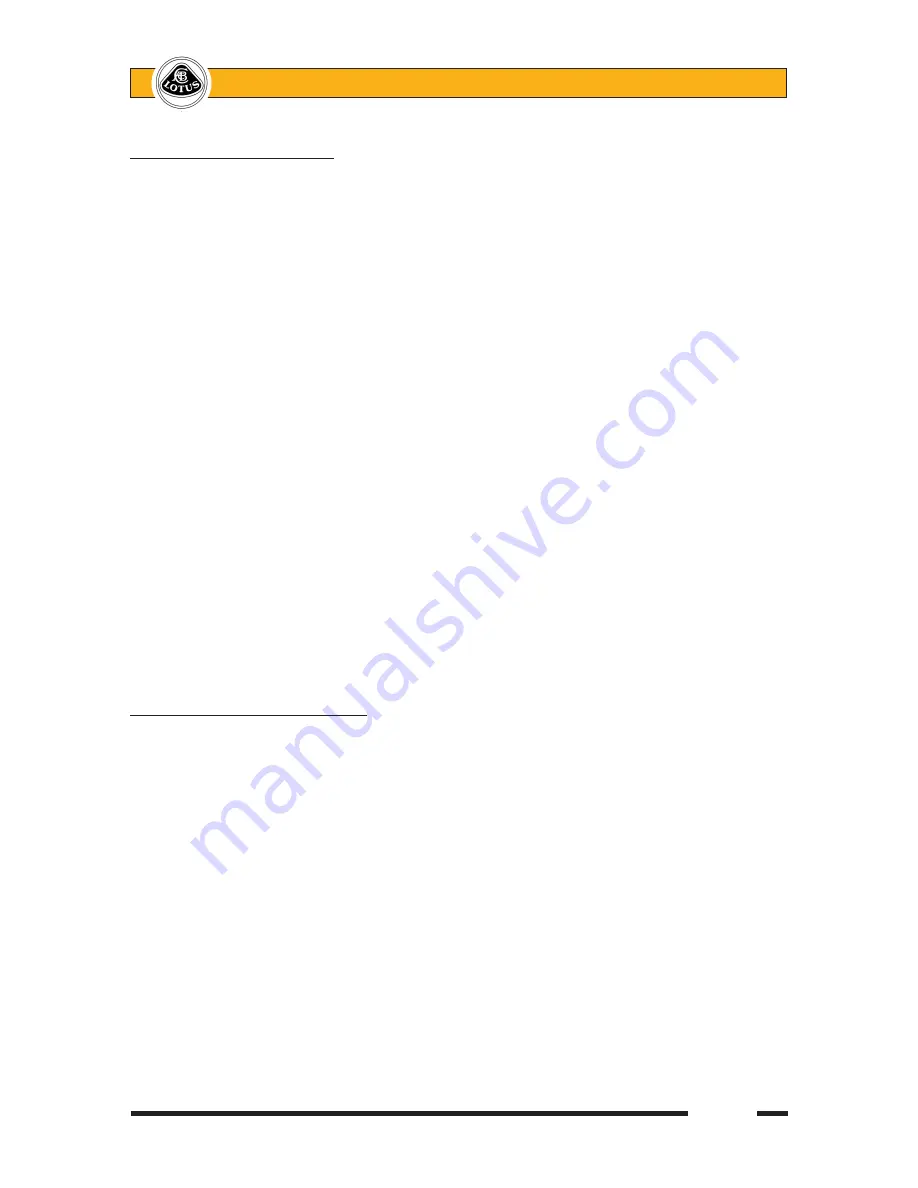
Page 3
Lotus Service Notes
Section CK
CK.1 - GENERAL DESCRIPTION
The independent front suspension comprises, on each side of the car, upper and lower forged aluminium
wishbones, a concentric coil spring/telescopic damper unit, and a tubular anti-roll bar. A forged steel hub car-
rier, provides a mounting for the hub bearing unit to which the 5-bolt road wheel and brake disc are attached,
and also features an integral steering arm and mounting bosses for the brake caliper.
