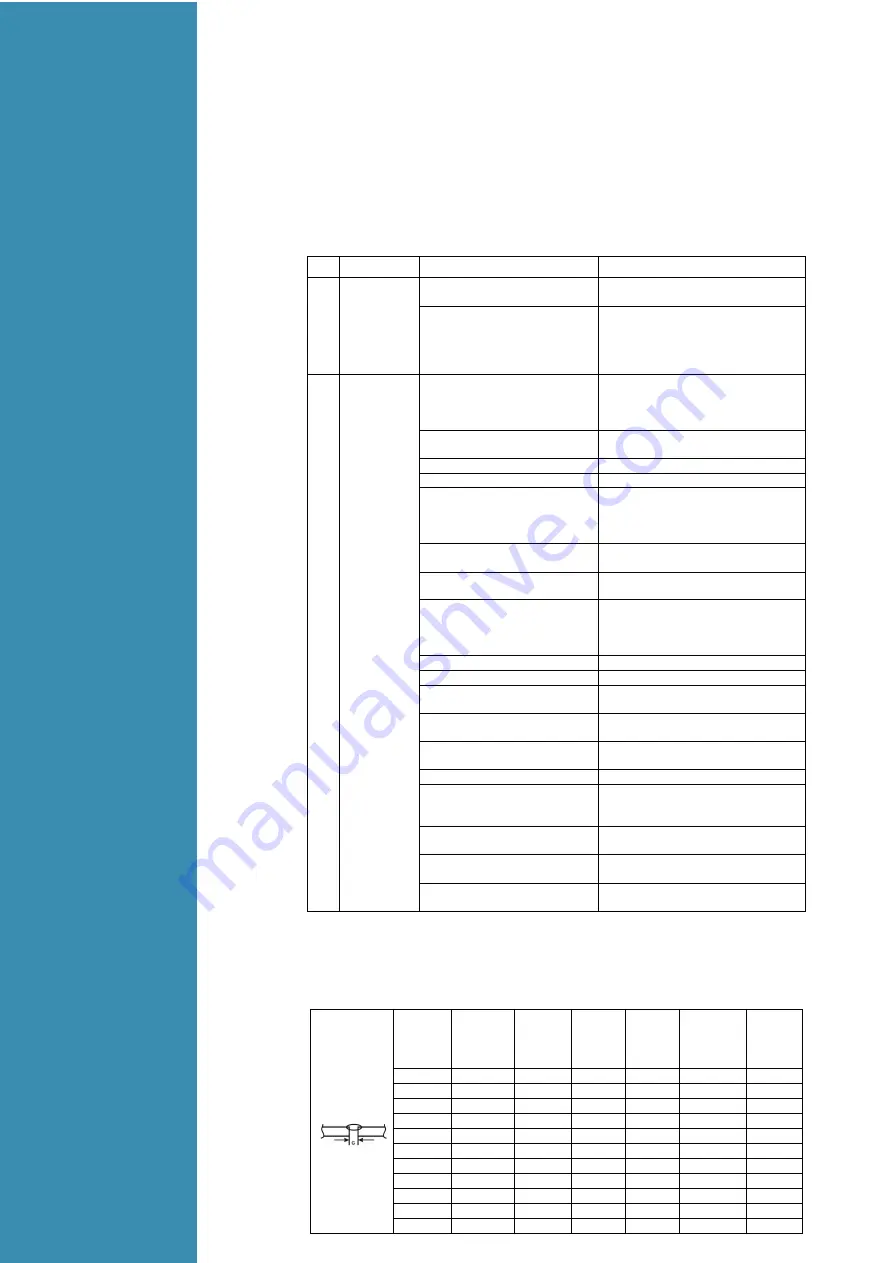
3.6.2
MIG wire
feed
trouble
shooting
The following chart addresses some of the common WIRE FEED problems during MIG welding. In all
cases of equipment malfunction, the manufacturer’s recommendations should be strictly adhered
to and followed.
NO. Trouble
Possible Reason
Suggested Remedy
1
No wire feed
Wrong mode selected
Check that the TIG/MMA/MIG selector
switch set to MIG position
Wrong torch selector switch
Check that the Wire Feeder /Spool Gun
selector switch is set to Wire Feeder
position for MIG welding and Spool
Gun when using the Spool gun
2
Inconsistent /
interrupted
wire feed
Adjusting wrong dial
Be sure to adjust the wire feed and
voltage dials for MIG welding. The
amperage dial is for MMA and TIG
welding mode
Wrong polarity selected
Select the correct polarity for the wire
being used - see machine setup guide
Incorrect wire speed setting
Adjust the wire feed speed
Voltage setting incorrect
Adjust the voltage setting
Mig torch lead too long
Small diameter wires and soft wires like
aluminium don ’t feed well through long
torch leads - replace the torch with a
lesser length torch
Mig torch lead kinked or too
sharp angle being held
Remove the kink, reduce the angle or
bend
Contact tip worn, wrong size,
wrong type
Replace the tip with correct size and
type
Liner worn or clogged (the most
common causes of bad feeding)
Try to clear the liner by blowing out
with compressed air as a temporary
cure, it is recommended to replace the
liner
Wrong size liner
Install the correct size liner
Blocked or worn inlet guide tube
Clear or replace the inlet guide t ube
Wire misaligned in drive roller
groove
Locate the wire into the groove of the
drive roller
Incorrect drive roller size
Fit the correct size drive roller eg;
0.8mm wire requires 0.8mm drive roller
Wrong type of drive roller
selected
Fit the correct type roller (e.g. knurled
rollers needed for flux cored wires
Worn drive rollers
Replace the drive rollers
Drive roller pressure too high
Can flatten the wire electrode causing it
to lodge in the contact tip - reduce the
drive roller pressure
Too much tension on wire spool
hub
Reduce the spool hub brake tension
Wire crossed over on the spool or
tangled
Remove the spool untangle the wire or
replace the wire
Contaminated mig wire
Use clean dry rust free wire. Do not
lubricate the wire with oil, grease etc
3.7
Welding
parameters
Process reference for CO2 butt welding of low carbon steel solid welding wire
Butt-joint
Material
thickness
(MM)
Root gap
G (MM)
Wire
diameter
(MM)
Welding
current
(A)
Welding
voltage
(V)
Welding
speed
(CM/MIN)
Gas-
flow
rate
(L/MIN)
0.8
0
0.8
60-70 16-16.5
50-60
10
1.0
0
0.8
75-85 17-17.5
50-60
10-15
1.2
0
0.8
80-90
17-18
50-60
10-15
2.0
0-0.5
1.0/1.2 110-120 19-19.5
45-50
10-15
3.2
0-1.5
1.2
130-150 20-23
30-40
10-20
4.5
0-1.5
1.2
150-180 21-23
30-35
10-20
6
0
1.2
270-300 27-30
60-70
10-20
6
1.2-1.5
1.2
230-260 24-26
40-50
15-20
8
0-1.2
1.2
300-350 30-35
30-40
15-20
8
0-0.8
1.6
380-420 37-38
40-50
15-20
12
0-1.2
1.6
420-480 38-41
50-60
15-20
Summary of Contents for GRAND MIG 351 MULTI SYN
Page 33: ...4 4 Electrical schematic drawing DRIVER...
Page 35: ...4 2 Troublesho oting...