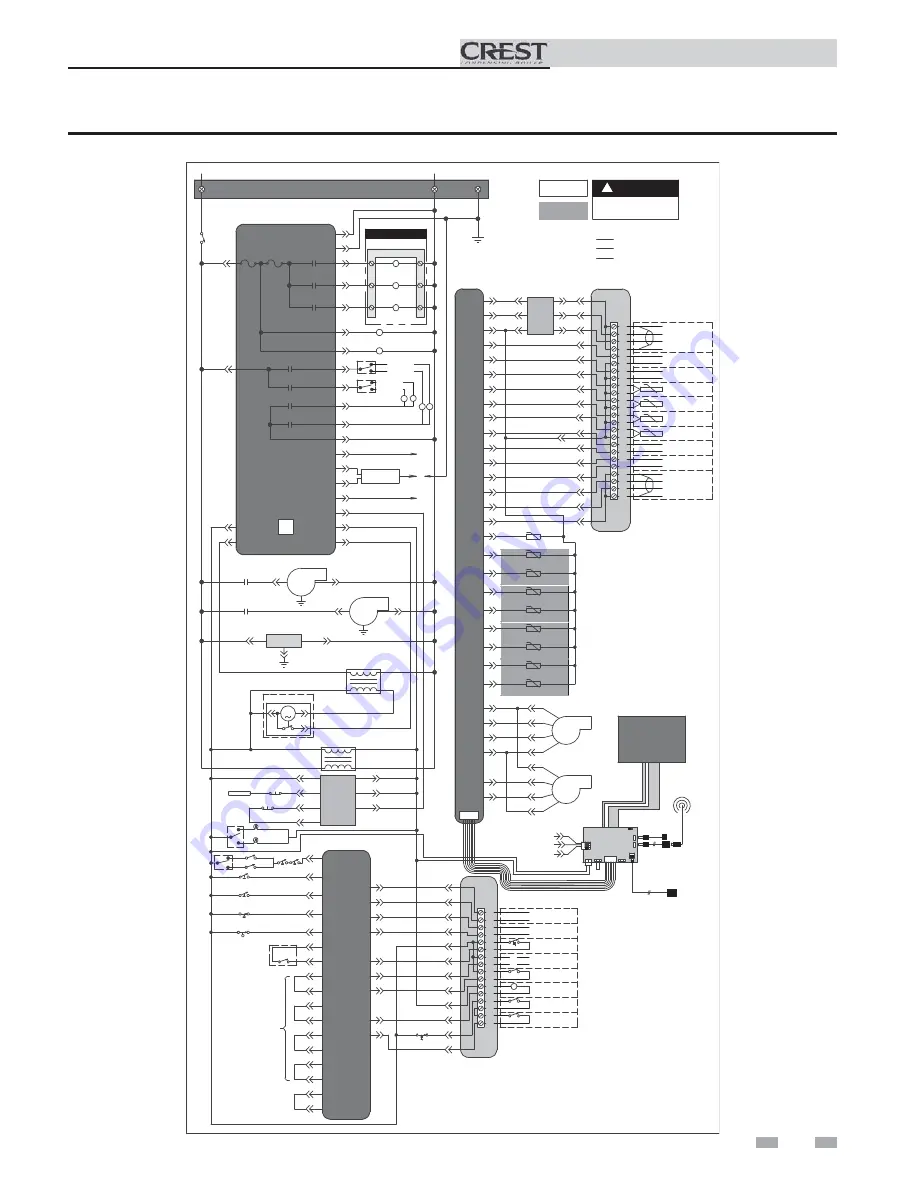
13
Dual Fuel Supplemental Manual
PRE-MIX SENSOR 1 (S11)
FLUE SENSOR (S10)
FLUE SENSOR
OUTLET SENSOR (S1)
-T
-T
-T
-T
-T
-T
-T
-T
PRE-MIX SENSOR 2 (S14)
PRE-MIX SENSOR 2 (S12)
PRE-MIX SENSOR 1 (S13)
OUTLET SENSOR (S9)
1.5A EACH MAX
WARNING
OUT
100267529 REV A
JUNCTION BOX
TERMINAL STRIP
120V SUPPLY "L"
TERMINAL STRIP
120V SUPPLY "N"
120VAC
NEUTRAL
INTEGRATED CONTROL
ON/OFF
SWITCH
F2
3.15 A
F4
5.0 A
SYSTEM PUMP
RELAY
BOILER PUMP
RELAY
DHW PUMP
RELAY
X1-1
X1-2
X1-4
X1-8
X2-4
SMALL BLOWER RELAY
LARGE BLOWER RELAY
SMALL GAS
VALVE RELAY
LARGE GAS
VALVE RELAY
X1-6
2
-
0
1
X
1
-
0
1
X
X10-3
SMALL GAS
VALVE RELAY
LARGE GAS
VALVE RELAY
X10-6
X10-5
X10-4
TERMINAL STRIP
SYSTEM PUMP
CONTACTOR
BOLIER PUMP
CONTACTOR
DHW PUMP
CONTACTOR
SMALL BLOWER
RELAY
LARGE BLOWER
RELAY
SMALL BLOWER
LARGE BLOWER
X6-10
X13-4
X6-1
X2-5
2
1
3
2
1
3
BAS
X1-1
X1-2
X1-3
FLUE DAMPER
TRANSFORMER
1
2
3
24V
TRANSFORMER
FLUE DAMPER
X6-3
X1-12
X1-3
LWCO
BOARD
TEST
SWITCH
LWCO
PROBE
LWCO RESET
J3-6
J3-3
J2-1
J2-2
J3-5
J3-2
J3-4
X6-5
X6-15
X6-12
X13-1
X6-6
X3-3
X3-4
X3-1
X3-2
X6-11
X6-2
X6-14
INTEGRATED
CONTROL
BLOWER PROVING
SWITCH (LARGE)
BLOWER PROVING
SWITCH (SMALL)
BLOCKED FLUE
SWITCH
BLOCKED DRAIN
SWITCH
1
2
3
4
5
6
7
8
9
10
11
12
13
14
15
16
ALARM
CONTACTS
RUN-TIME
CONTACTS
TANK
THERMOSTAT
LOUVER
PROVING
24 VAC LOUVER
RELAY COIL
AUX
SWITCH 1
AUX
SWITCH 2
ENABLE
R
W
SMALL
CONNECTION BOARD
CN1-4
CN1-5
CN1-6
CN1-12
CN1-10
X6-13
X6-4
CN1-11
CN1-9
CN1-8
CN1-7
CN1-1
CN1-2
CN1-3
HIGH LIMIT
SWITCH
X1-3
X1-7
X1-10
X2-5
FLAME
SENSE 2
FLAME
SENSE 1
SPARK
GENERATOR
SPARK
ROD
17
18
19
20
21
22
23
24
25
26
27
28
29
30
31
32
33
34
35
36
37
38
39
40
SHIELD
SHIELD
A
B
MODBUS
OPTION
+
-
-
+
RATE
X6-17
BOILER
PUMP OUT
SYSTEM RETURN
SENSOR
SYSTEM SUPPLY
SENSOR
0-10V
0-10V
TANK
SENSOR
OUTDOOR
SENSOR
+
+
-
-
0-10V
0-10V
BMS
IN
SYSTEM
PUMP IN
SHIELD
