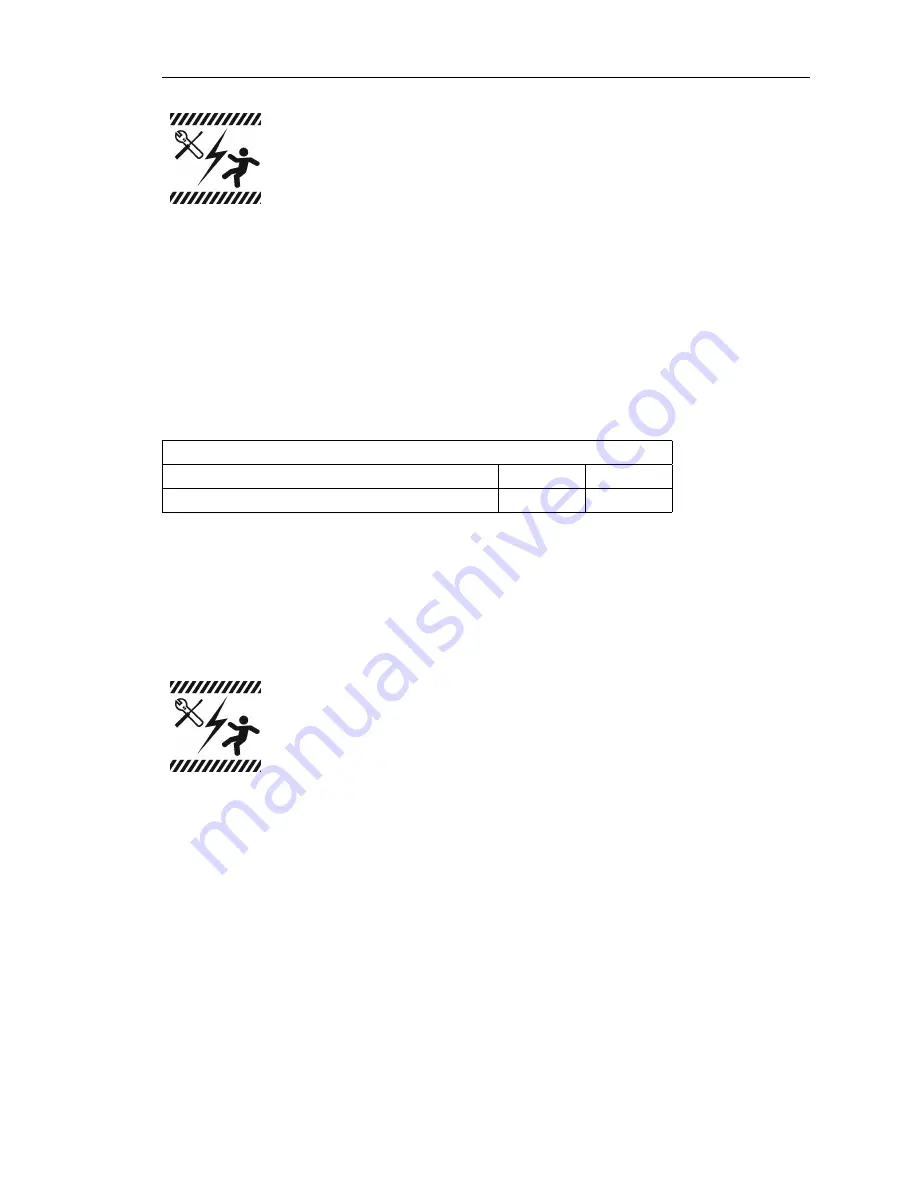
9. Miscellaneous
LOFA does not recommend using sealant with unsealed connectors.
Sealant traps moisture in the connector and encourages corrosion.
9.2.5
Harness Routing
The minimum routing radius of the wiring harnesses should be at least two times the diameter of the
wiring harness. Bends should be avoided within 1 inch (25 mm) of any connector in order to avoid
seal distortion allowing moisture to enter the connector.
9.3
Engine Starter Excitation Connection
9.3.1
Starter Relay
General Starter Relay Specifications
Minimum Starter Relay (Continuous) Rating
60A@12V
30A@24V
Maximum Starter Relay Excitation Current Draw
5A@12V
3A@24V
LOFA provides suitable heavy duty relays and generic starter relay wiring kits in both 12v and 24V;
please contact your LOFA reseller for more information.
9.3.2
Battery Circuit Requirements
Improper wiring can cause electrical noise, unreliable operation and may
damage the control system or other components. All power connections
must be free from foreign materials, including paint, which may interfere with
proper connection. A reliable 30A maximum fused power circuit must be
provided for the control system. LOFA recommends the power connection
be made directly to the battery with the fuse electrically close to the battery.
Grounding through frame members is not recommended. All circuit paths
must be capable of carrying any likely fault currents without damage. Do
not reverse the battery polarity. Attempting to crank the engine when the
polarity of the battery connections is reversed may damage the control
system.
9.3.3
Battery Positive Connection
The electronic control system operates on either a 12 VDC or 24 VDC electrical systems. The
unswitched battery positive connection to the control system is made at the weather proof connector.
The control system provides switched positive battery protected by solid-state MOSFETs. These
outputs include integral protection against overloads and short circuits.
Powering the control system through a 30A fused dedicated circuit reduces the possibility of system
damage.
LOFA document No. 463-3002-59
Page 39