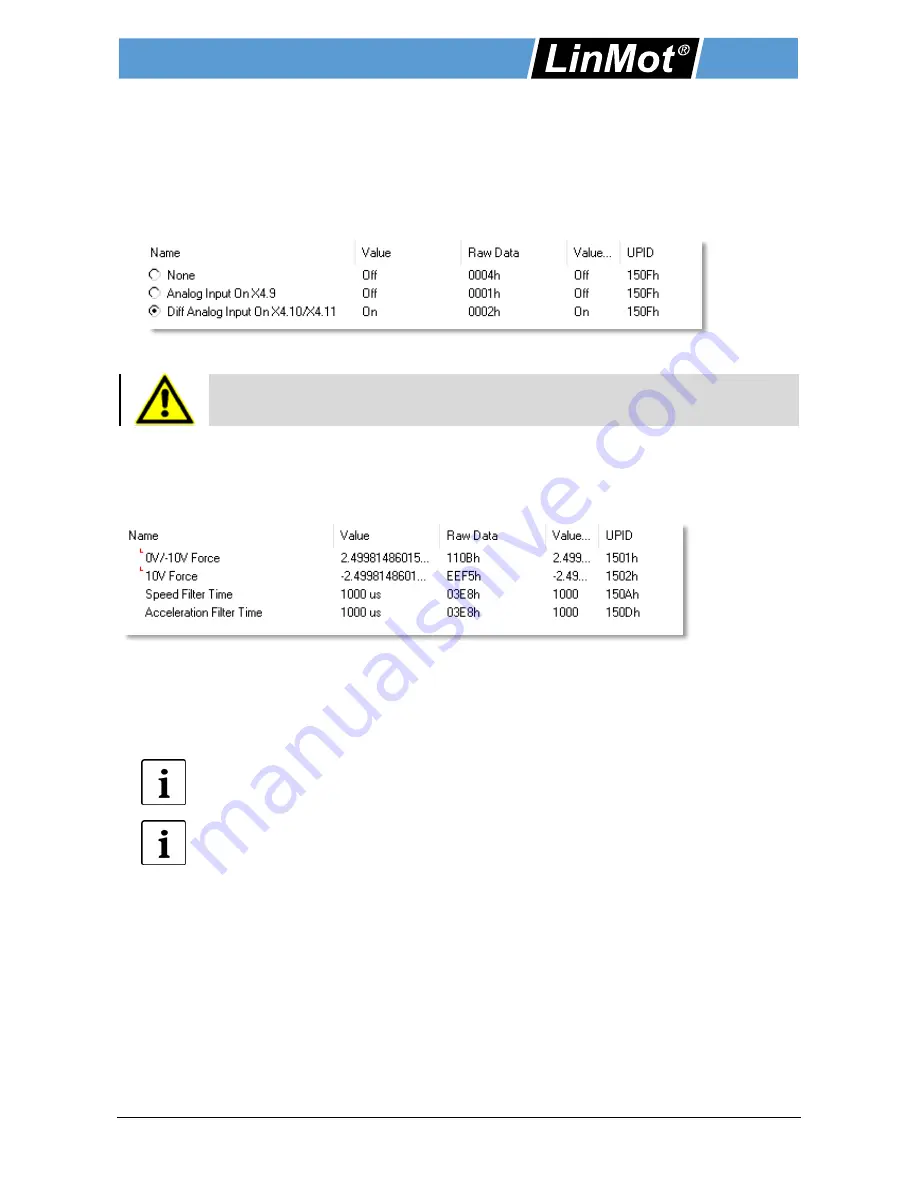
Installation Guide Linear Rotary Motors
ENG
NTI AG / LinMot
PR02-52
Page 13 / 24
5.2.3 Setting the parameters
Logged into the drive, you will find all parameters to be set in the LinMot-Talk software under the path
"Parameters -> Motion Control SW -> Protected Technology Functions -> Analog Force Feedback Control".
Step 1: Input Selection
Please select the following setting under "Input Selection":
Input Selection (UPID 150Fh) = Diff Analog Input On X4.10/X4.11
Step 2: Analog Force Feedback Config
Due to the definition of the DEFAULT positive direction of rotation, it is recommended to use
the +-10VDC signal via software. This means that with -10VDC the positive maximum value
and with +10VDC the negative maximum value of the torque measuring shaft is set.
0V/-10V Force (UPID 1501h)
= Positiver Maximalwert (z.B. 2.5Nm)
10V Force (UPID 1502h)
= Negativer Maximalwert (z.B. -2.5Nm)
Speed Filter Time (UPID 150Ah)
= 1000us
Acceleration Filter Time (UPID 150Dh)
= 1000us
Step 3: Force Control Parameters
The parameters for the torque control loop are set here. A PID controller, a few pilot parameters (FF
parameters) and a parameter for limiting the maximum control current (Force Ctrl Max Current) are available
for this purpose.
Recommendation:
To begin with, work with a pure I-controller to prevent the motor from oscillating during
torque control.
Limit the maximum control current in order to avoid damage if incorrect handling occurs
during commissioning.
6 Appropriate application of the torque measuring shaft
The torque measuring shaft is used to measure static and dynamic torques. The sensor can measure both
right and left load. The measured variable is suitable for control and regulation tasks.
Torque peaks beyond the permissible overload (see specifications in the PR02 data sheet) can lead to the
destruction of the torque measuring shaft. If peaks cannot be safely excluded, they must be intercepted.
The working temperature range of the sensors is 5 - 45 °C. Above or below the limits there is a
measurement error which influences the measurement results.
The max. operating range is between 0 - 80 °C.
For continuously precise measurement results it is recommended to calibrate the torque measuring shaft
every 2 years according to section 8.3.