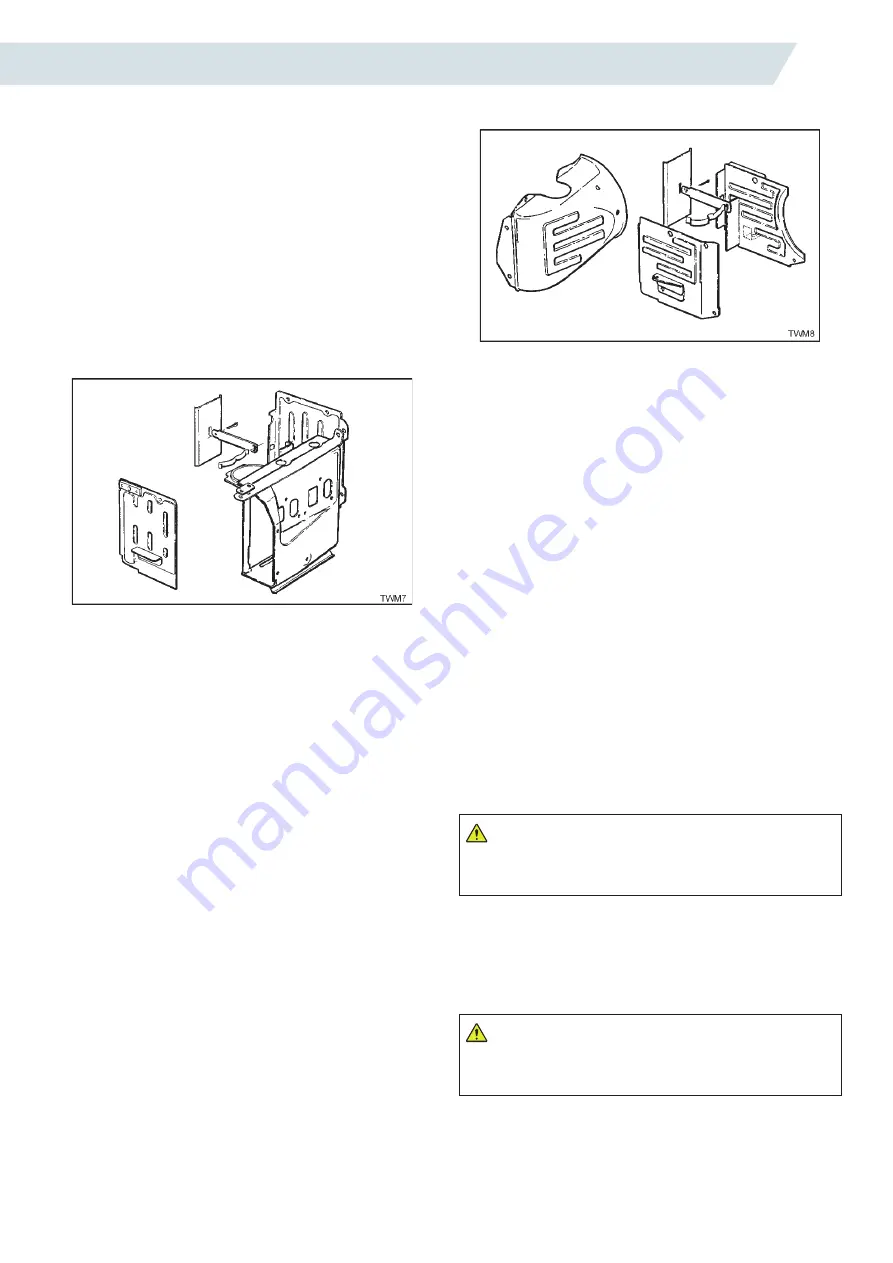
TS, TR, TX engines workshop manual
14
2.5 The Air Cowling
Three sides of the engine are encased in an air cowl and two
sides shields, which together with the air baffle(s) direct cooling
air from the flywheel fan around the cylinders.
Removing the Air Cowling - TS/TR
1. Remove the cold start pots if fitted.
2. Drain the fuel and remove the engine mounted fuel tank,
if fitted.
3. Remove the gear end air shield by removing the setscrews,
spring washers and plain washers in the top plate and air
cowling.
