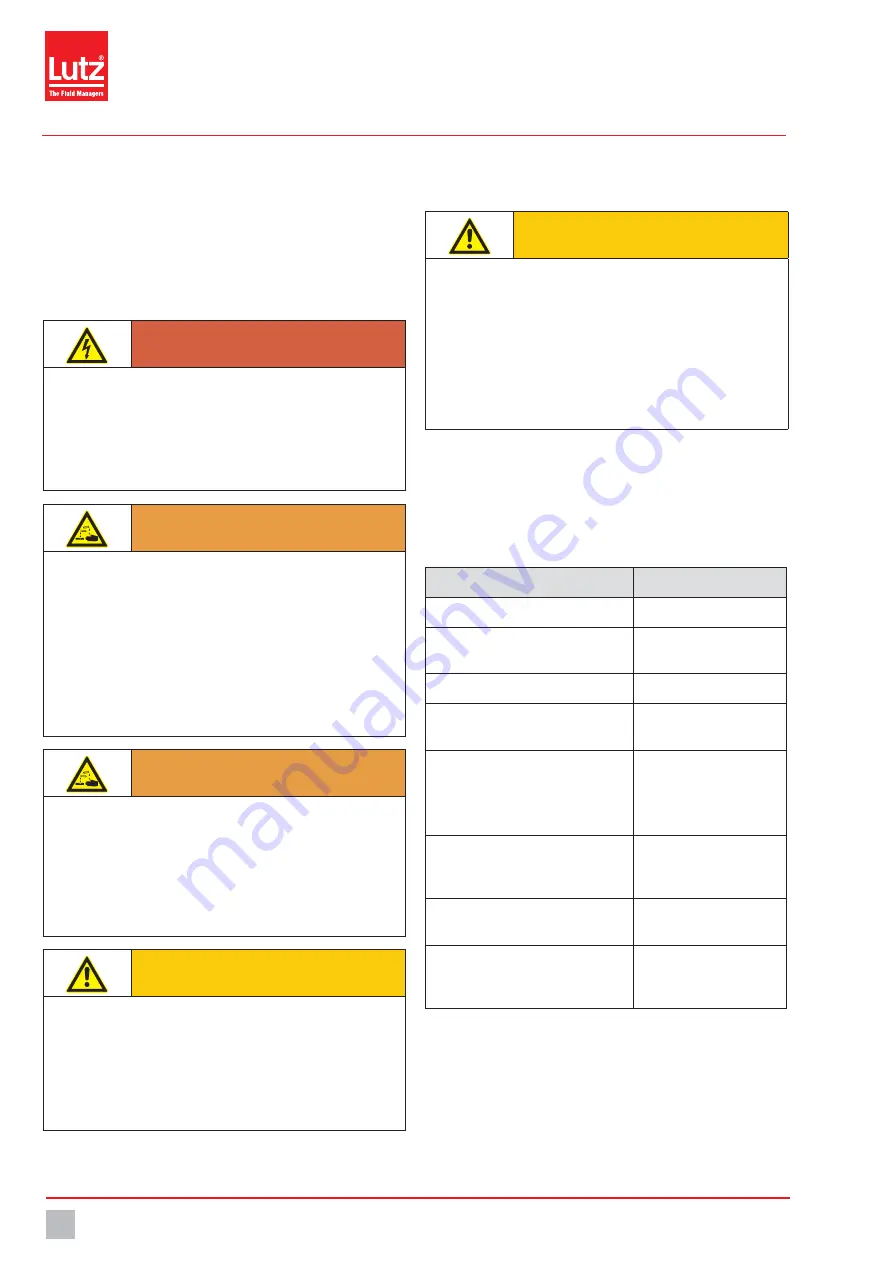
Maintenance
Maintenance intervals
46
© Lutz-Jesco GmbH 2014
BA-10103-02-V01
Stepper Motor-driven Diaphragm Dosing Pump
MEMDOS SMART LK
Operating instructions
12
Maintenance
Lutz-Jesco dosing pumps are produced to the highest quality standards
and have a long service life. Nevertheless, some of their parts are subject
to wear due to operation (e.g. diaphragms, valve seats, valve balls). This
means that regular visual inspections are necessary to ensure a long
operating life. Regular maintenance will protect the dosing pump from
operation interruptions.
DANGER
Mortal danger from electric shock!
Live parts can infl ict fatal injuries.
Before carrying out any maintenance work, always disconnect the
dosing pump from the power supply.
Secure the dosing pump from accidental power-up.
WARNING
Caustic burns or other burns through dosing media!
While working on the dosing head, valves and connections, you may
come into contact with dosing media.
Use suffi cient personal protective equipment.
Rinse the dosing pump with a medium (e.g. water) which does not
pose any risk.
Release pressure in hydraulic parts.
Never look into open ends of plugged pipelines and valves.
WARNING
Caustic burns or other burns through dosing media!
After connecting the mains supply, residual dosing media in the
dosing head can spray out.
Before connecting the mains supply, connect the dosing lines.
Check that all the screw connections have been tightened
correctly and are leak-proof.
CAUTION
Danger of personal injury and material damage!
The dosing pump can generate a pressure that is many times the
rated one. The dosing medium can escape in the case of material
failure or wear on the dosing head, the connection pipe or the seals
that are used.
Carry out maintenance work at the recommended intervals.
CAUTION
Increased risk of accidents due to insuffi cient qualifi ca-
tion of personnel!
Dosing pumps and their accessories may only be installed, operated
and maintained by personnel with suffi cient qualifi cations. Insuffi cient
qualifi cation will increase the risk of accidents.
Ensure that all action is taken only by personnel with suffi cient and
corresponding qualifi cations.
Prevent access to the system for unauthorised persons.
12.1 Maintenance intervals
This table gives you an overview of maintenance work and the intervals
at which you must carry it out. The next few chapters contain instructions
for carrying out this work.
Maintenance work to be carried out
Frequency
Check that piping is seated fi rmly
Regularly
Check that suction and discharge
valves are seated fi rmly
Regularly
Clean suction and discharge valves
Regularly
Check that electrical connections are
not damaged
Regularly
Tighten up dosing head bolts
Regularly
Before initial commissioning
After each diaphragm
change
Check diaphragm for leakage due to
rupture
Regularly (as long as no leak
monitoring system is
installed)
Check that the installed accessories are
functioning correctly
Regularly
Check the dosing pump for unusual
noises during operation, unusual
temperatures or smells
Regularly
Tab. 41: Maintenance information and maintenance intervals