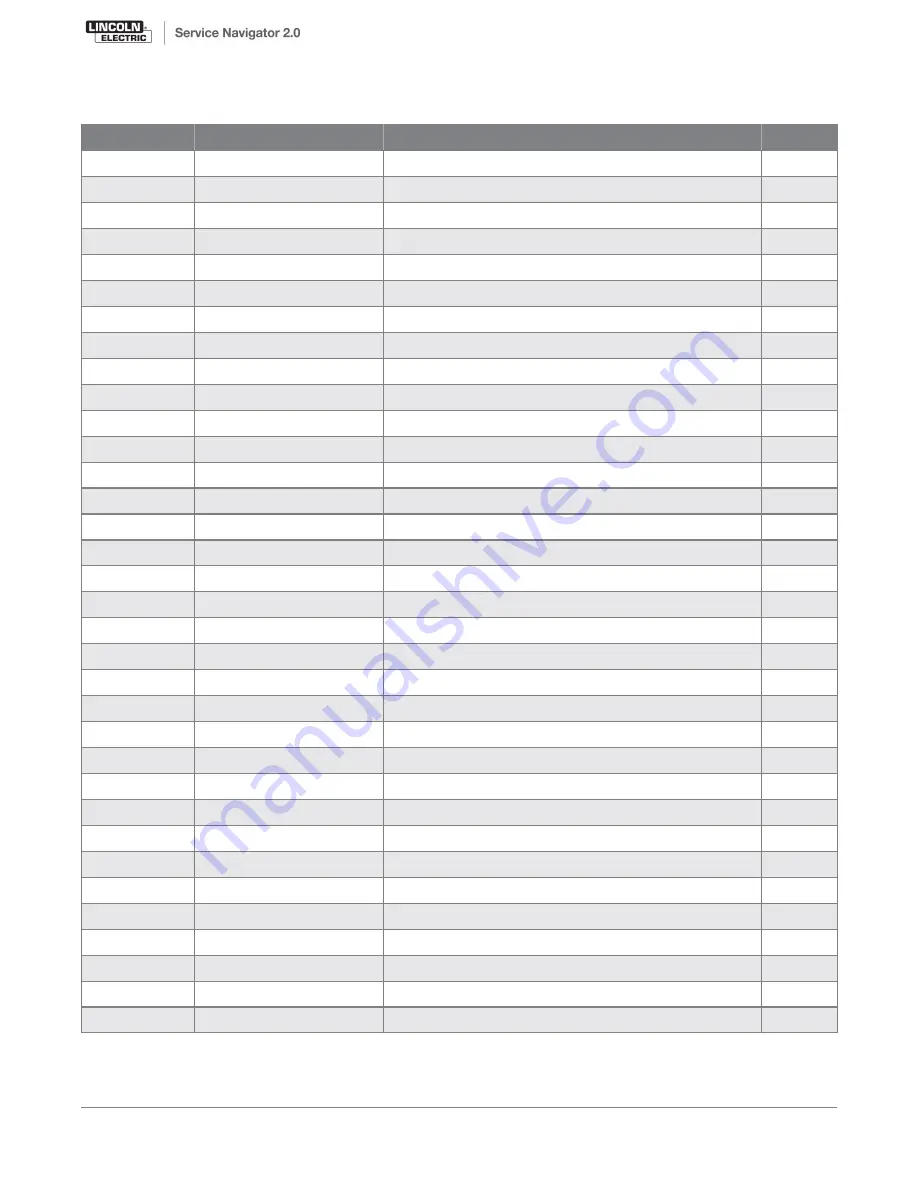
KEY
PART NUMBER
DESCRIPTION
QTY
9SG8388
CASE FRONT ASSEMBLY
1
1
9SG6513-3
CASE FRONT
1
9SM22487-1
LED HARNESS
1
9SS23740-2
LED PANEL MOUNT ASSEMBLY
2
9ST13657-4FA
YELLOW LED
1
9ST13657-7H24
LED-T-1 3/4BI-COLORRED/GREEN
1
3
9SS23093-1
LED LENS CLEAR
2
3A
9SS23094-1
RETAINING O RING
2
4A
9SM20305-1
NOISE SUPPRESSOR PC BD ASBLY
1
4B
9SS28402
NOISE SUPPRESSOR BRACKET
1
9ST9187-13
#10-24HLN-1817/1-NYLON INSERT
2
5A
9SL13263-1
PCB MOUNTING BRACKET
1
9ST9187-13
#10-24HLN-1817/1-NYLON INSERT
2
6A
9SL13263-2
PCB MOUNTING BRACKET
1
9ST9187-13
#10-24HLN-1817/1-NYLON INSERT
2
7A
9SS20030-1
LINE SWITCH
1
7B
9SS25384-1
SWITCH COVER - WEATHER RESISTANT
1
9ST9695-1
LOCKWASHER
2
9SCF000084
#10-32X.625HHCS
2
9SS18491-3
M.O.V. ASBLY
1
15A
9SM13896-9
OUTPUT TERMINAL MOLDING
2
15B
9SS9225-101
SELF TAPPING SCREW
4
16A
9SG6758-1
INPUT CONTROL & POWER SUPPLY PC BD ASBLY
1
9ST9187-13
#10-24HLN-1817/1-NYLON INSERT
3
18
9SG8226
NAMEPLATE
1
19
9ST10397-3
PLUG BUTTON
1
21
9ST10397-23
PLUG BUTTON
1
9SS9225-99
SELF TAPPING SCREW
4
26A
9SS9262-80
PLAIN WASHER
2
26B
9SE106A-15
LOCKWASHER
2
26C
9SCF000021
1/2-13X1.00HHCS
2
30A
9SS18657
SQUARE FLANGE FEMALE RECEPTACLE
1
9SS8025-118
SELF TAPPING SCREW
2
31A
9SL15069
COVER PLATE
1
Case Front Assembly
Power Wave S350 Aluminum - 12371
5
Printed 08/02/2016 at 10:04:29. Produced by Enigma.