T SERIES ENGINES WORKSHOP MANUAL
15
3.Replace the glowpiug cable.
4.Replace the axial fan air cowling.
2.5 THE AIR COWLING
Three sides of the engine are encased in an air
cowl and two sides shields, which together with the
air baffle(s) direct cooling air from the flywheel fan
around the cylinders.
Removing the Air Cowling - TS/TR
1.Remove the cold start pots if fitted.
2.Drain the fuel and remove the engine mounted
fuel tank, if fitted.
3.Remove the gear end air shield by removing the
setscrews, spring washers and plain washers in
the top plate and air cowling.
Figure 2.5.1 Air Cowling - TS/TR
4.Remove the manifolds.
5.Remove the air cowl by removing the setscrew
in the fanshroud and setscrews, spring and plain
washers in the cowl.
6.If a fuel filter is fitted to the flywheel end shield,
isolate or drain the fuel before disconnecting the
fuel feed to the fuel pumps and remove the nuts
and spring washers securing the fuel filter.
7.Remove the setscrews, spring washers and plain
washers securing the flywheel end shield to the
cylinder head top plate.
A setscrew is fitted in the middle of the filter
mounting block.
8.Remove the shield.
Removing the Air Cowling - TX
1.Remove the air cleaner if necessary.
2.Remove the flywheel end air shield.
3.Remove the axial fan cowling.
4.Isolate or drain the fuel before disconnecting the
fuel pipes to and from the fuel filter.
5.Remove the fuel filter.
6.Remove the gear end air shield; it may be
necessary to slacken the axial fan before the
shield can be removed.
The
Air Baffles
The air baffles are fitted between the cylinder
barrels and extreme care must be taken to ensure
they do not totally block the air flow when they are
refitted.
The baffles can be removed for cylinder fin cleaning
by removing the split pin; it is not necessary to
remove the cylinder heads.
2.06 THE CYLINDER COOLING FINS
The cylinder barrel, head, crankcase and cooling
fan fins must be kept reasonably clean otherwise
seizure of various components can occur because
of overheating.
Cleaning frequency will depend on the nature and
concentration of the substances contained in the
cooling air; fluff hair, vegetable fibre and other such
items have a greater clogging effect than dry dust.
The cooling fins should always be cleaned when
the engine is decarbonised and as necessary.
With the engine stopped, and immobilised, the
contaminants can be raked off the fins by using
a suitable hooked piece of wire or low pressure
compressed air.
WARNING
If compressed air is used extreme care must
be taken to prevent personal injury by the jet
or debris.
2.07 THE AXIAL FAN - TX
A single stage axial flow fan, belt driven from the
gear end forces cooling air to the cylinder heads,
barrel and crankcase external cooling fins.
WARNING
The axial fan belt must be changed every 2000
hours, irrespective of its condition.
Figure 2.5.1 Air Cowling - TS/TR
4. Remove the manifolds.
5. Remove the air cowl by removing the setscrew in the
fanshroud and setscrews, spring and plain washers in the
cowl.
6. If a fuel filter is fitted to the flywheel end shield, isolate or
drain the fuel before disconnecting the fuel feed to the fuel
pumps and remove the nuts and spring washers securing
the fuel filter.
7. Remove the setscrews, spring washers and plain washers
securing the flywheel end shield to the cylinder head top
plate.
A setscrew is fitted in the middle of the filter mounting block.
8. Remove the shield.
Removing the Air Cowling - TX
1. Remove the air cleaner if necessary.
2. Remove the flywheel end air shield.
3. Remove the axial fan cowling.
4. Isolate or drain the fuel before disconnecting the fuel pipes
to and from the fuel filter.
5. Remove the fuel filter.
T SERIES ENGINES WORKSHOP MANUAL
15
3.Replace the glowpiug cable.
4.Replace the axial fan air cowling.
2.5 THE AIR COWLING
Three sides of the engine are encased in an air
cowl and two sides shields, which together with the
air baffle(s) direct cooling air from the flywheel fan
around the cylinders.
Removing the Air Cowling - TS/TR
1.Remove the cold start pots if fitted.
2.Drain the fuel and remove the engine mounted
fuel tank, if fitted.
