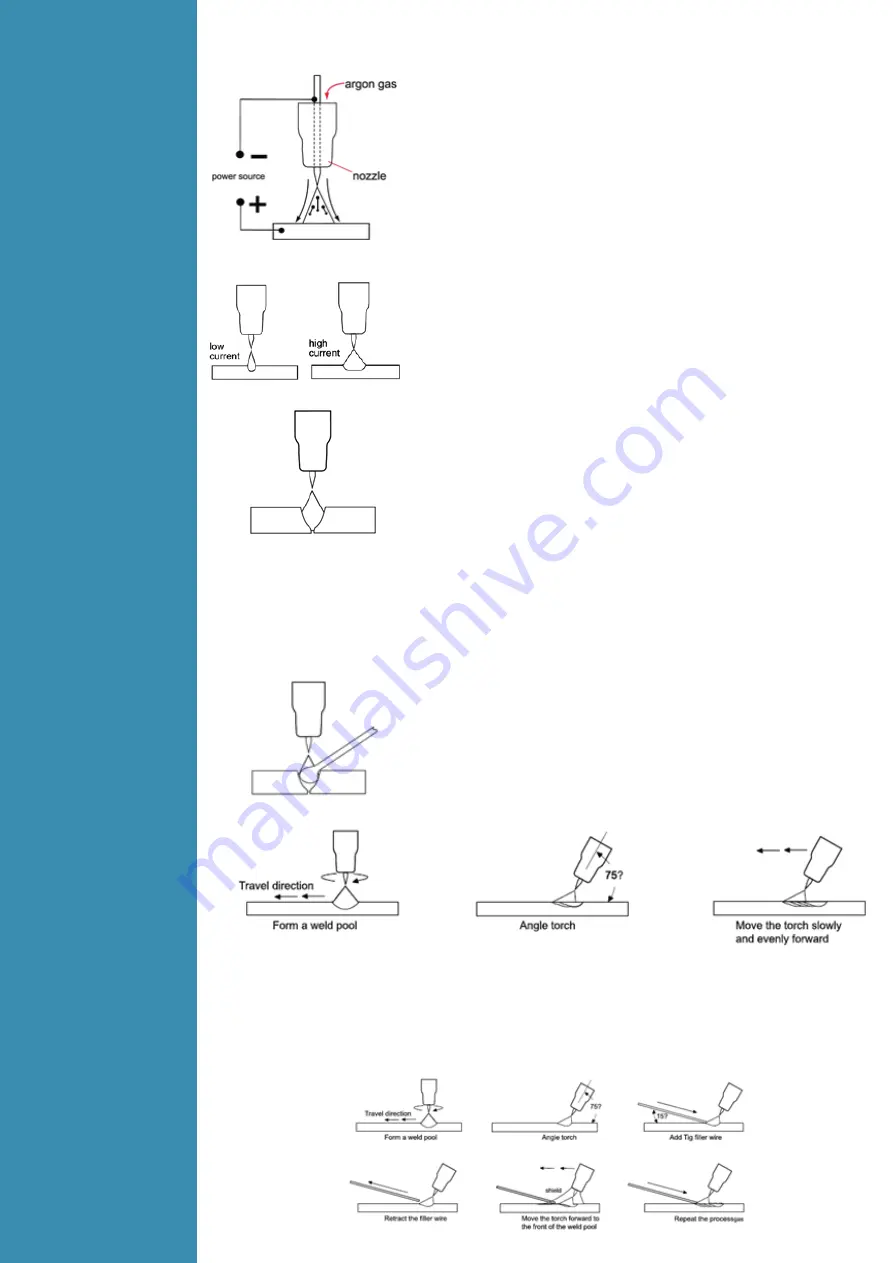
3.4.4
Tig
Welding
Techniques
DC TIG welding is a process in which an arc is struck between a
TUNGSTEN electrode and the metal work piece. The weld area is
shielded by an inert gas flow to prevent contamination of the tungsten,
molten pool and weld area. When the TIG arc is struck the inert gas is
ionized and superheated changing it’s molecular structure which
converts it into a plasma stream. This plasma stream flowing between
the tungsten and the work piece is the TIG arc and can be as hot as
19,000°C. It is a very pure and concentrated arc which provides the
controlled melting of most metals into a weld pool. TIG welding offers
the user the greatest amount of flexibility to weld the widest range of
material and thickness and types. DC TIG welding is also the cleanest
weld with no sparks or spatter.
The intensity of the arc is proportional to the current that flows from the
tungsten. The welder regulates the welding current to adjust the power
of the arc. Typically thin material requires a less powerful arc with less
heat to melt the material so less current (amps) is required, thicker
material requires a more powerful arc with more heat so more current
(amps) are necessary to melt the material.
TIG Welding Fusion Technique
Manual TIG welding is often considered the most difficult of all the
welding processes. Because the welder must maintain a short arc length,
great care and skill are required to prevent contact between the
electrode and the work piece. Similar to Oxygen Acetylene torch
welding, Tig welding normally requires two hands and in most instances
requires the welder to manually feed a filler wire into the weld pool with
one hand while manipulating the welding torch in the other.
However, some welds combining thin materials can be accomplished without filler metal like edge,
corner, and butt joints. This is known as Fusion welding where the edges of the metal pieces are melted
together using only the heat and arc force generated by the TIG arc. Once the arc is started the torch
tungsten is held in place until a weld pool is created, a circular movement of the tungsten will assist is
creating a weld pool of the desired size. Once the weld pool is established tilt the torch at about a 75°
angle and move smoothly and evenly along the joint while fusing the materials together.
TIG Welding with Filler Wire Technique
It is necessary in many situations with TIG welding to add a filler wire into
the weld pool to build up weld reinforcement and create a strong weld.
Once the arc is started the torch tungsten is held in place until a weld
pool is created, a circular movement of the tungsten will assist is creating
a weld pool of the desired size. Once the weld pool is established tilt the
torch at about a 75° angle and move smoothly and evenly along the
joint. The filler metal is introduced to the leading edge of the weld pool.
The filler wire is usually held at about a 15° angle and fed into the leading edge of the molten pool,
the arc will melt the filler wire into the weld pool as the torch is moved forward. Also a dabbing
technique can be used to control the amount of filler wire added, the wire is fed into the molten pool
and retracted in a repeating sequence as the torch is moved slowly and evenly forward. It is important
during the welding to keep the molten end of the filler wire inside the gas shield as this protects the end
of the wire from being oxidised and contaminating the weld pool.