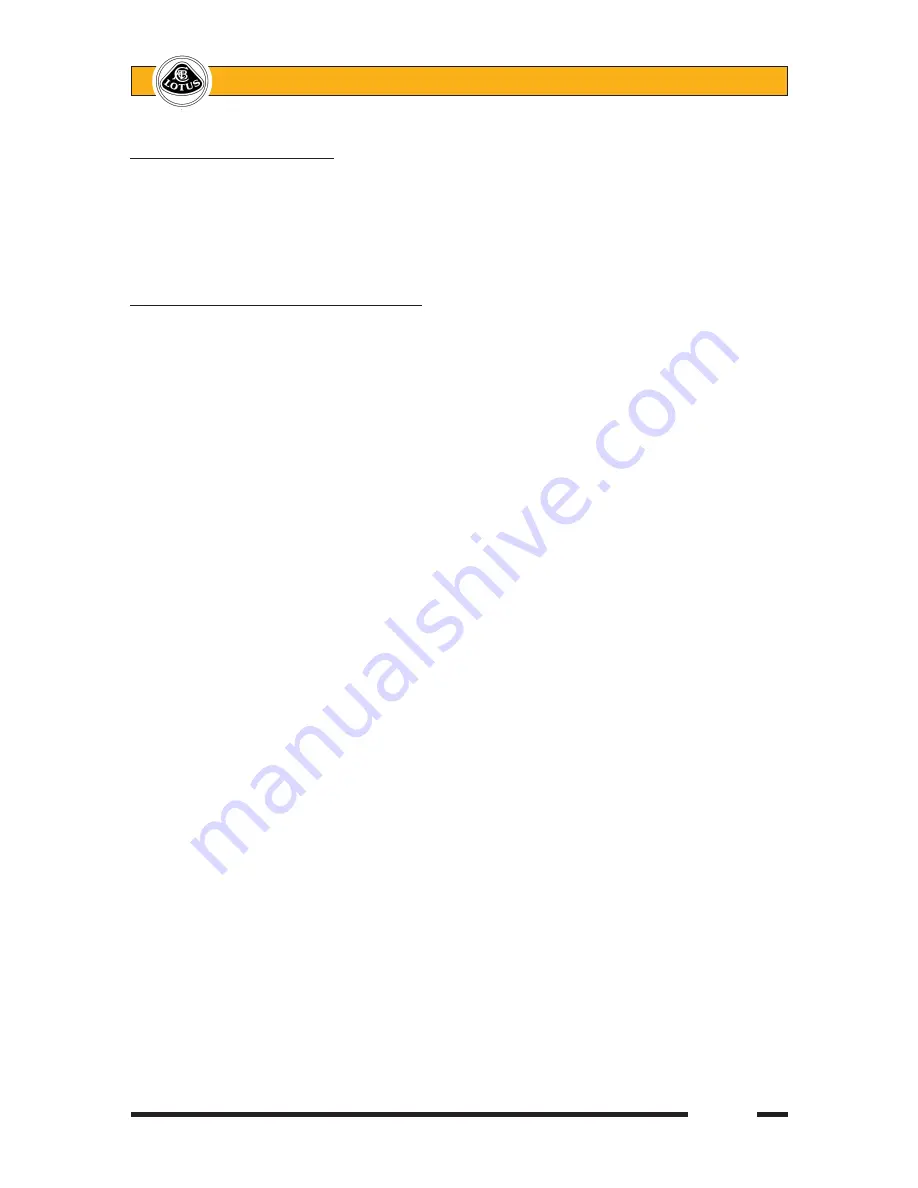
Page 3
Lotus Service Notes
Section BU
BU.1 - GENERAL DESCRIPTION
The body panels of the Lotus Evora are constructed of composite materials, and contribute to the overall
stiffness of the body/chassis structure. The panels are attached to the aluminium chassis and/or other body
panels either by elastomeric polyurethane adhesive, where maximum structural integrity is required, or by
threaded fasteners, where ease of service access and repair is the greater priority. The windscreen frame
incorporates foam cores to create closed box sections for optimum strength and lightness.