SHIELD
A
B
CASCADE
LARGE
CONNECTION BOARD
CN6-1
CN3-6
CN3-7
CN3-14
CN3-13
CN3-11
CN3-9
CN3-8
CN3-1
CN3-2
CN3-3
CN3-4
CN6-2
CN6-3
CN3-10
CN3-12
BAS
X4-1
X4-2
X4-3
X6-3
X6-1
X6-2
X8-20
X8-10
X7-8
X8-13
X8-14
X8-12
INTEGRATED
CONTROL
X8-5
X8-15
X7-7
X8-11
X8-6
X8-16
X8-7
X8-17
X8-1
-T
INLET SENSOR
X8-3
X8-8
X8-2
X8-4
X8-9
X7-1
X7-5
X7-2
X7-6
GROUND
X6-18
X6-9
M
X6-8
X13-2
X13-3
1
2
4
5
1
2
4
5
SMALL BLOWER
LARGE BLOWER
X11
X4
X5-1
X5-7
X5-2
X5-8
X5-3
X5-9
X5-4
X5-10
X5-5
X5-41
X5-6
X5-12
HIGH VOLTAGE
LOW VOLTAGE
OPTIONAL ITEMS
DUAL SENSOR
DISCONNECT POWER
non-repairable damage to the integrated controller or other components.
BEFORE SERVICING
CN6-2
3. Actual connector block locations may vary from those show n on diagrams. Refer to actual components for proper connector blo ck
SINGLE HOUSING
120 VAC
locations when using diagrams to troubleshoot unit.
USB
INTERFACE
"X5"
BLOCK WIRING
IS MODEL
DEPENDANT
CAM
SWITCH
PROPANE LIGHT
NATURAL LIGHT
NATURAL LGPS
PROPANE LGPS
CAM SWITCH
GPS2 GPS3
PROPANE
NATURAL
PROPANE
NATURAL
CN3-4
X8-1
OPTIONAL
ETHERNET CABLE
E
GND
WIFI
DONGLE
RIBBON CABLE
SW1
J2
8
43
J6
J9
J17
J23
J12
J11
LG CON BRD
J8
LCD
DISPLAY
USB CABLE
OPTIONAL USB/WIFI
EXTENSION CABLE
J10
J7
BAS
CN6-1
CN6-3
24V
Notes:
1. All wiring must be installed in accordance with: local, state, provincial and national code requirements per either N.E.C. in USA or
C.S.A. in Canada.
2. If any original equipment wire as supplied with the appliance must be replaced, it must be replaced with wire having same wi re gauge
(AWG) and rated for a minimum of 105°C. Exceptions: Replac ement high voltage spark lead and ribbon cables must be purchased
from the factory. Use of a non-approved spark lead or ribbon cables can lead to operational problems which could result in
BOX DEPICTS
BOX DEPICTS
!
3
Diagrams
(continued)
Figure 3-2 Ladder Diagram_2.5 - 3.5 Models