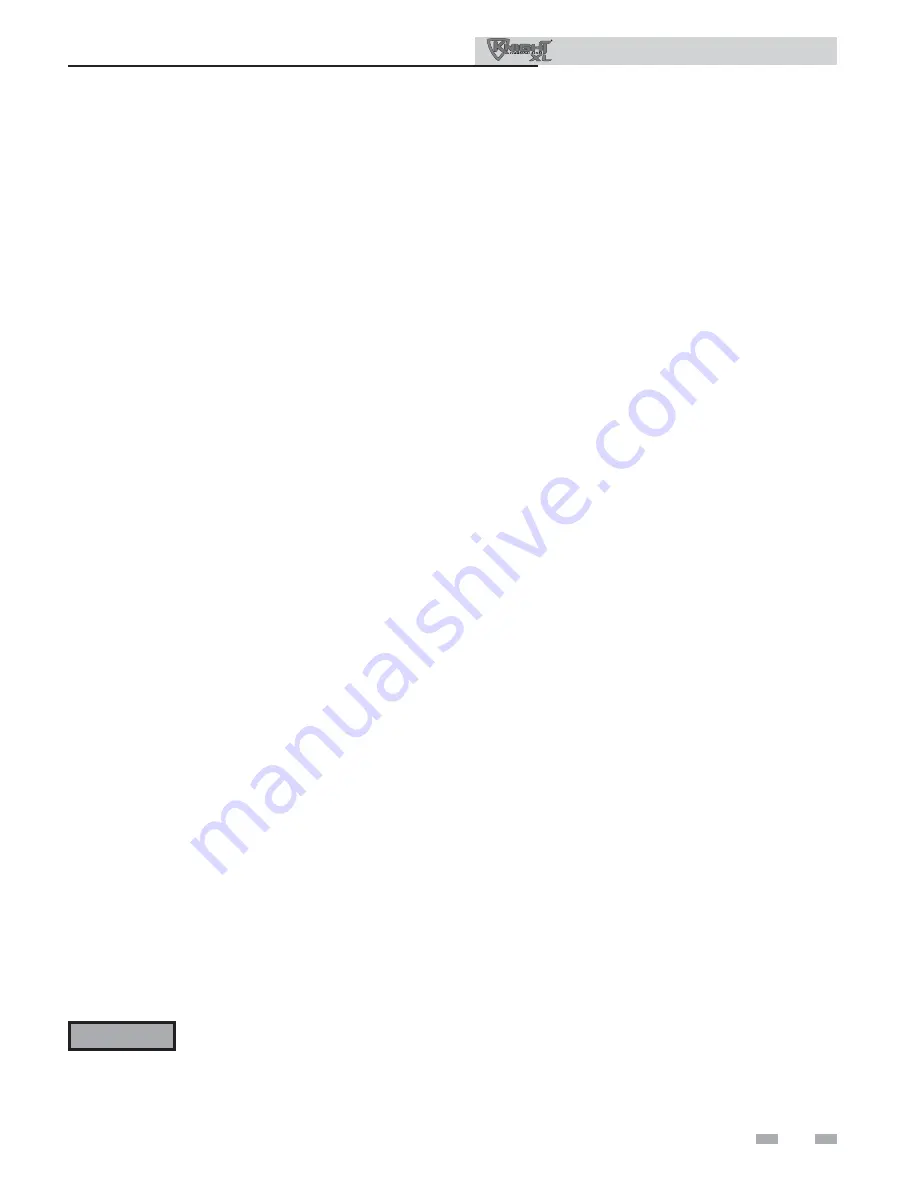
51
8
Field wiring
(continued)
Thermostat
1. Connect the room thermostats or end switches (isolated
contact only) to heat/loop demand 1, 2, or 3, as shown in
FIG. 8-3.
2. Install the thermostat on the inside wall away from
infl uences of draft s, hot or cold water pipes, lighting
fi xtures, television, sunlight, or fi replaces.
3. Th
ermostat anticipator (if applicable):
a.
If connected directly to boiler, set for 0.1 amps.
b. If connected to relays or other devices, set to match
total electrical power requirements of connected
devices. See device manufacturers’ specifi cations
and thermostat instructions for details.
Outdoor temperature sensor
1. Mount the sensor on an exterior wall, shielded from
direct sunlight or fl ow of heat or cooling from other
sources.
2. Route sensor wires through a knockout at the rear of the
boiler (see FIG. 8-2).
3. Connect the outdoor temperature sensor (FIG. 8-3) to
the outdoor sensor terminals on the connection board to
enable outdoor reset operation of the Knight XL. If fi xed
temperature operation is required, do not install outdoor
sensor.
DHW (Domestic Hot Water)
thermostat
Connect storage indirect water heater (DHW) thermostat
(FIG. 8-3) to the DHW thermostat terminals on the
connection board. If a tank sensor is connected (see DHW
Tank Sensor below) the tank thermostat is ignored.
DHW tank sensor
By installing a tank sensor, the SMART SYSTEM control can
perform the tank thermostat function. Th
e SMART SYSTEM
control automatically detects the presence of this sensor, and
generates a DHW call for heat when the tank temperature
drops 6°F (3°C) below the tank set point, and fi nishes the call
for heat when the tank temperature reaches the tank set point.
Th
e tank sensor included with the Lochinvar Squire® indirect
DHW tanks (100170544) is the only sensor suitable for use
with the SMART SYSTEM control. Connect the sensor leads
to the Tank Sensor terminals on the low voltage connection
board (FIG. 8-3).
Louver proving switch
1. When the operation of the louvers needs to be verifi ed
before the boiler fi res, remove the jumper wire from these
terminals and connect them to the normally open contacts
on its proving switch (FIG. 8-3).
High gas pressure switch
1. If a switch is provided to detect excessive gas pressure,
remove the jumper wire from the terminals on the
connection board, and then connect them to its normally
closed contacts (FIG. 8-3).
Low gas pressure switch
1. If a switch is provided to detect low gas pressure, remove
the jumper wire from the terminals on the connection
board and connect them to its normally open contacts
(FIG. 8-3).
2. If both a high and low gas pressure switch is used, connect
their respective contacts in series, and connect them to the
terminals on the connection board (FIG. 8-3).
Failure to use the correct sensor may
result in the tank temperature being either
above or below the set point.
WARNING
If 100170544 is not compatible with the indirect tank, a
tank thermostat can be used to control the boiler. Th
e
tank thermostat should be installed per the manufacturer’s
instructions and wired to the DHW Th
ermostat terminals on
the low voltage connection board (FIG. 8-3).
Variable speed system pump
If a variable speed pump is used in the primary loop, and
a 0-10V signal is available from the pump speed control,
this signal can be used by the SMART SYSTEM control to
anticipate changes in the building heat load. By connecting
this 0 - 10V signal to the 0 - 10V SYS PUMP IN terminals, the
boiler (or cascade) can modulate up and down as the primary
fl ow increases and decreases.
Boiler pump speed output
Th
is 0 - 10V output is available to control the speed of a variable
speed boiler pump. Th
e SMART SYSTEM control will vary the
speed of this pump in order to maintain a minimum
T across
the heat exchanger, as well as prevent high limit lockouts when
the fl ow in the primary loop is extremely low. Connect this
output to the 0 - 10V input on the boiler pump speed control.
Rate output
Th
is output provides a 0 - 10V signal that is proportional to the
fi ring rate of the boiler. Th
is may be used by a BMS system to
monitor the actual rate of the boiler.
Installation & Operation Manual