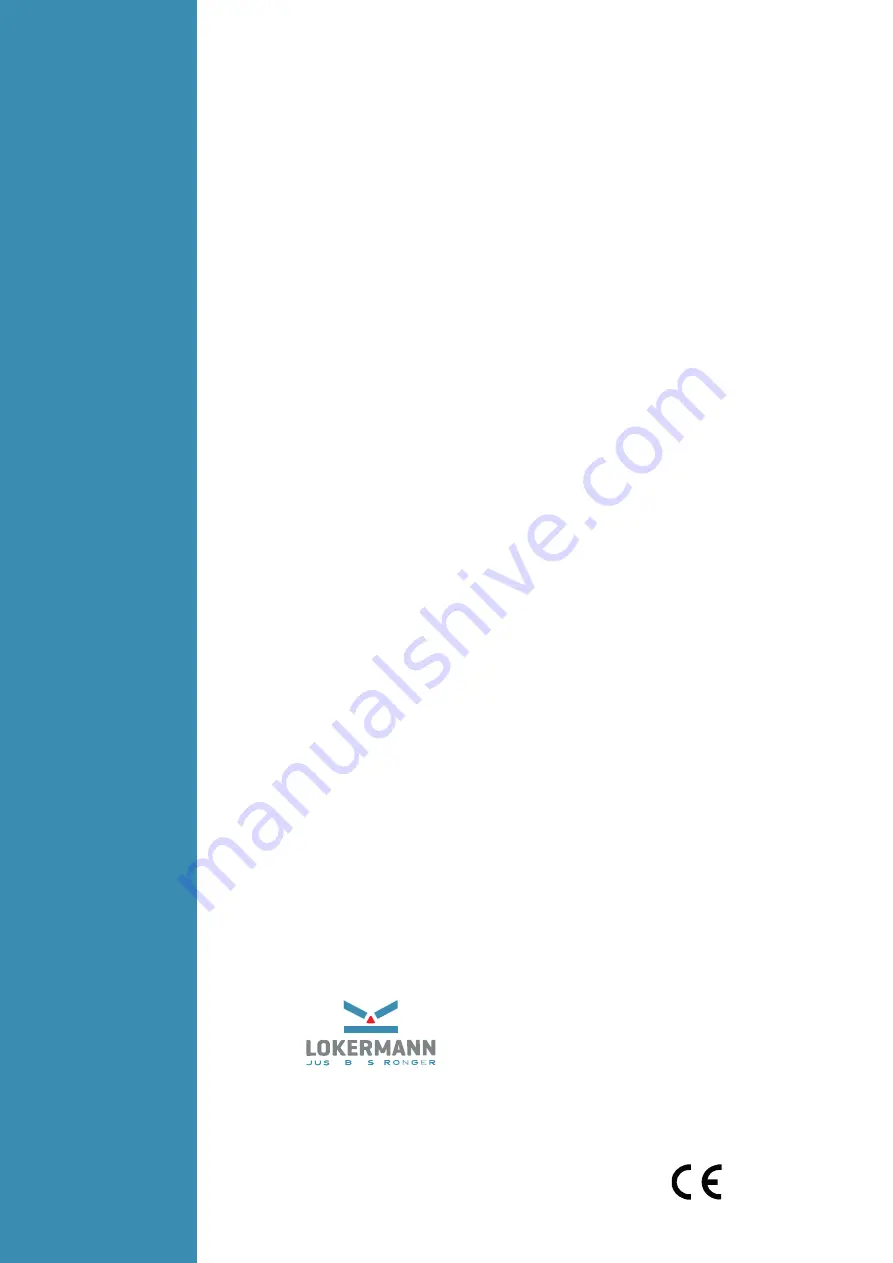
LOKERMANN Srl,
Via Produzione 16/18, 37044, Cologna Veneta,
(VR)-Italy, Tel: +39 0442 1722469
[email protected] - www.lokermann.eu
LOKERMANN Srl,
Via Produzione 16/18, 37044, Cologna Veneta,
(VR)-Italy, Tel: +39 0442 1722469
[email protected] - www.lokermann.eu