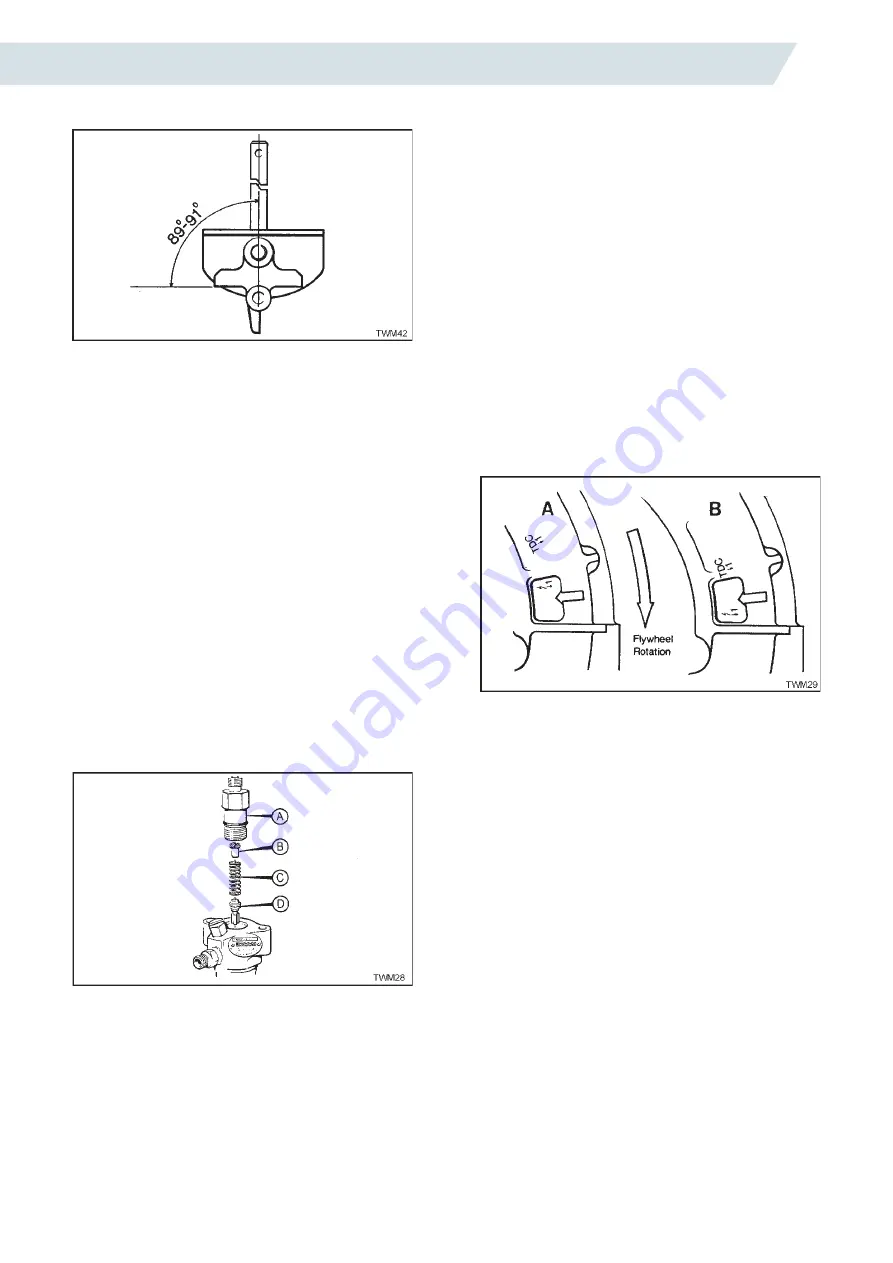
TS, TR, TX engines workshop manual
27
T SERIES ENGINES WORKSHOP MANUAL
29
When re-fitting the new type of linkage to the fuel
pumps it is important to ensure that the radiused
shackles follow the pump radius.
Figure 2.27.3 Fuel Pump Linkage
A - Early TS/TR
B - Later TS/TR and all TX
6.Re-connect the speeder spring to the spigot.
If the spigot was turned when the pumps were
removed it must be turned until the hole axis is
at 90° to the camshaft before refitting the spring
when the speeder spring spigot is upright.
Figure 2.27.4 Speed Control Lever
7.Check the governor setting; refer to "02.31
Setting the Governor".
8.Fit new joints to the fuel pump inspection doors
and replace the doors.
9.Replace the fuel pipes.
10.Prime the fuel system if it is not self-priming.
11.Check and adjust the pump timing.
2.28 FUEL PUMP TIMING
Fuel pump components are manufactured to
exacting limits and care must be taken to ensure
they are returned to their respective pumps if more
than one pump is dismantled at a time.
The fuel pump timing gauge, 317-50518, can
be used to check the timing without the need to
dismantle the pump.
Spill Timing
1.Isolate the fuel supply.
2.Remove the fuel pipe from the pump to the
injector.
