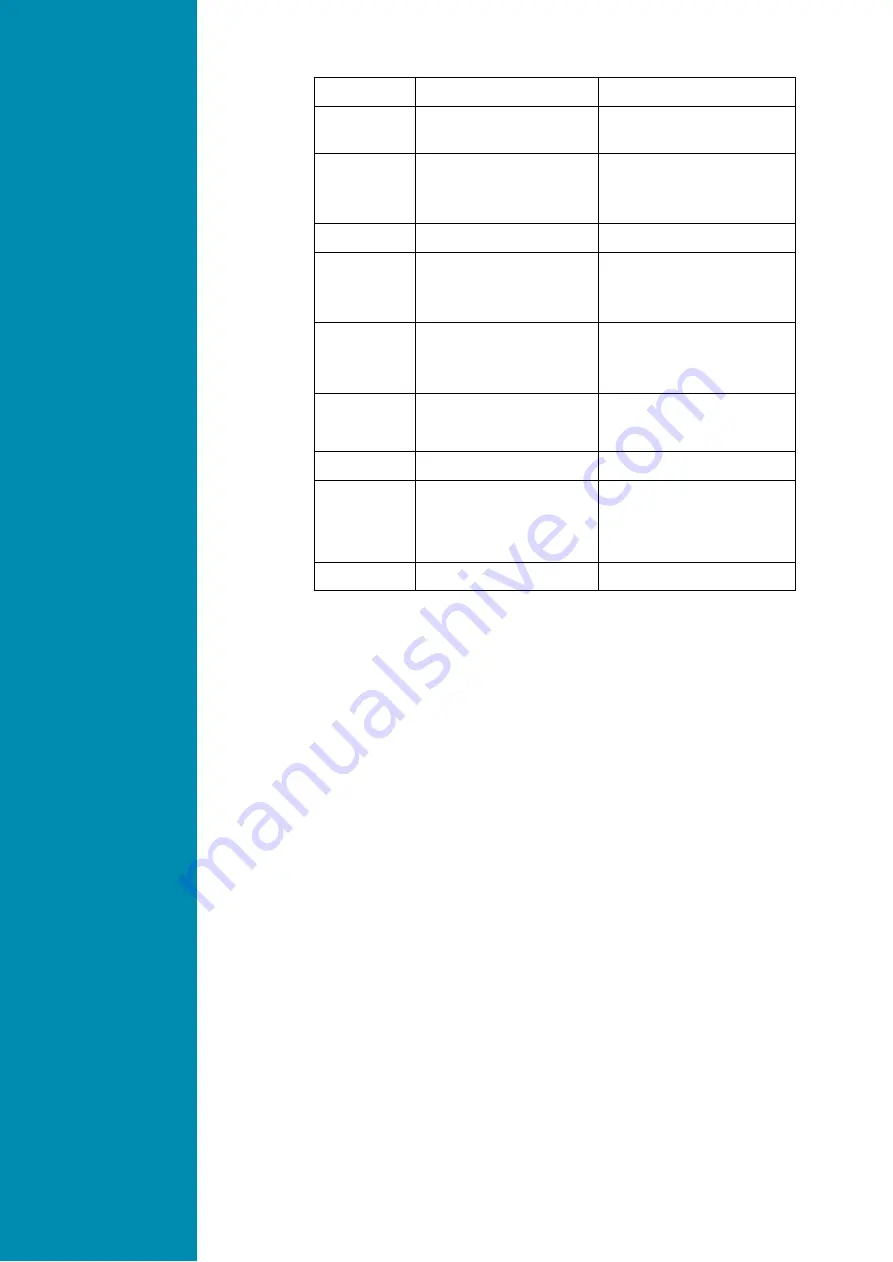
3.4
Troublesh-
ooting
Trouble
Possible Reason
Suggested Remedy
Torch will not come
on
1.Power switch OFF
2.Air supply is not of sufficient volume
or pressure
3. Work piece ground clamp not attached.
1.Turn power switch to the ON position
2. Check air supply
(5 Bar, 150 L/min)
3. Attach to work piece or to steel table with
work piece securely clamped to table
Sparks are shooting
upward instead of
down through the
material.
1.Plasma torch is not piercing the
material
2. Torch may be too far away from the
work piece
3. Material may not be earthed properly
4. Travel speed too fast
1. Increase current
2. Decrease the distance of your torch to the
work piece
3. Check connections for proper earth
4. Reduce speed
Beginning of cut not
completely pierced
Possible earth connection problem
Check all connections
Dross build-up on
parts of cuts
1. Tool/material building up heat
2. Cutting speed too slow or current too
high
3. Worn torch parts
1. Allow material to
cool then continue
cut.
2. Increase speed and/or reduce current until
dross is reduced to minimum
3. Inspect
and
repair or replace
worn parts
Arc stops while
cutting
1. Cutting speed too slow
2. Torch is too high, away from material
3. Worn torch parts
4. Work piece earth cable disconnected
1. Increase speed until problem solved
2. Lower torch to recommended height
3. Inspect
and
repair or replace
worn parts
4. Connect work piece earth clamp
to
work piece or steel table.
Insufficient
penetration
1.Cutting
speed too fast
2. Torch tilted too much
3.Metal too thick for plasma capacity
4. Worn torch parts
1.Slow down travel speed
2. Adjust
tilt
3. Several passes may be necessary
4. Inspect
and
repair or
replace worn parts
Arc sputters/flares
Water in the air supply
Install air
drier
or additional
filtration
Consumables wear
quickly
1. Exceeding unit capability
2. Excessive ARC starting HF use
3. Improperly assembled torch
4. Inadequate air supply, pressure too low
5. Faulty air compressor
1. Material too thick, increase angle to
prevent blow back into torch tip
2. See section
‘Replacing Consumables’
3. Check air filters,
increase air pressure
4. Check
air compressor operation and
make sure input air pressure is at
least
100
PSI
Circuit breaker/fuse
trips while operating
Extension
cord
being used is not
heavy duty
Use a heavy duty extension cord (at least
2.5mm2 section)
If you have any problems in setting up or operating the machine, please rst re-consult this manual.
3.5
Operation
environment
▲ Height above sea level ≤1000 M
▲ Operation temperature range -10°+40°C
▲ Air relative humidity is below 90 %( 20°C)
▲ Preferable site the machine some angles above the oor level, the maximum angle does not
exceed 15
�
.
▲ Protect the machine against heavy rain AND against direct sunshine.
▲ The content of dust, acid, corrosive gas in the surrounding air or substance cannot exceed normal
standard.
▲ Take care that there is sufcient ventilation during welding. There must be at least 30cm free
distance between the machine and wall.
3.6
Operation
Notices
▲ Read Section 1 carefully before starting to use this equipment.
▲ Ensure that the input is single-phase: 50/60Hz, 110V/220V ±10%.
▲Before operation, none concerned people should not be around the working area and especially
children. Do not watch the arc in unprotected eyes.
▲ Ensure good ventilation of the machine to improve Duty Cycle.
▲ Turn off the engine when the operation nished for energy consumption efciency.
▲When power switch shuts off protectively because of failure. Don’t restart it until problem is resolved.
Otherwise, the range of problem will be extended.
▲In case of problems, contact your local dealer if no authorized maintenance staff is available!
Summary of Contents for GRAND CUT 40 PFC MV
Page 17: ......