective clothing or none at all
3.6.5 Incorrect operation
Protective equipment not functioning correctly or dismantled
Modifi cation of the dosing pump without authority
Ignoring operational disturbances
Elimination of operational disturbances by personnel without
adequate qualifi cations
Deposits in the dosing head due to inadequate purging, particularly
with suspensions
Bridging the external fuse
Operation made more diffi cult due to inadequate lighting or machines
that are diffi cult to access
Operation not possible due to dirty or illegible display of the dosing
pump
Delivery of dosing media for which the system is not designed
Delivery of particulate or contaminated dosing media
Inadequate protective clothing or none at all
3.6.6 Incorrect maintenance
Carrying out maintenance during ongoing operation
Carrying out work that is not described in the operating instructions
No adequate or regular inspection of correct functioning
No replacement of damaged parts or cables with inadequate
insulation
No securing against reactivation during maintenance work
Using cleaning materials that can cause reactions with the dosing
media
Inadequate cleaning of the system
Unsuitable purging medium
Unsuitable cleaning materials
Cleaning materials left in system sections
Using unsuitable cleaning equipment
Using the wrong spares or lubricants
Contaminating the dosing medium with lubricant
Installing spares without following the instructions in the operating
manual
Blocking venting orifi ces
Pulling off sections of the plant
Contamination at installation without a dirt trap
Mixing up the valves
Mixing up the sensor lines
Not reconnecting all the lines
Damaging or not installing all the seals
Not renewing seals
Not paying attention to safety data sheets
Inadequate protective clothing or none at all
3.6.7 Incorrect decommissioning
Not completely removing the dosing medium
Dismantling lines while the dosing pump is running
Device not disconnected from the power supply
Using the wrong dismantling tools
Inadequate protective clothing or none at all
3.6.8 Incorrect disposal
Incorrect disposal of dosing media, operating resources and other
materials
No labelling of hazardous substances