The primary, vehicle weight bearing, lower wishbone, is braced by two integral struts and features an in-
tegrated steering swivel lower ball joint, a pair of press fit bonded rubber pivot bushes, and attachment points
for a fabricated steel bracket carrying the damper lower end, and a forged steel bracket for the anti-roll bar
drop link. The upper wishbone is a simple open 'A' frame, into the apex of which the upper steering swivel ball
joint is integrated.
The inboard ends of both wishbones use replaceable bonded rubber pivot bushes for maintenance free
articulation, with a compliance profile tuned to provide the vehicle with accurate and responsive dynamic char-
acteristics. Eccentric cams incorporated at the front and rear pivot points for the lower wishbone, provide for
the adjustment of both camber and castor.
The bottom of the Bilstein monotube telescopic damper fixes to the lower wishbone via a folded steel
cradle bolted to both arms of the wishbone, with the damper top end fixing to the subframe via a substantial
alloy casting bolted to the subframe longeron. The damper uses a bonded rubber bush in the top eye for noise
suppression, and a through bolted spherical steel joint in the lower eye for optimum dynamic response, and is
orientated with the damper rod uppermost. The dual rate concentric coil spring abuts against a lower seat on
the damper body, and a rubber cushioned upper seat incorporated in the damper top mounting bracket, thus
relieving the damper top bush from vehicle weight to the benefit of noise and ride refinement. The dual rate
coil spring is mounted with the close coiled end lowermost.
A 28mm o.d. tubular steel anti-roll bar is mounted in rubber bushes to the underside of the subframe and
projects through the lower wishbone before connecting to the wishbone rear leg via a short ball jointed drop
link and a forged steel bracket.
The hub bearing unit, which is common to all four wheels, is fixed to the hub carrier by 4 bolts, and in-
corporates a double row ball bearing with the inner race of the outboard bearing formed directly in the hub
forging, and the inner race of the inboard bearing retained by a swaging operation on the hub flange. Inboard
and outboard grease seals are included in the assembly, with a vehicle speed sensor ring integrated into the
inboard seal, whose 48 pole signal is picked up by a sensor mounted in the rear of the hub carrier. This data
is used for the anti-lock brake, vehicle stability, engine management and speedometer functions.
CK.2 - GEOMETRY & ADJUSTMENTS
Provision is made for the adjustment of wheel alignment, camber and castor. Under normal service con-
ditions, no periodic scheduled check of the geometry is necessary, although a front wheel alignment check is
recommended when the front tyres are replaced. A full geometry check is required only after front suspension
component replacement, or if excessive tyre wear is evident, or if steering difficulties are manifest. Before
any measurements or adjustments are made it is essential first to set the vehicle to its ‘mid-laden’ ride height,
approximating to driver and passenger and a full tank of fuel. This will require the vehicle to be ballasted, or
pulled down on a ramp:
Type Independent. Upper and lower wishbone; co-
axial coil spring/telescopic damper; anti-roll bar.
Mid-laden ride height (2x75 kg occ full fuel tank) - set car to this height before measuring geometry:
- front 125 mm below front end of chassis siderail
- rear 147 mm below rear end of chassis siderail
Castor - optimum + 5.2°
- tolerance range + 5.0° to + 5.5°; max. side/side 0.3°
Camber - optimum - 0.3°
- tolerance range - 0.5° to - 0.2°; max. side/side 0.2°
Alignment - optimum Zero
- tolerance range 0.5 mm toe-out, to 0.5mm toe-in overall
Steering axis inclination 9.4° nominal
Summary of Contents for Evora
Page 13: ...Page 7 Lotus Service Notes Section AJ ...
Page 81: ... Lotus Service Notes Section EMR Page 9 EMR 3 COMPONENT LOCATION em239 O2 O2 O2 O2 2009 02 ...
Page 82: ...Page 10 Lotus Service Notes Section EMR em240 2009 02 ...
Page 115: ... Lotus Service Notes Section EMR Page 43 2009 02 ...
Page 116: ...Page 44 Lotus Service Notes Section EMR 2009 02 ...
