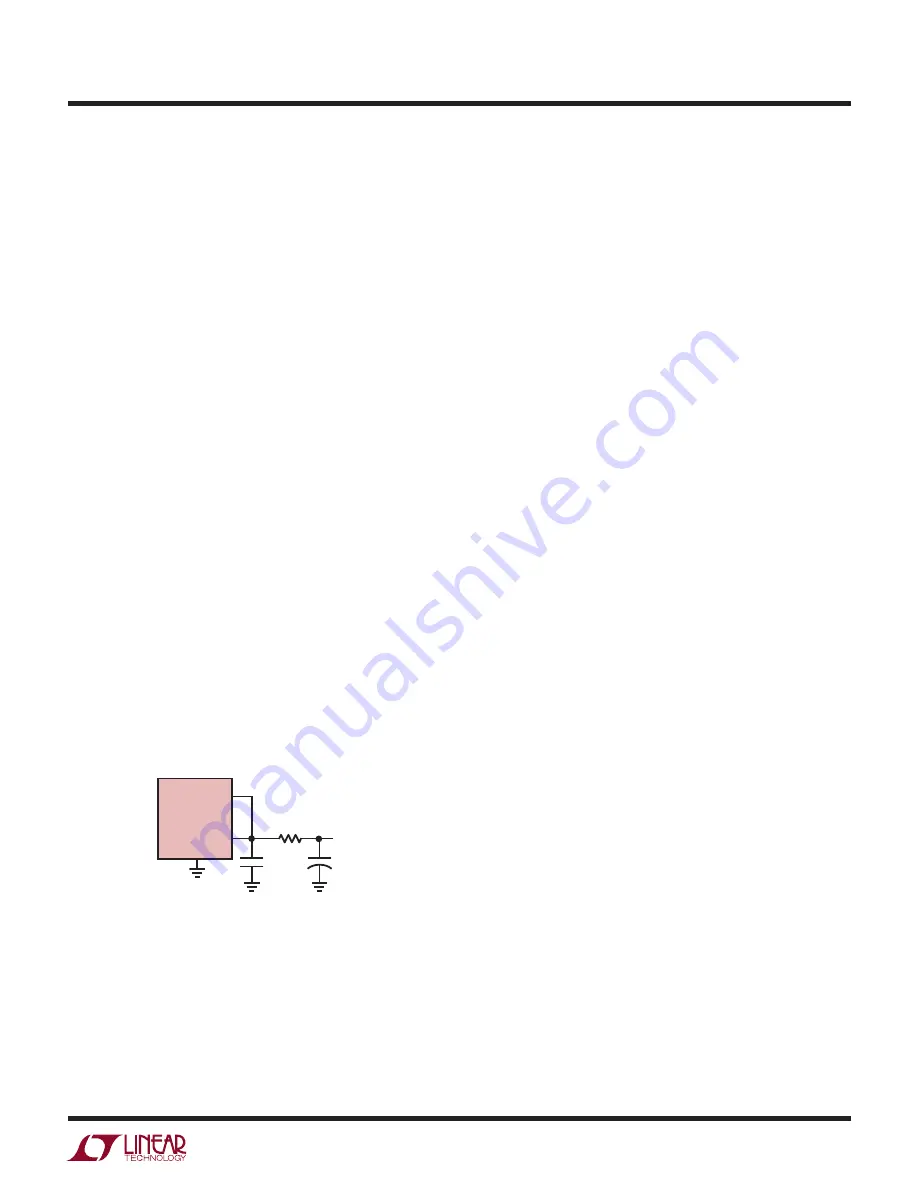
LTC3875
27
3875fb
For more information
www.linear.com/LTC3875
APPLICATIONS INFORMATION
The following list summarizes the four possible connec-
tions for EXTV
CC
:
1. EXTV
CC
left open (or grounded). This will cause INTV
CC
to be powered from the internal 5.5V regulator resulting
in an efficiency penalty at high input voltages.
2. EXTV
CC
connected directly to V
OUT
. This is the normal
connection for a 5V regulator and provides the highest
efficiency.
3. EXTV
CC
connected to an external supply. If a 5V external
supply is available, it may be used to power EXTV
CC
providing it is compatible with the MOSFET gate drive
requirements.
4. EXTV
CC
connected to an output-derived boost network.
For 3.3V and other low voltage regulators, efficiency
gains can still be realized by connecting EXTV
CC
to an
output-derived voltage that has been boosted to greater
than 4.7V.
For applications where the main input power is below 5V,
tie the V
IN
and INTV
CC
pins together and tie the combined
pins to the 5V input with a 1Ω or 2.2Ω resistor as shown
in Figure 11 to minimize the voltage drop caused by the
gate charge current. This will override the INTV
CC
linear
regulator and will prevent INTV
CC
from dropping too low
due to the dropout voltage. Make sure the INTV
CC
voltage
is at or exceeds the R
DS(ON)
test voltage for the MOSFET
which is typically 4.5V for logic level devices.
MOSFET. This enhances the MOSFET and turns on the
topside switch. The switch node voltage, SW, rises to V
IN
and the BOOST pin follows. With the topside MOSFET on,
the boost voltage is above the input supply:
V
BOOST
= V
IN
+ V
INTVCC
– V
DB
where V
DB
is the diode forward voltage drop.
The value of the boost capacitor, C
B
, needs to be 100 times
that of the total input capacitance of the topside MOSFET(s).
The reverse breakdown of the external Schottky diode
must be greater than V
IN(MAX)
. When adjusting the gate
drive level, the final arbiter is the total input current for
the regulator. If a change is made and the input current
decreases, then the efficiency has improved. If there is
no change in input current, then there is no change in
efficiency.
Undervoltage Lockout
The LTC3875 has two functions that help protect the
controller in case of undervoltage conditions. A precision
UVLO comparator constantly monitors the INTV
CC
voltage
to ensure that an adequate gate-drive voltage is present.
It locks out the switching action when INTV
CC
is below
3.7V. To prevent oscillation when there is a disturbance
on the INTV
CC
, the UVLO comparator has 500mV of preci-
sion hysteresis.
Another way to detect an undervoltage condition is to
monitor the V
IN
supply. Because the RUN pins have a
precision turn-on reference of 1.22V, one can use a resistor
divider to V
IN
to turn on the IC when V
IN
is high enough.
An extra 4.5µA of current flows out of the RUN pin once
the RUN pin voltage passes 1.22V. One can program the
hysteresis of the run comparator by adjusting the values
of the resistive divider. For accurate V
IN
undervoltage
detection, V
IN
needs to be higher than 4.5V.
C
IN
and C
OUT
Selection
The selection of C
IN
is simplified by the 2-phase architec-
ture and its impact on the worst-case RMS current drawn
through the input network (battery/fuse/capacitor). It can
be shown that the worst-case capacitor RMS current oc-
curs when only one controller is operating. The controller
with the highest (V
OUT
)(I
OUT
) product needs to be used
INTV
CC
LTC3875
R
VIN
1Ω
C
IN
3875 F11
5V
C
INTVCC
4.7µF
+
V
IN
Figure 11. Setup for a 5V Input
Topside MOSFET Driver Supply (C
B
, D
B
)
External bootstrap capacitor, C
B
, connected to the BOOST
pin supplies the gate drive voltages for the topside MOSFET.
Capacitor C
B
in the Functional Diagram is charged though
external diode D
B
from INTV
CC
when the SW pin is low.
When the topside MOSFET is to be turned on, the driver
places the C
B
voltage across the gate source of the