3.Unscrew the fuel pump delivery union body (A)
and remove it.
4.Lift out the delivery valve spring seat (B) and
spring (C).
Figure 02.28.1 Fuel Pump Components
5.Carefully lift out the delivery valve (D) taking care
not to disturb the valve seat.
6.Place these components in a suitable container
of clean fuel.
7.Replace the delivery union body (A).
8.Fit a suitable spill pipe.
9.Ensure the fuel pump rack is in the run position
by removing a cylinder fuel pump housing door
and manually moving the fuel pump rack towards
the gear end.
10.Turn the flywheel, in the direction of rotation,
until the piston for the cylinder being timed is at
'FP' on the compression stroke.
At this position both the inlet and exhaust valves
will be closed.
11.Connect the fuel supply and bleed the fuel filter
and pump.
12.Carefully turn the flywheel against rotation until
fuel is flowing from the spill pipe.
13.Turn the flywheel very slowly in the direction of
rotation until the fuel flow from the spill pipe just
stops dripping this is known as the 'Spill Point'.
14.Check the flywheel timing mark.
The flywheel timing mark (FP), which can be
seen through an aperture in the fanshroud,
should align with the arrow on the fanshroud.
15.If the flywheel mark is not correct, see 'Figure
2.28.2', the shims under the fuel pump must be
adjusted, see "Timing Shims".
Figure 2.27.4 Speed Control Lever
7. Check the governor setting; refer to "2.31 Setting the Governor".
8. Fit new joints to the fuel pump inspection doors and replace
the doors.
9. Replace the fuel pipes.
10. Prime the fuel system if it is not self-priming.
11. Check and adjust the pump timing.
2.28 Fuel Pump Timing
Fuel pump components are manufactured to exacting limits
and care must be taken to ensure they are returned to their
respective pumps if more than one pump is dismantled at a time.
The fuel pump timing gauge, 317-50518, can be used to check
the timing without the need to dismantle the pump.
Spill Timing
1. Isolate the fuel supply.
2. Remove the fuel pipe from the pump to the injector.
3. Unscrew the fuel pump delivery union body (A) and remove it.
4. Lift out the delivery valve spring seat (B) and spring (C).
T SERIES ENGINES WORKSHOP MANUAL
29
When re-fitting the new type of linkage to the fuel
pumps it is important to ensure that the radiused
shackles follow the pump radius.
Figure 2.27.3 Fuel Pump Linkage
A - Early TS/TR
B - Later TS/TR and all TX
6.Re-connect the speeder spring to the spigot.
If the spigot was turned when the pumps were
removed it must be turned until the hole axis is
at 90° to the camshaft before refitting the spring
when the speeder spring spigot is upright.
Figure 2.27.4 Speed Control Lever
7.Check the governor setting; refer to "02.31
Setting the Governor".
8.Fit new joints to the fuel pump inspection doors
and replace the doors.
9.Replace the fuel pipes.
10.Prime the fuel system if it is not self-priming.
11.Check and adjust the pump timing.
2.28 FUEL PUMP TIMING
Fuel pump components are manufactured to
exacting limits and care must be taken to ensure
they are returned to their respective pumps if more
than one pump is dismantled at a time.
The fuel pump timing gauge, 317-50518, can
be used to check the timing without the need to
dismantle the pump.
Spill Timing
1.Isolate the fuel supply.
2.Remove the fuel pipe from the pump to the
injector.
3.Unscrew the fuel pump delivery union body (A)
and remove it.
4.Lift out the delivery valve spring seat (B) and
spring (C).
Figure 02.28.1 Fuel Pump Components
5.Carefully lift out the delivery valve (D) taking care
not to disturb the valve seat.
6.Place these components in a suitable container
of clean fuel.
7.Replace the delivery union body (A).
8.Fit a suitable spill pipe.
9.Ensure the fuel pump rack is in the run position
by removing a cylinder fuel pump housing door
and manually moving the fuel pump rack towards
the gear end.
10.Turn the flywheel, in the direction of rotation,
until the piston for the cylinder being timed is at
'FP' on the compression stroke.
At this position both the inlet and exhaust valves
will be closed.
11.Connect the fuel supply and bleed the fuel filter
and pump.
12.Carefully turn the flywheel against rotation until
fuel is flowing from the spill pipe.
13.Turn the flywheel very slowly in the direction of
rotation until the fuel flow from the spill pipe just
stops dripping this is known as the 'Spill Point'.
14.Check the flywheel timing mark.
The flywheel timing mark (FP), which can be
seen through an aperture in the fanshroud,
should align with the arrow on the fanshroud.
15.If the flywheel mark is not correct, see 'Figure
2.28.2', the shims under the fuel pump must be
adjusted, see "Timing Shims".
Figure 02.28.1 Fuel Pump Components
5. Carefully lift out the delivery valve (D) taking care not to
disturb the valve seat.
