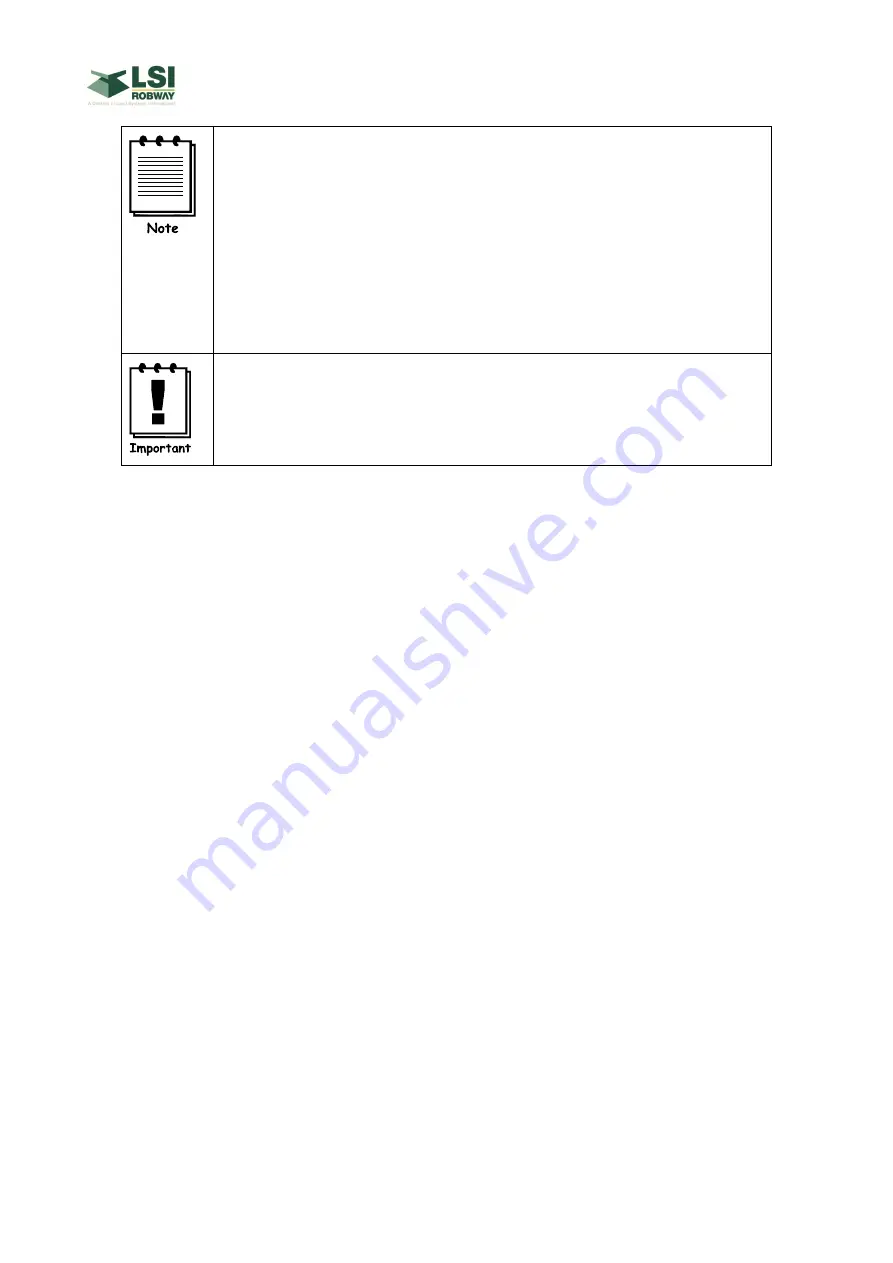
Please note that while in view mode, that is using either "VIEW
UNCALIBRATED ..." or "VIEW CALIBRATED ..." functions, the
ENTER
key works as a toggle switch to turn that channel ON or OFF. This
function allows the user to temporarily turn a sensor off if it is not needed.