Page 118: ...Page 46 Lotus Service Notes Section EMR 2009 02 ...
Page 184: ...Page 2 Lotus Service Notes Section JL GENERAL LAYOUT TBA ...
Page 207: ...Page 25 Lotus Service Notes Section JL ...
Page 233: ...Page 9 Lotus Service Notes Section MR Blank page ...
Page 259: ...Page 35 Lotus Service Notes Section MR ...
Page 260: ...Page 36 Lotus Service Notes Section MR ...
Page 261: ...Page 37 Lotus Service Notes Section MR ...
Page 262: ...Page 38 Lotus Service Notes Section MR ...
Page 263: ...Page 39 Lotus Service Notes Section MR ...
Page 264: ...Page 40 Lotus Service Notes Section MR ...
Page 265: ...Page 41 Lotus Service Notes Section MR ...
Page 266: ...Page 42 Lotus Service Notes Section MR ...
Page 267: ...Page 43 Lotus Service Notes Section MR ...
Page 268: ...Page 44 Lotus Service Notes Section MR ...
Page 269: ...Page 45 Lotus Service Notes Section MR ...
Page 270: ...Page 46 Lotus Service Notes Section MR ...
Page 271: ...Page 47 Lotus Service Notes Section MR ...
Page 272: ...Page 48 Lotus Service Notes Section MR ...
Page 273: ...Page 49 Lotus Service Notes Section MR ...
Page 274: ...Page 50 Lotus Service Notes Section MR ...
Page 275: ...Page 51 Lotus Service Notes Section MR ...
Page 276: ...Page 52 Lotus Service Notes Section MR ...
Page 277: ...Page 53 Lotus Service Notes Section MR ...
Page 278: ...Page 54 Lotus Service Notes Section MR ...
Page 279: ...Page 55 Lotus Service Notes Section MR ...
Page 280: ...Page 56 Lotus Service Notes Section MR ...
Page 281: ...Page 57 Lotus Service Notes Section MR ...
Page 282: ...Page 58 Lotus Service Notes Section MR ...
Page 283: ...Page 59 Lotus Service Notes Section MR ...
Page 284: ...Page 60 Lotus Service Notes Section MR ...
Page 285: ...Page 61 Lotus Service Notes Section MR ...
Page 286: ...Page 62 Lotus Service Notes Section MR ...
Page 287: ...Page 63 Lotus Service Notes Section MR ...
Page 288: ...Page 64 Lotus Service Notes Section MR ...
Page 289: ...Page 65 Lotus Service Notes Section MR ...
Page 290: ...Page 66 Lotus Service Notes Section MR ...
Page 291: ...Page 67 Lotus Service Notes Section MR ...
Page 292: ...Page 68 Lotus Service Notes Section MR ...
Page 293: ...Page 69 Lotus Service Notes Section MR ...
Page 294: ...Page 70 Lotus Service Notes Section MR ...
Page 295: ...Page 71 Lotus Service Notes Section MR ...
Page 296: ...Page 72 Lotus Service Notes Section MR ...
Page 297: ...Page 73 Lotus Service Notes Section MR ...
Page 298: ...Page 74 Lotus Service Notes Section MR ...
Page 299: ...Page 75 Lotus Service Notes Section MR ...
Page 300: ...Page 76 Lotus Service Notes Section MR ...
Page 301: ...Page 77 Lotus Service Notes Section MR ...
Page 302: ...Page 78 Lotus Service Notes Section MR ...
Page 303: ...Page 79 Lotus Service Notes Section MR ...
Page 304: ...Page 80 Lotus Service Notes Section MR ...
Page 305: ...Page 81 Lotus Service Notes Section MR ...
Page 306: ...Page 82 Lotus Service Notes Section MR ...
Page 307: ...Page 83 Lotus Service Notes Section MR ...
Page 336: ...Page 2 Lotus Service Notes Section QJ GENERAL LAYOUT Illustration TBA ...
Page 357: ...Page 2 Lotus Service Notes Section WF Illustration to follow ...