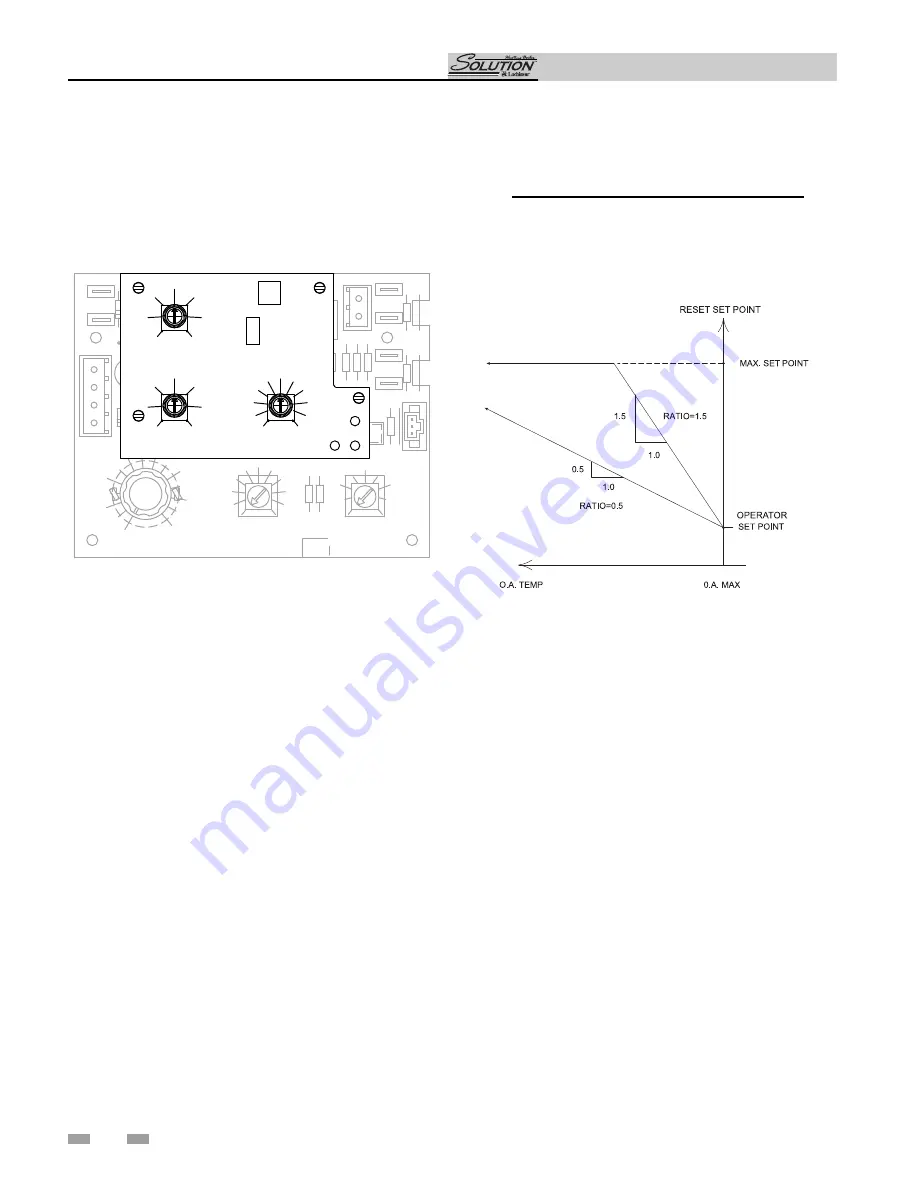
Installation & Service Manual
38
Outdoor Air Reset Option
For boilers ordered with the Outdoor Air Reset option, there
is an additional control (FIG. 5-5). There are three setting
knobs for Shutdown, Outdoor Air Max., and Ratio. There is
also a switch to turn the outdoor air shutdown feature On or
Off. An O.A. Sensor is also included.
R4R
4
R6R
6
R8R
8
R16R
1
6
R15R
1
5
C7C
7
C9C
9
C10C
1
0
VR2
VR2
VR3
VR3
OJ1
OJ1
OJ2
OJ2
D4D
4
J4J
4
CN1
CN1
CN2
CN2
CN9
CN9
CN7
CN7
CN8
CN8
CN3
CN3
CN4
CN4
CN5
CN5
CN6
CN6
W1
W1
TST2314
TST2314
20
20
15
15
10
10
5
5
(F-)0
(F-)0
15
15
14
14
13
13
12
12
11
11
10
9
9
8
8
7
7
6
6
5
5
OFF
OFF
120
120
240
240
220
220
200
200
160
160
140
140
SETPOINT
SETPOINT
DIFFERENTIAL
DIFFERENTIAL
HIGH-FIRE
HIGH-FIRE
OFFSET
OFFSET
(c)2002 L.C.
(c)2002 L.C.
SHUTDOWN
45
50
45
1.3
O.A. MAX.
70
40
VR1
65
RATIO
VR2
0.6
0.5
0.7
1.4
1.5
W1
W2
W3
60
50
70
40
55
60
VR3
65
DISABLE
O.A. SHUTDOWN
1.0
0.9
0.8
1.2
1.1
O.A. SENSOR
ENABLE
ON
SW1
55
CN1
Shutdown
The Shutdown knob specifies the outdoor air lockout
temperature at which the control would prevent the unit from
operating.
Outdoor Air Max (O.A. Max)
The O.A. Max knob allows a reset up to the maximum
outdoor air temperature specified by this knob setting. When
the outdoor air temperature is above the specified setting, the
unit will not function in the O.A. Reset Mode, but will
continue to run at the selected set point temperature.
Note that the set point knob will now indicate the “minimum”
boiler temperature. Target temperature is determined by the
ratio and outdoor air temperature below the O.A. Max
setting.
Ratio
The Ratio knob allows control over the reset ratio to be used
during Outdoor Air Reset. The allowable ratios are as low as
0.5:1 or as high as 1.5:1.
Selecting the 0.5:1 ratio will increase the set point 0.5° for
every 1.0° drop in outdoor air temperature up to the
maximum set point temperature.
Selecting the 1.5:1 ratio will increase the set point 1.5° for
every 1.0° drop in outdoor air temperature up to the
maximum set point temperature.
If the outdoor design and boiler design temperatures are known,
the Ratio setting can be calculated using the following formula:
Ratio = (boiler design temperature - operator set point)
(O.A. Max. setting - outdoor design temperature)
Note that the reset set point cannot exceed the maximum set
point of the boiler thermostat.
These settings are illustrated graphically in FIG. 5-6.
Figure 5-5_
Optional Outdoor Air Reset Control
Figure 5-6_
Outdoor Air Control Example Chart
Outdoor Air Shutdown Enable/Disable Switch
The Outdoor Air Shutdown Enable/Disable switch turns the
outdoor air shutdown feature On and Off. Disabling the
Outdoor Air Shutdown feature allows the unit to operate
regardless of the outdoor air temperature. This is needed for
indirect domestic hot water systems for example
.
Additional Temperature Controls
High Water Temperature Limit Con trol
The appliance is supplied with a fixed setting, auto-reset high
water temperature limit control. The setting of this control
limits max
i
mum discharge water tem
per
a
ture. If water
temperature exceeds the setting, the limit will break the con trol
circuit and shut down the appliance. The limit control will only
be reset after the water tem per a ture has cooled well below the
setting of the limit. The auto-reset high water temperature limit
control is mount ed in the outlet side of the front header.
5
Electrical connections
Summary of Contents for SOLUTION 260000
Page 51: ...51 Notes...