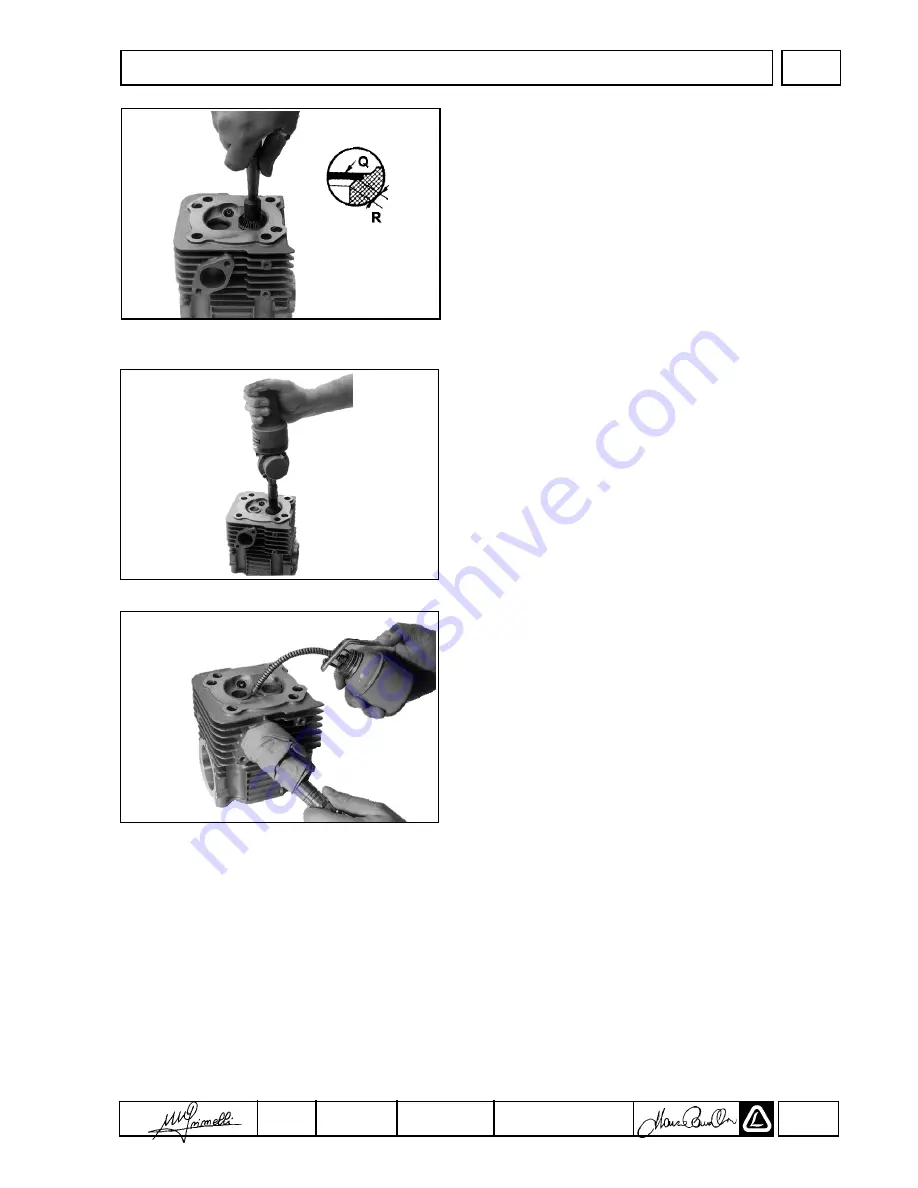
COMPILER TECO/ATL
REG. CODE
1-5302-528
MODEL N°
50805
DATE OF ISSUE
31.07.2001
REVISION
00
ENDORSED
DATE
31.07.2001
21
VIII
DISASSEMBLY/REASSEMBLY
VALVE SEATS
The special high nickel-chromium alloy content cast iron valve seats
are particularly resistant to the heat caused by combustion.
For grinding, use a tapered milling cutter:
88° exhaust - 88° intake for engine LGA 280 OHC
88° exhaust- 120° intake for engine LGA 340 OHC
N.B.: Valve seats with angles of 90° (exhaust) and 120° (intake) will be
used in the LGA 280 OHC too. Please check technical informative
sheet for introdution date.
Following prolonged engine operation, the hammering of the
valves on the seats, at high temperatures, hardens the track P
(fig.8) making manual grinding impossible. The hardened surface
must be removed using a grinder fitted on a seat refacer. The final
accommodation may be carried out with a manual cutter, as
previously described (fig.8).
Valve seat grinding will lead to the enlarging of trace R that faces
the valve on the seat. lf R is wider than 2 mm, using an inverted
cutter, lower the face Q (fig. 12) until the R measurement is
between: 1.3-1.5 mm
The final accommodation of the valve in the seat should be carried
out by spreading a layer of fine grain lapping paste in the seat and
rotating the valve, using slight pressure and an alternating
movement, until the surfaces are perfectly set (fig. 13).
Wash the valve and seat thoroughly with oil or petrol to eliminate all
traces of lapping paste or shavings.
To check the efficiency of the seal between the valve and seat, once
lapping is terminated, proceed as follows:
1) Fit the valve on the head with the spring and cotters.
2) Pour a few drops of diesel fuel or oil around the edge of the valve head.
3) Direct compressed air inside the duct (intake/exhaust), taking care
to plug the edges of the duct in order to avoid air leakage (fig.14).
lf air infiltration causes bubbles to form between the seat and the valve,
disassemble the valve and correct the seat grinding.
The test can also be carried out by pushing the valve upward in the seat
and then allowing it to return freely. lf the recoil is both substantial and
uniform, even when manually rotating the valve, this means that the
accommodation is satisfactory. lf not, continue the lapping operation
until the aforementioned conditions have been achieved.
lf the seat needs to be replaced, proceed as follows:
1) Using a 2-3 mm drill bit, drill holes on the seat, completing the cut with a chisel, without damaging the housing.
2) Extract the seat.
3) Heat the head to a temperature of between 160°-180° degrees C.
4) Introduce the new seat using the press.
It is advised that this type of operation is carried out at specialized workshops.
12
13
14