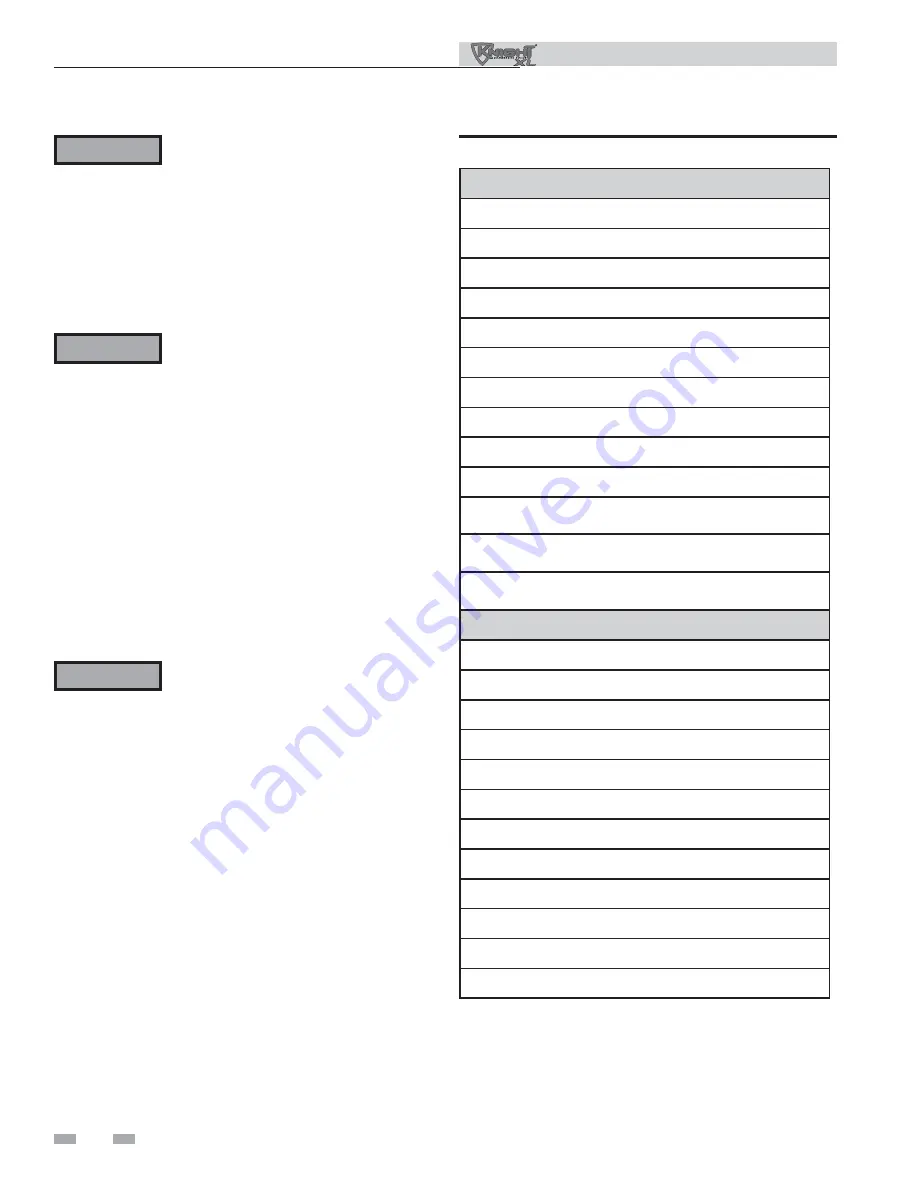
1
Prevent combustion air contamination
4
If the boiler combustion air inlet is located in
a laundry room or pool facility, for example,
these areas will always contain hazardous
contaminants.
To prevent the potential of severe personal
injury or death, check for areas and products
listed in Table 1A before installing the boiler
or air inlet piping.
If contaminants are found, you MUST:
• Remove contaminants permanently.
—OR—
• Relocate air inlet and vent
terminations to other areas.
WARNING
WARNING
Products to avoid:
Spray cans containing chloro/fluorocarbons
Permanent wave solutions
Chlorinated waxes/cleaners
Chlorine-based swimming pool chemicals
Calcium chloride used for thawing
Sodium chloride used for water softening
Refrigerant leaks
Paint or varnish removers
Hydrochloric acid/muriatic acid
Cements and glues
Antistatic fabric softeners used in clothes dryers
Chlorine-type bleaches, detergents, and cleaning solvents
found in household laundry rooms
Adhesives used to fasten building products and other similar
products
Areas likely to have contaminants
Dry cleaning/laundry areas and establishments
Swimming pools
Metal fabrication plants
Beauty shops
Refrigeration repair shops
Photo processing plants
Auto body shops
Plastic manufacturing plants
Furniture refinishing areas and establishments
New building construction
Remodeling areas
Garages with workshops
Table 1A Corrosive Contaminants and Sources
WARNING
If the boiler combustion air inlet is located
in any area likely to cause contamination,
or if products which would contaminate
the air cannot be removed, you must have
the combustion air and vent re-piped
and terminated to another location.
Contaminated combustion air will damage
the boiler, resulting in possible severe
personal injury, death, or substantial
property damage.
Pool and laundry products and common household and hobby
products often contain fluorine or chlorine compounds. When
these chemicals pass through the boiler, they can form strong
acids. The acid can eat through the boiler wall, causing serious
damage and presenting a possible threat of flue gas spillage or
boiler water leakage into the building.
Please read the information listed in Table 1A. If contaminating
chemicals will be present near the location of the boiler
combustion air inlet, have your installer pipe the boiler
combustion air and vent to another location, per the Knight XL
Installation and Operation Manual.
User’s Information Manual