3.Remove the gear end air shield by removing the
setscrews, spring washers and plain washers in
the top plate and air cowling.
Figure 2.5.1 Air Cowling - TS/TR
4.Remove the manifolds.
5.Remove the air cowl by removing the setscrew
in the fanshroud and setscrews, spring and plain
washers in the cowl.
6.If a fuel filter is fitted to the flywheel end shield,
isolate or drain the fuel before disconnecting the
fuel feed to the fuel pumps and remove the nuts
and spring washers securing the fuel filter.
7.Remove the setscrews, spring washers and plain
washers securing the flywheel end shield to the
cylinder head top plate.
A setscrew is fitted in the middle of the filter
mounting block.
8.Remove the shield.
Removing the Air Cowling - TX
1.Remove the air cleaner if necessary.
2.Remove the flywheel end air shield.
3.Remove the axial fan cowling.
4.Isolate or drain the fuel before disconnecting the
fuel pipes to and from the fuel filter.
5.Remove the fuel filter.
6.Remove the gear end air shield; it may be
necessary to slacken the axial fan before the
shield can be removed.
The
Air Baffles
The air baffles are fitted between the cylinder
barrels and extreme care must be taken to ensure
they do not totally block the air flow when they are
refitted.
The baffles can be removed for cylinder fin cleaning
by removing the split pin; it is not necessary to
remove the cylinder heads.
2.06 THE CYLINDER COOLING FINS
The cylinder barrel, head, crankcase and cooling
fan fins must be kept reasonably clean otherwise
seizure of various components can occur because
of overheating.
Cleaning frequency will depend on the nature and
concentration of the substances contained in the
cooling air; fluff hair, vegetable fibre and other such
items have a greater clogging effect than dry dust.
The cooling fins should always be cleaned when
the engine is decarbonised and as necessary.
With the engine stopped, and immobilised, the
contaminants can be raked off the fins by using
a suitable hooked piece of wire or low pressure
compressed air.
WARNING
If compressed air is used extreme care must
be taken to prevent personal injury by the jet
or debris.
2.07 THE AXIAL FAN - TX
A single stage axial flow fan, belt driven from the
gear end forces cooling air to the cylinder heads,
barrel and crankcase external cooling fins.
WARNING
The axial fan belt must be changed every 2000
hours, irrespective of its condition.
6. Remove the gear end air shield; it may be necessary to slacken
the axial fan before the shield can be removed.
The Air Baffles
The air baffles are fitted between the cylinder barrels and
extreme care must be taken to ensure they do not totally block
the air flow when they are refitted.
The baffles can be removed for cylinder fin cleaning by removing
the split pin; it is not necessary to remove the cylinder heads.
2.6 The Cylinder Cooling Fins
The cylinder barrel, head, crankcase and cooling fan fins must be
kept reasonably clean otherwise seizure of various components
can occur because of overheating.
Cleaning frequency will depend on the nature and concentration
of the substances contained in the cooling air; fluff hair,
vegetable fibre and other such items have a greater clogging
effect than dry dust.
The cooling fins should always be cleaned when the engine
is decarbonised and as necessary. With the engine stopped,
and immobilised, the contaminants can be raked off the
fins by using a suitable hooked piece of wire or low pressure
compressed air.
WARNING
If compressed air is used extreme care must be taken to
prevent personal injury by the jet or debris.
2.7 The Axial Fan - TX
A single stage axial flow fan, belt driven from the gear end
forces cooling air to the cylinder heads, barrel and crankcase
external cooling fins.
WARNING
The axial fan belt must be changed every 2000 hours,
irrespective of its condition.
Removing the Fan
1. Remove the drive guards.
2. Slacken the alternator mounting bolts and move the
alternator as far as it will go towards the crankcase.
Summary of Contents for TS/TR1
Page 1: ...P027 08270 edition 8 April 2021 TS TR TX Engines Workshop Manual T SERIES ...
Page 80: ...TS TR TX engines workshop manual 80 T SERIES ENGINES WORKSHOP MANUAL 90 ct ical Wiring i g ...
Page 85: ...TS TR TX engines workshop manual 85 T SERIES ENGINES WORKSHOP MANUAL 95 ...