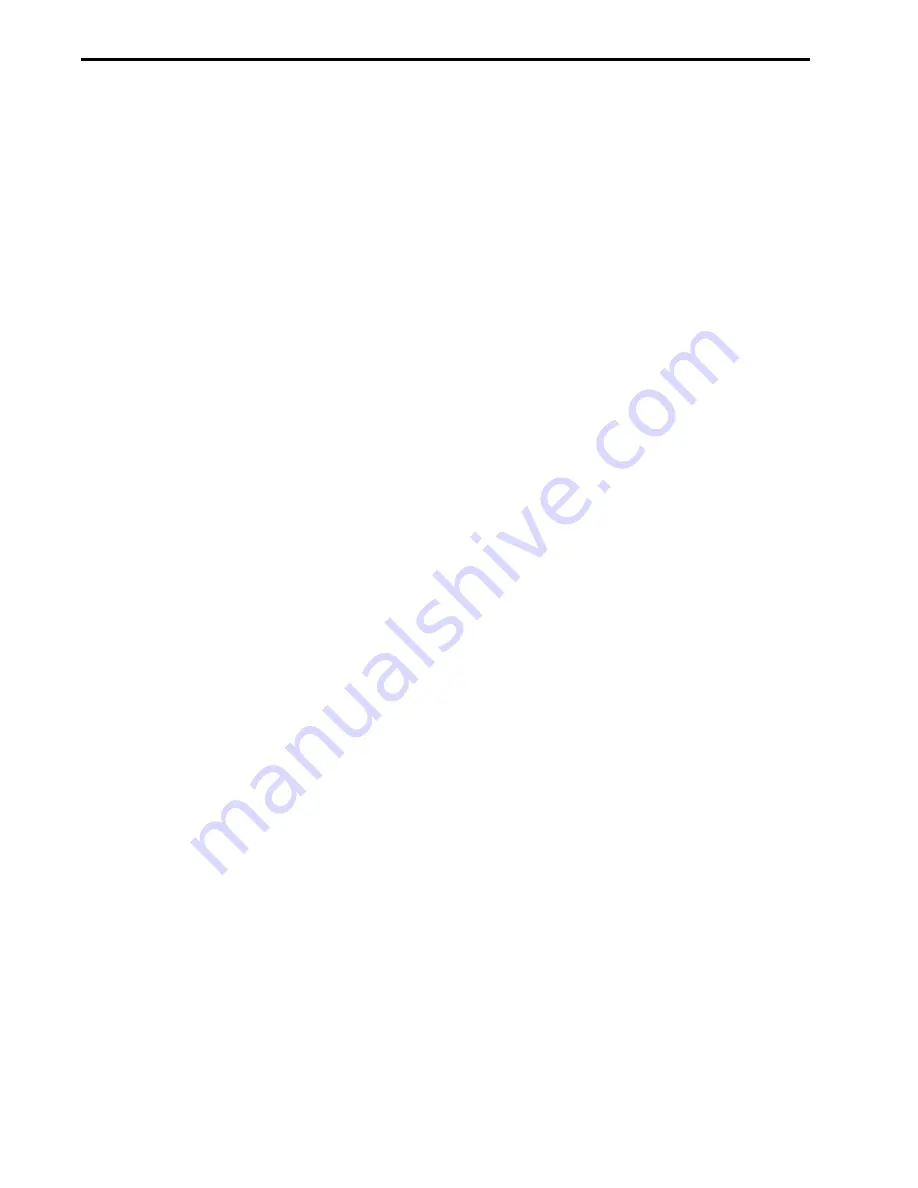
Since the main rotor on a helicopter rotates while the fuselage or body of the
helicopter does not, some mechanism is needed to transmit control commands from
the non-rotating pilot to the rotating main rotor blades. One such mechanism is called
a swashplate which is essentially a large ball bearing assembly surrounding the main
rotor shaft. In order to tilt the main rotor, the pilot moves linkages attached to the
lower half of the swashplate. The upper half of the swashplate is connected through
linkages to the rotor blades.
Traditionally, the pilot of a full-size helicopter controls the main rotor by manipulating
a joystick called the “cyclic” control located in front of the pilot, and a lever called the
“collective” control located to the left of the pilot. Cables, pushrods, and bellcranks
connect the cyclic and collective controls through the swashplate to the pitch controls
of the main rotor blades.
Main rotor systems of most radio-controlled model helicopters operate in a manner
similar to full-size helicopters. The pilot manipulates small control sticks on a
hand-held radio transmitter which in turn sends commands to servo actuators
located within the flying model. Pushrods and bellcranks connect the servos through
the swashplate to the pitch controls of the main rotor blades.
To bank the helicopter to the right or left, or move forward or backward, the rotating
rotor blades are pitched upward as they pass around one side of the helicopter and
downward around the other. This is called “cyclic” pitching since the rotor blades
cycle up and down as the rotor rotates. The difference in lift produced on either side of
the helicopter causes the main rotor blades to flap up and down, and the rotor disk
appears to tilt. The tilted rotor disk produces a sideways thrust force that then pushes
the helicopter in the direction of the tilt.
The large size and high inertia of most helicopter rotors means that they cannot
change speed quickly. For this reason, they are usually designed to operate at a
nearly constant rotational speed at all times. To control main rotor lift, the main rotor
blades are pitched upward or downward in unison. This is called “collective” pitching
since all rotor blades move together. The change in pitch, and associated lift force of
the rotating rotor blades causes the helicopter to gain or loose altitude.
Some small model helicopters (such as the Lite Machines
Model 110
) rely on
variable engine speed instead of collective blade pitch for altitude control since main
rotor thrust is proportional to rotor speed as well as blade pitch. The main rotor blades
on these models are typically built at a fixed pitch (relative to each other) and are light
enough to react quickly to changes in engine speed. The primary advantage of
fixed-pitch rotors on models is reduced mechanical complexity and cost.
Main Rotor Stability
Flight stability is often a problem for small helicopters. To improve stability, weighted
stabilizer bars (flybars) are usually incorporated into model helicopters, but are
uncommon on modern full-size helicopters. First patented by Stanley Hiller Jr. in
1953 and refined for use on models by Dieter Shlüter in 1970, these flybars are tipped
with aerodynamic paddles (Hiller paddles), and are connected through linkages to
the swashplate and main rotor blades.
Op er a tor's Guide
How Helicopters Work
8-6
LITE MA CHINES