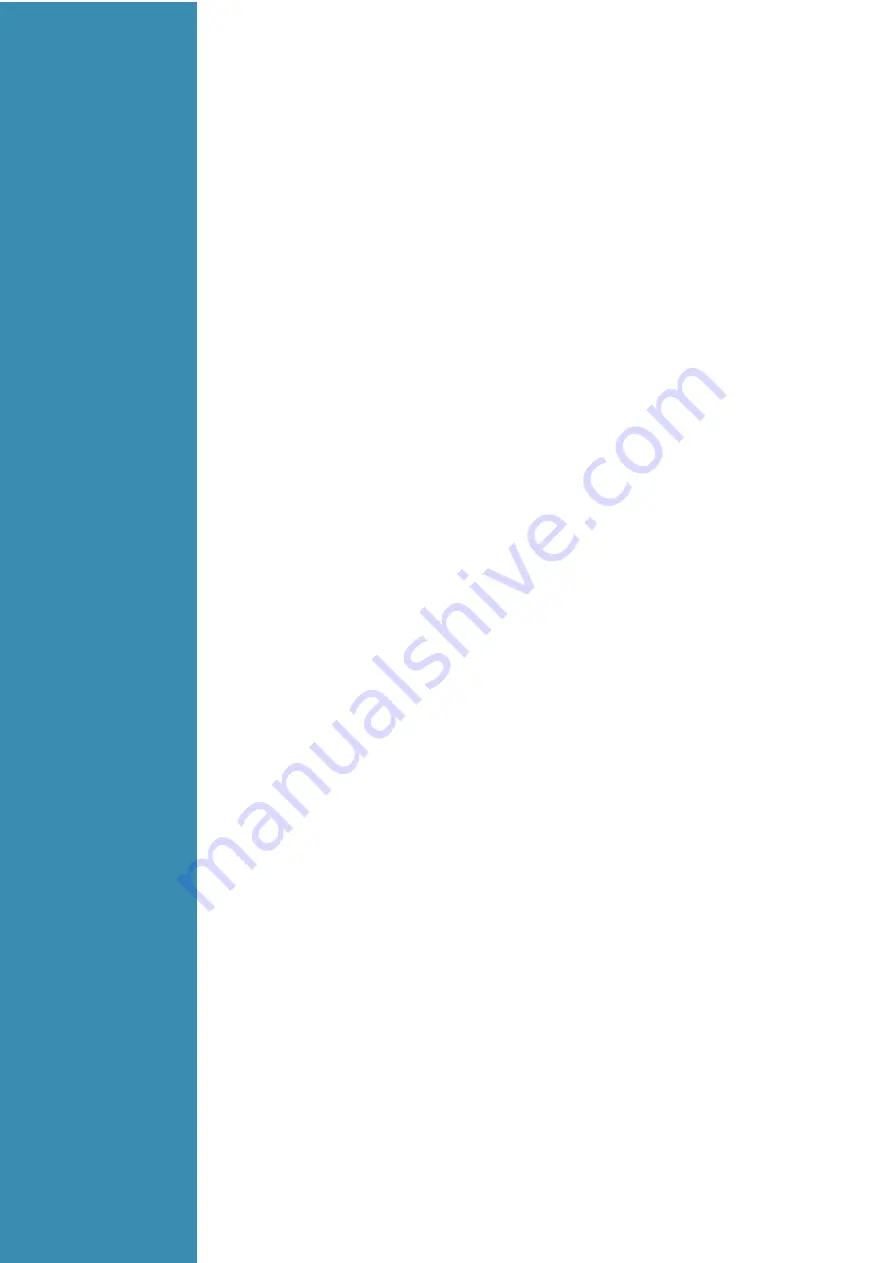
INSTALLATION WARNING
This machine is certified according to 60974-10:2014 Arc Welding Equipment Part 10: Electromagnetic
compatibility (EMC) requirement and the EUT belongs to Group 2 Class A.
WARNING: This Class A equipment is intended for industrial use and it is not intended for use in
residential locations where the elctrical power is provided by the public low-voltage supply system.
There may be potential difficulties in ensuring electromagnetic compatibility in those locations, due to
conducted as well as radiated disturbances.
WARNING: This equipment does not comply with IEC 61000-3-12. If it is connected to a public low-
voltage system, it is the responsability of the installer or user of the equipment to ensure, by consultation
with the distribution network operator if necessary, that the equipment may be connected.
Assessment of area
Before installing arc welding equipment the user shall make an assessment of potential
electromagnetic problems in the surrounding area. The following shall be taken into account:
a) other supply cables, control cables, signalling and telephone cables, above, below and
adjacent to the arc welding equipment;
b) radio and television transmitters and receivers;
c) computer and other control equipment;
d) safety critical equipment, for example guarding of industrial equipment;
e) the health of the people around, for example the use of pacemakers and hearing aids;
f) equipment used for calibration or measurement;
g) the immunity of other equipment in the environment. The user shall ensure that other
equipment being used in the environment is compatible. This may require additional
protection measures;
h) the time of day that welding or other activities are to be carried out.
The size of the surrounding area to be considered will depend on the structure of the building
and other activities that are taking place. The surrounding area may extend beyond the
boundaries of the premises.
Methods of reducing emissions-Public supply system
Arc welding equipment should be connected to the public supply system according to this manual
recommendations. If interference occurs, it may be necessary to takeadditional precautions such as
filtering of the public supply system. Consideration should be given to shielding the supply cable of
permanently installed arc welding equipment, in metallic conduit or equivalent. Shielding should be
electrically continuous throughout its length. The shielding should be connected to the welding power
source so that good electrical contact is maintained between the conduit and the welding power
source enclosure.
Maintenance of the arc welding equipment
The arc welding equipment should be routinely maintained according to this manual
recommendations. All access and service doors and covers should be closed and properly
fastened when the arc welding equipment is in operation. The arc welding equipment should
not be modified in any way, except for those changes and adjustments covered in this manaul. In
particular, the spark gaps of arc striking and stabilising devices
should be adjusted and maintained according to our recommendations.
Welding cables
The welding cables should be kept as short as possible and should be positioned close
together, running at or close to the floor level.
Equipotential bonding
Bonding of all metallic objects in the surrounding area should be considered. However,
metallic objects bonded to the work piece will increase the risk that the operator could receive
an electric shock by touching these metallic objects and the electrode at the same time. The
operator should be insulated from all such bonded metallic objects.
Earthing of the workpiece
Where the workpiece is not bonded to earth for electrical safety, nor connected to earth
because of its size and position, for example, ship’s hull or building steelwork, a connection
bonding the workpiece to earth may reduce emissions in some, but not all instances. Care should be
taken to prevent the earthing of the workpiece increasing the risk of injury to users or damage to other
electrical equipment. Where necessary, the connection of the workpiece to earth should be made by
a direct connection to the workpiece, but in some countries where direct connection is not permitted,
the bonding should be achieved by suitable capacitance, selected according to national regulations.
Screening and shielding
Selective screening and shielding of other cables and equipment in the surrounding area may
alleviate problems of interference. Screening of the entire welding area may be considered for
special applications.
Summary of Contents for GRAND MIG 351 MULTI SYN
Page 33: ...4 4 Electrical schematic drawing DRIVER...
Page 35: ...4 2 Troublesho oting...