6. Place these components in a suitable container of clean fuel.
7. Replace the delivery union body (A).
8. Fit a suitable spill pipe.
9. Ensure the fuel pump rack is in the run position by removing
a cylinder fuel pump housing door and manually moving the
fuel pump rack towards the gear end.
10. Turn the flywheel, in the direction of rotation, until the piston
for the cylinder being timed is at 'FP' on the compression
stroke.
At this position both the inlet and exhaust valves will be
closed.
11. Connect the fuel supply and bleed the fuel filter and
pump.
12. Carefully turn the flywheel against rotation until fuel is
flowing from the spill pipe.
13. Turn the flywheel very slowly in the direction of rotation
until the fuel flow from the spill pipe just stops dripping
this is known as the 'Spill Point'.
14. Check the flywheel timing mark.
The flywheel timing mark (FP), which can be seen through
an aperture in the fanshroud, should align with the arrow
on the fanshroud.
15. If the flywheel mark is not correct, see 'Figure 2.28.2', the
shims under the fuel pump must be adjusted, see "Timing
Shims".
T SERIES ENGINES WORKSHOP MANUAL
30
Figure 2.28.2 Flywheel Timing Marks
If the timing is:
Advanced - Add Shims
Retarded - Remove Shims.
Approximately 1° of flywheel movement can be
obtained with a 0.127mm (0.005in) shim.
16.Re-check the timing.
17.When the correct timing has been obtained
remove the spill pipe and delivery union body.
18.Replace the delivery valve, delivery valve spring
and spring seat.
19.Refit the delivery union body and torque it to
35.0/45.0Nm (26.0/33.0lbf ft).
20.Check that the fuel pump calibration marks are
still aligned.
21.Repeat this procedure for the remaining fuel
pumps.
22.Connect all fuel pipes and torque the pump to
injector pipe nuts to:
TS/TR - 29.0Nm (21.0lbf ft).
TX - 22.0Nm (16.0lbf ft).
23.Bleed the entire fuel system.
Fuel Pump Timing Gauge
1.Assemble the pipe (A) to the gauge ensuring that
the pipe nuts are tight.
Figure 2.28.3 Fuel Pump Timing Gauge - 317-50518
2.Remove the fuel pipe from the pump to the
injector.
3.Connect the gauge and pipe to the fuel pump
delivery valve union for the cylinder being timed.
4.Bleed the filter and pump.
5.Ensure the fuel pump rack is in the run position
by removing a cylinder fuel pump housing door
and manually moving the fuel pump rack towards
the gear end.
6.Turn the flywheel, in the direction of rotation, to
prime the gauge.
7.Turn the flywheel, in the direction of rotation, until
the flywheel 'FP' timing mark is in line with the
arrow.
At this position both the inlet and exhaust valves
will be closed.
8.Turn the flywheel against rotation for 50.8mm
(2.00in).
9.Slowly release the gauge knob (B) until the fuel
level is in line with the calibration mark on the
gauge sight glass.
10.Turn the flywheel in the direction of rotation,
extremely slowly, until the fuel in the sight glass
just moves.
11.Check the flywheel timing mark.
The flywheel timing mark (FP), which can be
seen through an aperture in the fanshroud,
should align with the arrow on the fanshroud.
12.If the flywheel mark is not correct, the shims
under the fuel pump must be adjusted, see
"Timing Shims".
Figure 2.28.3 Flywheel Timing Marks
If the timing is:
Advanced - Add Shims
Retarded - Remove Shims.
Approximately 1 of flywheel movement can be
obtained with a 0.127mm (0.005in) shim.
13.Remove the gauge and replace the pump to
injector pipe and torque the pipe nuts to:
TS/TR - 29.0Nm (21.0lbf ft).
TX - 22.0Nm (16.0lbf ft).
Figure 2.28.2 Flywheel Timing Marks
If the timing is:
Advanced - Add Shims
Retarded - Remove Shims.
Approximately 1° of flywheel movement can be obtained
with a 0.127 mm (0.005 in) shim.
16. Re-check the timing.
17. When the correct timing has been obtained remove the spill
pipe and delivery union body.
18. Replace the delivery valve, delivery valve spring and spring
seat.
19. Refit the delivery union body and torque it to 35.0/45.0 Nm
(26.0/33.0 lbf ft).
20. Check that the fuel pump calibration marks are still
aligned.
21. Repeat this procedure for the remaining fuel pumps.
22. Connect all fuel pipes and torque the pump to injector
pipe nuts to:
TS/TR - 29.0 Nm (21.0 lbf ft).
TX - 22.0 Nm (16.0 lbf ft).
23. Bleed the entire fuel system.
Summary of Contents for TS/TR1
Page 1: ...P027 08270 edition 8 April 2021 TS TR TX Engines Workshop Manual T SERIES ...
Page 80: ...TS TR TX engines workshop manual 80 T SERIES ENGINES WORKSHOP MANUAL 90 ct ical Wiring i g ...
Page 85: ...TS TR TX engines workshop manual 85 T SERIES ENGINES WORKSHOP MANUAL 95 ...