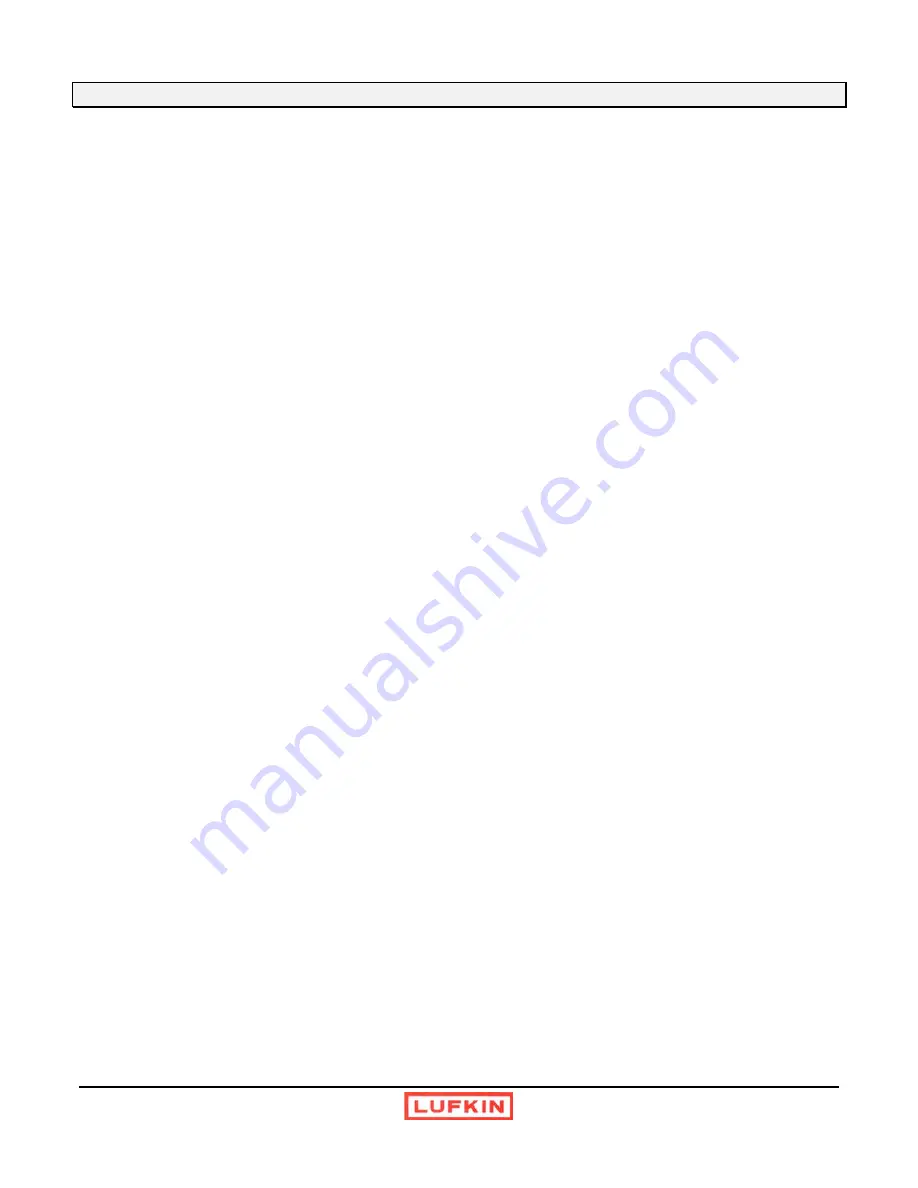
Page 37
SECTION 10
10.1 END DUMP MAINTENANCE
10.1.1 TAIL GATE LATCHES AND ASSEMBLY
The tailgate latch normally opens with the use of a push pull valve located near the center of the
trailer. In some cases, however, an automatic tailgate latch may be installed, which allows the
tailgate latches to open as the dump cycle begins. Before the first load is hauled, the dump should
be raised to check for proper release of the latches. There are two (2) grease fittings on the half-
round dump (HRD) tailgate hinges. They should be periodically greased to keep them operating
properly. Grease with a premium grade of wheel bearing grease.
10.1.2 FIFTH WHEEL ASSEMBLY
The upper fifth wheel assembly needs greasing periodically to prevent wear and flush out foreign
matter at the exposed pivot points. There are two (2) grease fittings on the plate to grease the fifth
wheel, four (4) on radius arm knuckles, two (2) at front and two (2) at rear, two (2) on the hydraulic
cylinder, one (1) at top pivot pin (ULD models only), and one (1) at bottom pivot pin. Grease with a
premium grade of wheel bearing grease.
10.1.3 HYDRAULIC
CYLINDERS
Some hydraulic cylinders are equipped with an automatic air bleeder valve, which is located in top
of the top stage. This valve will permit air to exhaust from the top of the cylinder until hydraulic oil
forces the ball up and seals. This replaces the manual bleeder valve. There will be a small mist of
oil escaping in the air and is not indicative of a malfunction. If oil continues to leak after cylinder is
pressurized, it may be used as a manual bleeder until repair can be made. To stop flow, use a 7/32”
Allen Key to turn the set screw in the center of the bleeder cartridge in a clockwise direction until it
bottoms out. To allow release of air, back out screw until it is flush with top of cartridge body.
Pressurize cylinder and when all air is purged, turn set screw clockwise to bottom out. Usually the
malfunction is due to foreign matter preventing the ball from seating. The cartridge can be removed
with a 3/4” thin wall deep socket. Remove the set screw, spring, and ball. Flush out, wipe clean,
and reassemble. The correct set screw depth is determined by the top of the set screw head being
flush with the top of the cartridge body.
Hydraulic fluid used in dump trailer operation is very important to the life of the pump. LUFKIN
recommends a hydraulic fluid that is rated as a petroleum base (PB) with 150-160 SSU/100°F.
Hydraulic fluids have additives to control foaming, rusting, oxidation, and to release entrained air
quickly. Do not mix motor oil with hydraulic fluid. If foaming occurs, it will be blown out the vent cap.
Vent should be kept clean and open. It is recommended that when hydraulic fluid is added to a
reservoir that it be run through 100 mesh screen to filter out contamination. Starving a pump of fluid
or air in the fluid will cause scoring of the pump side plates and gears. Usually a high-pitched
whining or screaming noise indicates cavitation. If the pump sounds as though it is “gargling
marbles,” it is an indication that air bubbles are present. Keep a check on fluid in the reservoir. Low
fluid level can cause both cavitation and aeration. Slowing down pump speed will help both
problems. Either a rigid mount or oscillating fifth wheel can be used for a dump trailer operation.
If
oscillating fifth wheel is used, it must be blocked so it will not oscillate.
Never let a pump run dry of fluid because only a few seconds will destroy it.
10.1.4 FLOORS
AND
WALLS
Periodic inspection of the inside of dump trailer is imperative. It is known that sand and gravel, as
well as other abrasive materials, will, over time, wear out a steel floor and walls. Wear rate is
greatest on the rear 1/3 of the trailer floor or walls.