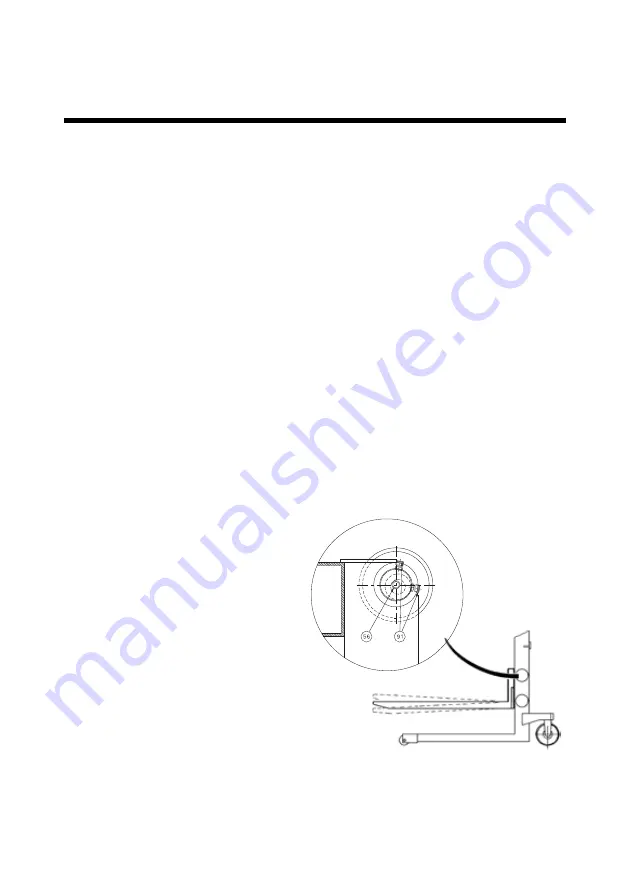
21
6.0 Long live the Logiflex
6.3 The hydraulic pump
The hydraulic pump has a S3 “periodic intermittent duty” of 10%. This means that
the pump in total is allowed to operate 1 minute for a period of 10 minutes.
Note!
If the pump operates more than 10%, the motor will be damaged due to
superheating.
Bleeding the hydraulic system
With a load of 50-100 kg, the forks must be raised and lowered to top and bottom
position 2-3 times.
6.4 Fork adjustment
Two of the rollers on the fork bracket are mounted on eccentric pins, so that they
can be adjusted. The adjustable rollers are at the top.
1. Loosen screw (pos. 91)
(key width 5 mm).
2. Eccentric pins (pos. 56) (key width 8 mm) can now be turned to give the
necessary fork adjustment.
3. Adjustment must be made on both sides to ensure uniform loading of
the rollers.
Summary of Contents for LOGIFLEX SELF1003
Page 1: ...LOGIFLEX SELF1003 SELFS1003...
Page 9: ...9 3 0 How to operate the Logiflex...
Page 29: ...29 7 0 Fault codes Fault location key...
Page 31: ...31...