BU.2 - LOTUS COMPOSITE BODY FEATURES
Composite structures have the ability to absorb high impact loads by progressive collapse, with impact
damage being localised. In vehicle accidents this feature protects the occupants from injurious shock loads and
greatly reduces the danger of entrapment by deformation of steel body panels. This behaviour also facilitates
repair either by replacing the damaged bonded or bolt on panels, and/or integrating a replacement section
with the undamaged area, using recognised approved methods which restore the panel to its original condition
without residual strain or distortion.
The manufacturing process enables the thickness of composite mouldings to be varied in order to pro vide
efficient structures of high strength and low weight. Composites will not corrode, so the strength of compos-
ite components is retained regardless of age, unless physical damage is sustained. On the Evora, the body
construction features a safety cell around the cabin, comprising an assembly of body panels bonded to the
chassis and to each other to provide maximum occupant protection combined with light weight. Both ahead of,
and behind the cabin, body panels are screw fixed to permit easy removal for access to chassis or powertrain
components, or to allow simple and economic accident repair.
A composite panel may return to its original shape after deflection, but beyond a certain level of flexibility,
such treatment may result in the formation of surface cracks which may not be immediately apparent due to
the masking effect of the paint film. A steel panel similarly treated would become dented or deformed. The
cracking may be confined to the surface layer with no reduction in panel strength, but if the damage is more
severe the composite structure below the surface may be weakened. Localised repairs can be made in either
case. Possible causes of surface cracking include:
-
Vehicle collision;
-
Inappropriately sitting, leaning heavily or pushing on the body or any composite panel;
-
Knocking doors against obstructions when opening;
-
Dropping or striking objects against a panel, including footballs and other wayward missiles;
-
Unrestrained items in the luggage compartment striking the inside of the rear body;
-
Attempting to close the tailgate onto projecting luggage or tools
-
Applying excessive force to parts attached to composite panels e.g. mirrors, handles and locks (inc. action
by vandals).
-
Incorrect jacking, or panel removal procedures.
The composite body panels of the Evora are manufactured by one of several processes dependent on
the requirements of the panel concerned:
-
All visible external panels, where surface quality is a priority, are produced by Injection Compression System
Resin Transfer Moulding (ICSRTM), whereby glass fibre mat cut to shape and preformed when necessary,
is placed in a heated, chrome steel surfaced, closed mould, into which polyester resin is injected. After
filling, the gap between the two halves of the mould is then reduced in order to compress the moulding
and ensure complete material flow and consistent structural quality. Panel thickness varies according to
strength/weight requirement. The special 'low profile' resin used ensures minimum shrinkage during the
curing process, in order to provide the optimum surface finish.
-
For less visible components, including the rear bulkhead, battery box, boot box and some reinforcement
panels, a Resin Transfer Moulding process is used with standard polyester resin injected at low pressure
into a double sided closed tool containing dry and preformed composite material.
-
For panels with a relatively simple shape and a low structural requirement, a Sheet Moulding Compound
(SMC) process is used, whereby a pad of material impregnated with resin is placed in a closed tool which
applies heat and a low compression to the moulding. A panel of high surface quality is produced, requiring
only a minimum of fettling operations.
Summary of Contents for Evora
Page 13: ...Page 7 Lotus Service Notes Section AJ ...
Page 81: ... Lotus Service Notes Section EMR Page 9 EMR 3 COMPONENT LOCATION em239 O2 O2 O2 O2 2009 02 ...
Page 82: ...Page 10 Lotus Service Notes Section EMR em240 2009 02 ...
Page 115: ... Lotus Service Notes Section EMR Page 43 2009 02 ...
Page 116: ...Page 44 Lotus Service Notes Section EMR 2009 02 ...
Page 118: ...Page 46 Lotus Service Notes Section EMR 2009 02 ...
