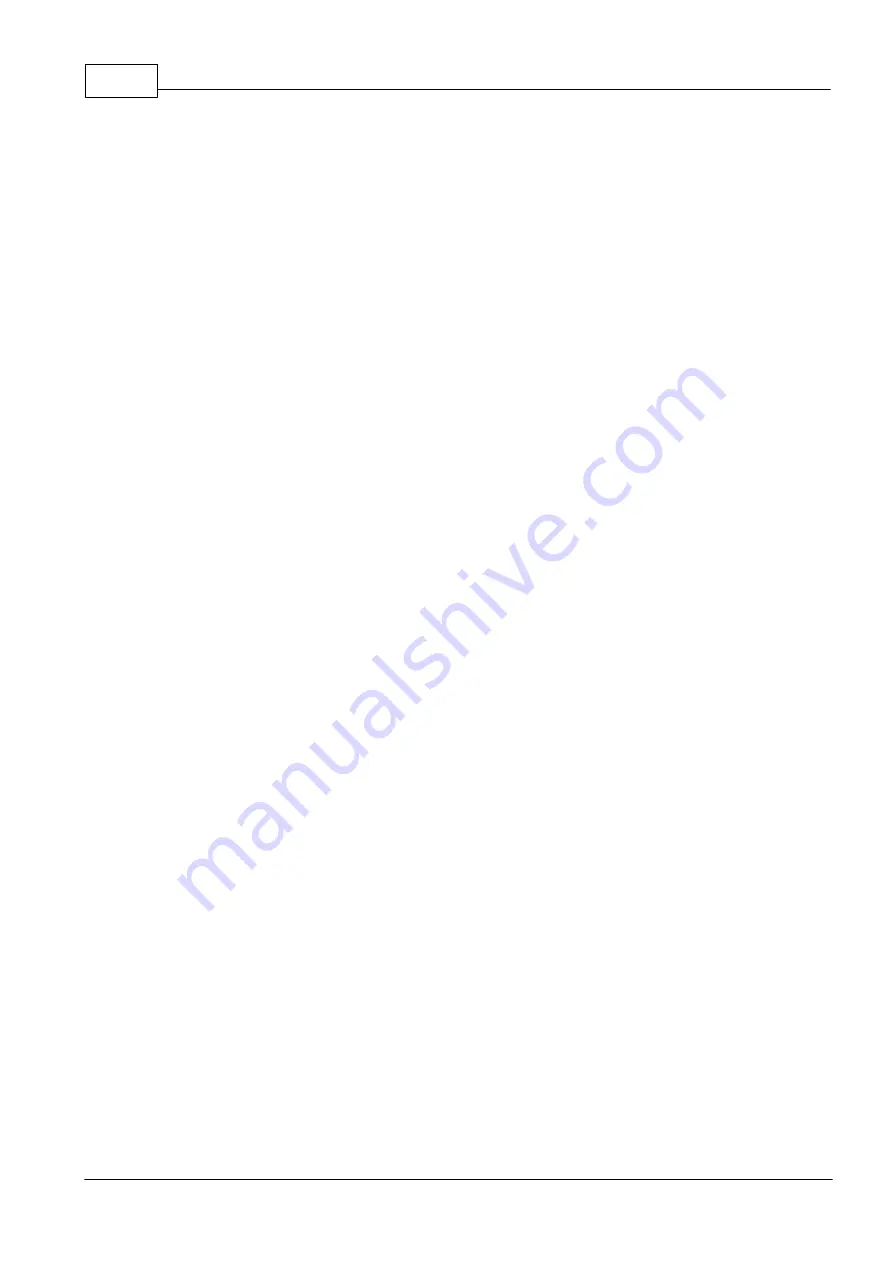
G4 Wiring and Installation Manual
56
© 2009 Link
1. Click on ‘Analogue Channel’.
2. Select the Analogue Channel that is wired to the
MAP sensor.
a. Set the function to ‘MAP Sensor’.
b. Select the correct “MAP Sensor Type’.
c. Ensure the MAP runtime value reads
reasonably close to the barometric pressure
reading (BAP).
d. Perform a MAP Sensor Calibration. Do this by
selecting ‘MAP Sensor Calibration’ from the
Tools menu and following on screen
instructions.
3. Select the Analogue Channel that is wired to the
TPS sensor:
a. Set the function to TPS (main).
b. Perform a TPS Calibration. Do this by selecting
‘TPS Calibration’ from the Tools menu and
following on screen instructions.
4. Set up all other connected Analogue Volt channels
as required.
5. Set unused channels to OFF.
6. Click on the An Temp channel wired to the engine
coolant temperature (ECT sensor).
a. Set the channels function to 'ECT'.
b. Select ‘Temp Sensor Type’. If a custom type
sensor is to be used then the resistance vs.
temperature values should be entered now.
c. Confirm correct reading of the sensor by
opening the Analogue Inputs tab runtime values
(lower area of PCLink Tuning Software screen).
7. Repeat the previous step for all Analogue
Temperature channels.
8. Perform a Store to permanently save changes to
the ECU by pressing F4.
Trigger Set-up
Trigger set-up requires entering information regarding the way in which engine speed and
position is measured. Consult the PCLink Tuning Software online help for further
information on functions.
WARNING!
These are probably the most critical set-up values. Do not
attempt to start the engine unless you are 100% confident that
these values are correct.
If trigger information is unknown, consult your nearest Link dealer for further assistance.