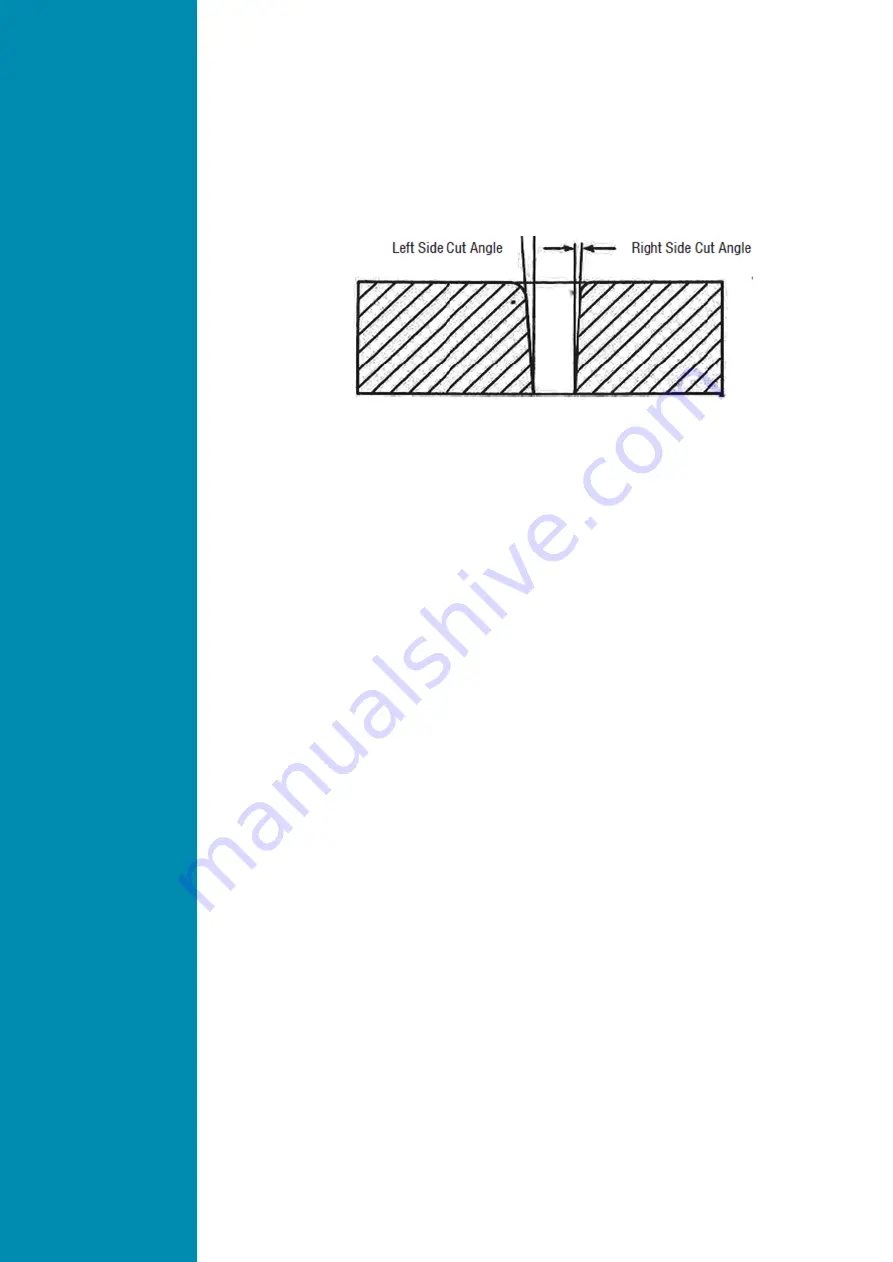
5. Direction of Cut - The plasma gas stream swirls as it leaves the torch to maintain a smooth column
of gas. This swirl effect results in one side of a cut being more square than the other. Viewed along
the direction of travel, the right side of the cut is more square than the left.
To make a square-edged cut along an inside diameter of a circle, the torch should move counter
clockwise around the circle. To keep the square edge along an outside diameter cut, the torch
should travel in a clockwise direction.
6. Quality Cuts - Dross (slag) is the excess material that spatters and builds up on the underside of the
work-piece as you cut. Dross occurs when the operating procedure and technique is less than
optimal. It will require practice and experience to obtain cuts without dross. Although less than
optimal cuts will contain dross, it is relatively easy to remove by breaking it off using pliers or
chipping off with a chisel or scraping or grinding the nished cut as needed and is generally only
a minor inconvenience.
A combination of factors contributes to the build-up of dross. They include; material type, material
thickness, amperage used for the cut, speed of the torch across the work-piece, condition of the torch
tip, input line voltage, air pressure, etc. Generally there is an inversely proportional relationship
between output current and speed of cut. Do not use more output current than is necessary and
adjust speed of cut toward minimizing dross build-up on underside of cut. Experiment with adjusting
current and speed to minimize dross.
When dross is present on carbon steel, it is commonly referred to as either ‘high speed, slow speed, or
top dross’. Dross present on top of the plate is normally caused by too great a torch to plate distance.
‘Top dross’ is normally very easy to remove and can often be wiped off with a welding glove.
‘Slow speed dross’ is normally present on the bottom edge of the plate. It can vary from a light to
heavy bead, but does not adhere tightly to the cut edge, and can be easily scraped off. ‘High speed
dross’ usually forms a narrow bead along the bottom of the cut edge and is very difcult to remove.
When cutting troublesome steel, it is sometimes useful to reduce the cutting speed to produce
‘slow speed dross’. Any resultant clean up can be accomplished by scraping, not grinding.
Summary of Contents for GRAND CUT 40 PFC MV
Page 17: ......