Page 184: ...Page 2 Lotus Service Notes Section JL GENERAL LAYOUT TBA ...
Page 207: ...Page 25 Lotus Service Notes Section JL ...
Page 233: ...Page 9 Lotus Service Notes Section MR Blank page ...
Page 259: ...Page 35 Lotus Service Notes Section MR ...
Page 260: ...Page 36 Lotus Service Notes Section MR ...
Page 261: ...Page 37 Lotus Service Notes Section MR ...
Page 262: ...Page 38 Lotus Service Notes Section MR ...
Page 263: ...Page 39 Lotus Service Notes Section MR ...
Page 264: ...Page 40 Lotus Service Notes Section MR ...
Page 265: ...Page 41 Lotus Service Notes Section MR ...
Page 266: ...Page 42 Lotus Service Notes Section MR ...
Page 267: ...Page 43 Lotus Service Notes Section MR ...
Page 268: ...Page 44 Lotus Service Notes Section MR ...
Page 269: ...Page 45 Lotus Service Notes Section MR ...
Page 270: ...Page 46 Lotus Service Notes Section MR ...
Page 271: ...Page 47 Lotus Service Notes Section MR ...
Page 272: ...Page 48 Lotus Service Notes Section MR ...
Page 273: ...Page 49 Lotus Service Notes Section MR ...
Page 274: ...Page 50 Lotus Service Notes Section MR ...
Page 275: ...Page 51 Lotus Service Notes Section MR ...
Page 276: ...Page 52 Lotus Service Notes Section MR ...
Page 277: ...Page 53 Lotus Service Notes Section MR ...
Page 278: ...Page 54 Lotus Service Notes Section MR ...
Page 279: ...Page 55 Lotus Service Notes Section MR ...
Page 280: ...Page 56 Lotus Service Notes Section MR ...
Page 281: ...Page 57 Lotus Service Notes Section MR ...
Page 282: ...Page 58 Lotus Service Notes Section MR ...
Page 283: ...Page 59 Lotus Service Notes Section MR ...
Page 284: ...Page 60 Lotus Service Notes Section MR ...
Page 285: ...Page 61 Lotus Service Notes Section MR ...
Page 286: ...Page 62 Lotus Service Notes Section MR ...
Page 287: ...Page 63 Lotus Service Notes Section MR ...
Page 288: ...Page 64 Lotus Service Notes Section MR ...
Page 289: ...Page 65 Lotus Service Notes Section MR ...
Page 290: ...Page 66 Lotus Service Notes Section MR ...
Page 291: ...Page 67 Lotus Service Notes Section MR ...
Page 292: ...Page 68 Lotus Service Notes Section MR ...
Page 293: ...Page 69 Lotus Service Notes Section MR ...
Page 294: ...Page 70 Lotus Service Notes Section MR ...
Page 295: ...Page 71 Lotus Service Notes Section MR ...
Page 296: ...Page 72 Lotus Service Notes Section MR ...
Page 297: ...Page 73 Lotus Service Notes Section MR ...
Page 298: ...Page 74 Lotus Service Notes Section MR ...
Page 299: ...Page 75 Lotus Service Notes Section MR ...
Page 300: ...Page 76 Lotus Service Notes Section MR ...
Page 301: ...Page 77 Lotus Service Notes Section MR ...
Page 302: ...Page 78 Lotus Service Notes Section MR ...
Page 303: ...Page 79 Lotus Service Notes Section MR ...
Page 304: ...Page 80 Lotus Service Notes Section MR ...
Page 305: ...Page 81 Lotus Service Notes Section MR ...
Page 306: ...Page 82 Lotus Service Notes Section MR ...
Page 307: ...Page 83 Lotus Service Notes Section MR ...
Page 336: ...Page 2 Lotus Service Notes Section QJ GENERAL LAYOUT Illustration TBA ...
Page 357: ...Page 2 Lotus Service Notes Section WF Illustration to follow ...