E.g. if you want to use the main winch only on a twin winch system;
normally, if you have not connected the auxiliary sensor up, the RCI-3100
will report an error and activate motion cut. To prevent this you can press
the ENTER key, while in "VIEW UNCALIBRATE TRANSDUCER 2
function", to turn the auxiliary channel off.
To turn a channel back on, you have to re-enter the same VIEW
UNCALIBRATED... function and press the ENTER key again.
Remember that you must always end a view function by pressing the
CANCEL key.
7.3. Tools Required for Calibration
To ensure correct calibration, you will require the following;
an accurate 100’ measuring tape
an accurate boom angle finder tool
a Robway RCI simulator tool is recommended
a notepad to record results
the correct Robway system manual for the crane
7.4. Map of Calibration (suggested order)
Set date and Time
Verify the raw counts stay within 33-999 for full working range of all sensors.
Ensure all digital inputs (switched) are wired correctly, incl. ATB.
Ensure all digital outputs (switched) are wired correctly.
Review all geometry Function code settings for correctness
Check / Set the following function codes
No. of Samples (amount of averaging applied to sensor inputs)
Set Lift Value (enter a weight slightly larger than the selected winch hook block)
Set Rigging Load (enter the maximum allowable load allowed during rigging)
Set Rigging Length (enter the maximum boom length allowed during rigging)
Set % SWL trip points (nominally set to 85, 100 and 110%)
Set Data-logger recording points (if supplied)
Calibrate lo/hi boom angle sensor.
Calibrate short/long boom length sensor (telescopic cranes only)
Calibrate lo/hi luffing fly angle sensor (if fitted)
Set Amplifier gain for Transducer 1 to suit load-cell m/volt output.
Set Amplifier gain for Transducer 2 to suit load-cell m/volt output.
Test & Calibrate Transducer 1.
Test & Calibrate Transducer 2.
Calibrate lo/hi luffing fly angle sensor (if fitted)
Calibrate Active winch – main.
Calibrate Active winch – aux.
Calibrate Unladen boom radius correction
Calibrate Laden boom radius correction
Boom Stop Friction (compression) correction.
Once happy the system is operating correctly, perform a “Cal-Table Backup” to ensure the
calibration data can be restored if necessary.
Use the “Transmit LM Data” function code to save a copy of the load calibration to a PC file.
Use the “View Cal-Data” function code to manually record (pen and paper) the sensor calibration
data as an extra safeguard.
Summary of Contents for RCI-1550 LM
Page 2: ......
Page 58: ...Drawings Part A System Components ...
Page 59: ......
Page 60: ......
Page 61: ......
Page 62: ......
Page 63: ...APPROVED BY TOL 0 0 0 1 2 3 4 55 26 2 0 7 2 8 9 1 1 1 1 0 7 5 6 2 ...
Page 64: ......
Page 66: ...APPROVED BY TOL 0 0 0 1 22 3 4 5 6 0 22 2 1 7 8 98 1 7 8 98 7 8 98 7 8 98 1 0 9 8 3 6 8 3 ...
Page 67: ... APPROVED BY 0 1 2 22 3 3 3 TOL 4 4 23 4 232 22 5 0 42 4 2 3617 8 9 8 8 2 ...
Page 68: ... APPROVED BY 0 1 2 22 3 3 3 TOL 4 4 23 4 232 22 3 242 4 2 32 2 3516 7 8 7 7 9 2 3 42 4 2 ...
Page 72: ......
Page 74: ......
Page 76: ......
Page 77: ......
Page 78: ......
Page 79: ......
Page 80: ...Drawings Part B General Arrangement and Wiring ...
Page 81: ......
Page 82: ......
Page 83: ......
Page 84: ......
Page 85: ......
Page 86: ......
Page 87: ......
Page 88: ......
Page 89: ......
Page 90: ......
Page 91: ......
Page 92: ......
Page 93: ......
Page 94: ......
Page 95: ......
Page 96: ... Appendix 4 RCI System Crane Configuration Sheet Duty Listing XQFWLRQ RGHV ...
Page 97: ......