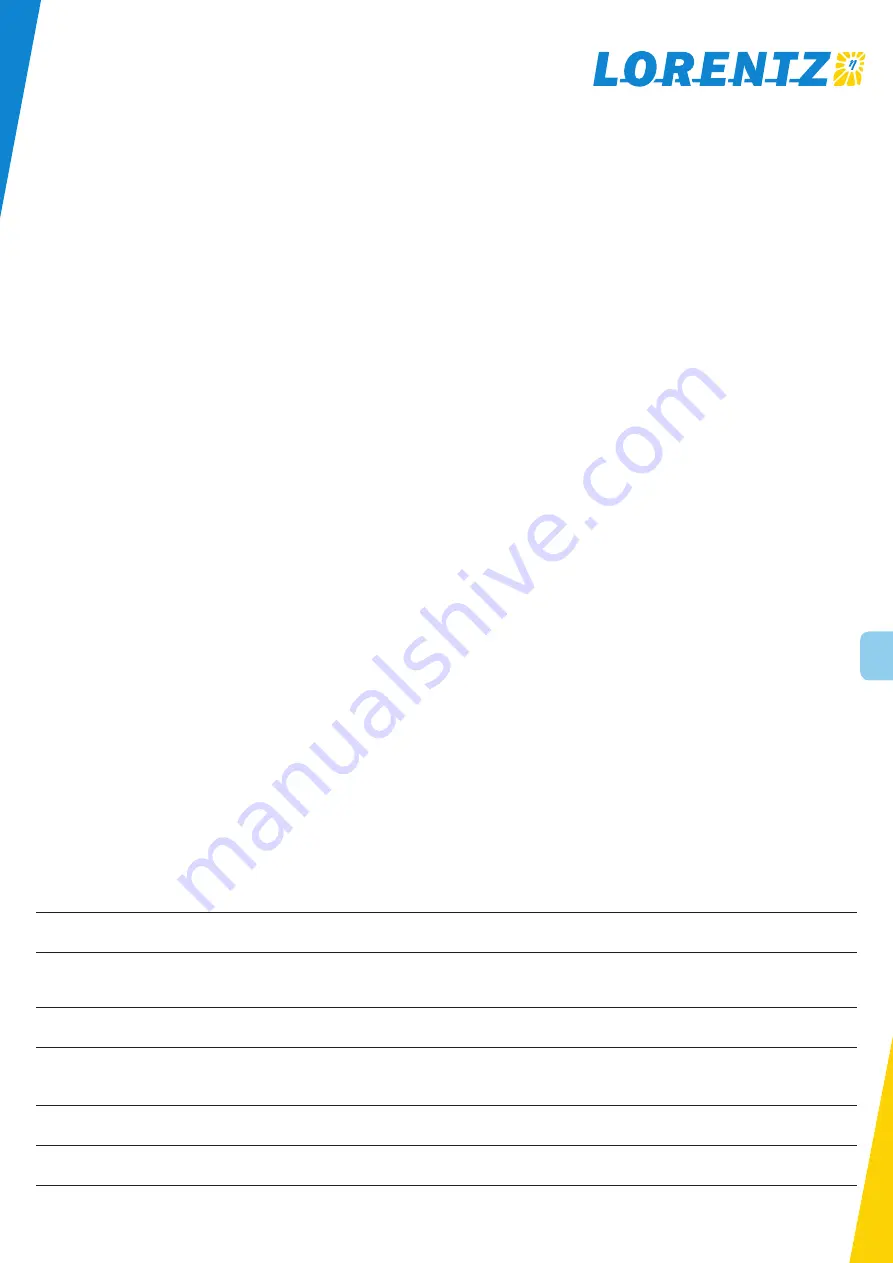
v140822
Sun. Water.
Life.
BERNT LORENTZ GmbH & Co. KG
Kroegerskoppel 7, 24558 Henstedt-Ulzburg, Germany, Tel. +49 (0) 4193 7548 - 0, Fax - 29,
www.lorentz.de
All specifi cations and information are given with good intent, errors are possible and products may be subject to change without notice. Pictures may
differ from actual products depending on local market requirements and regulations.
22
6 Service and Maintenance
6 1 Routine Inspection and Maintenance
Affected by ambient temperature, humidity, dust, vibration
and internal device aging of the controller, problems might
occur during operation. To make the controller run stably, a
periodic inspection must be performed
every year
.
Requirement of Inspection and Maintenance
1.
The inspection must be performed by professional
technical personnel.
2.
Before working on the controller, always cut off the
power supply and wait, until the display turns off.
3.
Avoid leaving any metal components in the
controller, or else they might cause damage to the
equipment.
4.
An electric insulation test has been made on the con-
troller before it has left factory. A withstand-voltage
test is not necessary.
5.
It is forbidden to use the megohmmeter to test in the
control circuit.
6.
When conducting insulation test on the motor, you
have to disconnect the connection between motor
and controller.
Main Points for Inspection and Maintenance
Please use the controller under environment recommended
by this manual. Inspect and maintain as per the following
table.
Inspect frequency
regular
Inspection item
Inspection content
Judgment standard
√
running environment
1.
temperature, humidity
2.
dust, gas
1.
temperature <50 °C
2.
humidity < 90 %, no dew condensation, no peculiar smell,
flammable, explosive gas
√
cooling system
1.
installation environment
2.
radiator
1.
excellent ventilation in installation environment
2.
radiator air duct not blocked
√
controller body
1.
vibration, temperature rise
2.
noise
3.
lead, terminal
1.
stable vibration, normal temperature of the shell
2.
no abnormal noise and peculiar smell
3.
fastening screws not loose
√
motor
1.
vibration, temperature rise
2.
noise
1.
steady running and normal tempera-ture
2.
no abnormal and uneven noise
√
input and output parameter
1.
input voltage
2.
output current
1.
input voltage in the specified scope
2.
output current under the rated value
6 2 Replacement of Wear Parts
Filter Capacitor
Pulsating current of the main circuit will influence the
performance of the aluminum electrolytic filter capacitor, of
which the degree will depend on the ambient tempera-
ture and application condition. The Controller used under
normal condition should replace its electrolytic capacitor
every 10 years. When the filter capacitor’s electrolyte is
leaking, safety valve bursting out or the capacitor main
body expanding, replace it immediately.
Cooling Fan
Cooling fan’s service life is about 15.000 hours. If the fan
appears abnormal noise or produces vibration, replace it
immediately.