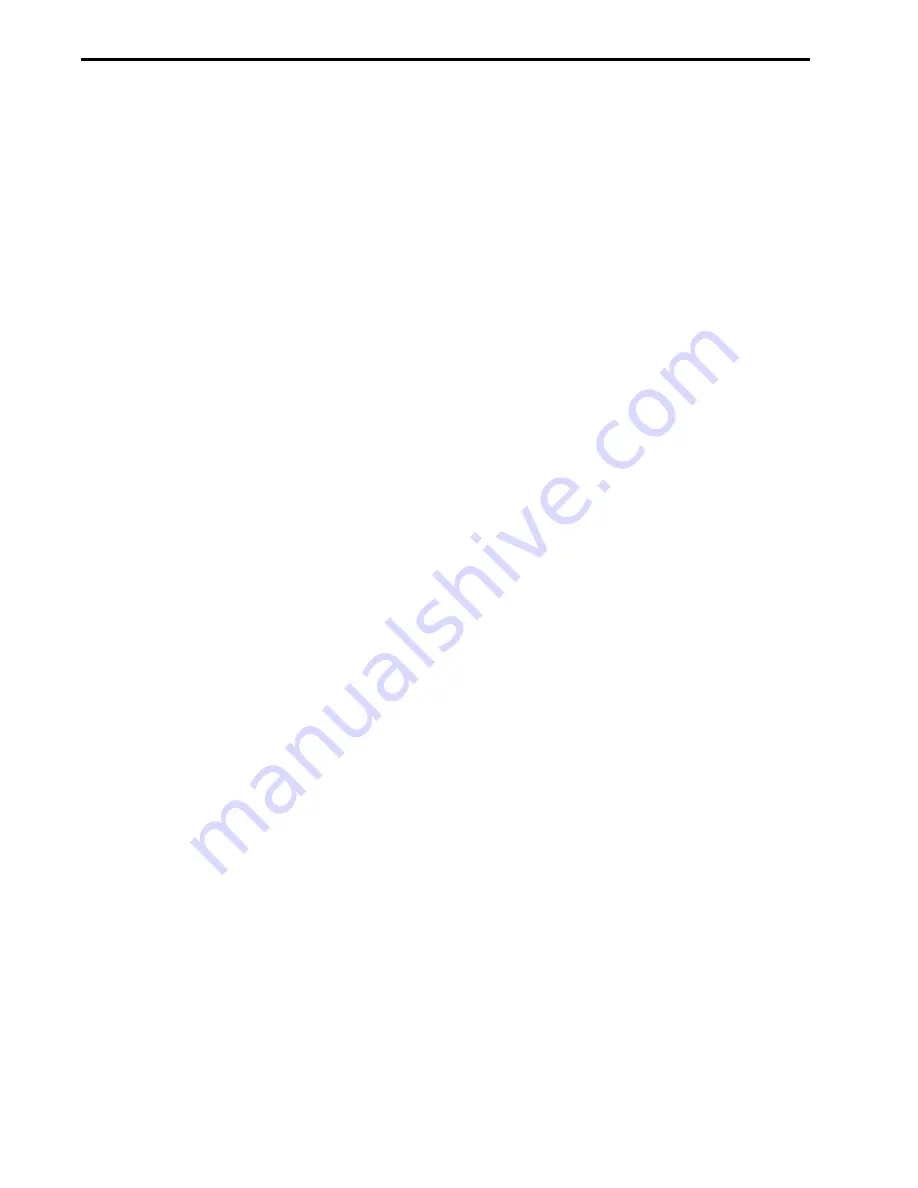
collective-pitch (constant-speed) main rotor systems do not normally experience
retreating blade stall during descents, and do not require as much forward stick
pressure to maintain forward speed.
Anti-Torque Systems
The torque (reaction force) created by rotating the main rotor of a helicopter in one
direction tends to cause the body to turn in the opposite direction. When trimmed for
steady hovering flight, the tail rotor at the end of the tail boom creates enough thrust
force to balance the torque produced by the main rotor so that the helicopter
maintains a constant heading. Decreasing or increasing the thrust force of the tail
rotor causes the helicopter to turn in one direction or the other.
The pilot of a full-size helicopter controls the tail rotor by manipulating foot pedals
located within the cockpit. The pilot of a model helicopter manipulates control sticks
on a radio transmitter which in turn sends commands to servo actuators located
within the flying model. Cables, pushrods, and bellcranks connect the pedals or the
servos to the pitch controls of the tail rotor blades. The pilot adjusts the pitch and
associated thrust force of the rotating tail rotor blades to turn the helicopter.
Although a number of modern anti-torque systems (such as blown tail booms and
shrouded fans) have been developed, tail rotors have not changed materially for over
25 years. For reasons of structure and simplicity, and to minimize actuation forces,
tail rotor blades traditionally employ symmetrical cross sections such as a NACA
0012 airfoil, and simple constant-chord blade shapes. While easy to build, these
rotors do not utilize power very efficiently. Since helicopters have relatively low
payload capacities, even small increases in rotor performance can result in large
percent changes in payload capacity.
Cambered (curved) airfoils can substantially increase the lifting potential of a rotor
blade. Cambered airfoils, however, have a drawback: the curvature of the airfoil
causes the airfoil to pitch downward toward negative angles of attack. This pitching
tendency can cause the rotor blade to twist and exert high loads on the blade
pitch-control linkages (and consequently to the pilot’s legs in full-size helicopters, or
to the servos in model helicopters).
The unique swept tail rotor blades on Lite Machines helicopters balance the
aerodynamic twisting forces of high lift cambered airfoils with other forces. They
operate something like canards (little forward wings) on an airplane by balancing the
negative twisting force of cambered airfoils with a positive lift force located in front of
the blade pitching axis. Small counterweights at the blade root also help to balance
the aerodynamic forces. As a result, tail rotor power requirements are lower, and
control linkage forces are reduced by as much as 80%.
Op er a tor's Guide
How Helicopters Work
8-8
LITE MA CHINES