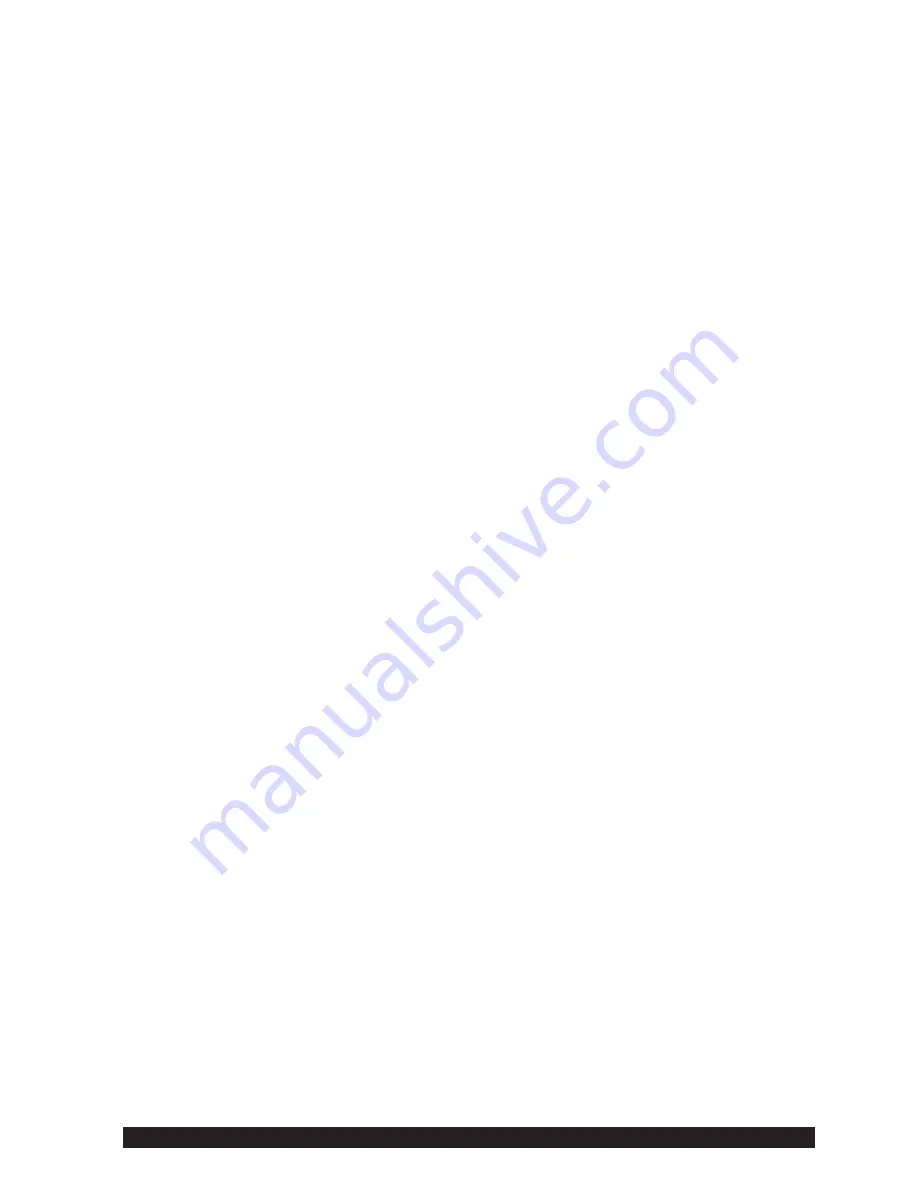
IMA 474
DC-400
Page 11
INPUT LINE VOLTAGE COMPENSATION
The power source is equipped with input line voltage
compensation as standard. For a line voltage fluctuation of
±10% the output will remain essentially constant. This is
accomplished through the feedback network in the control
circuit.
SOLID STATE OUTPUT CONTROL
The output of the welder is electronically controlled by
SCR’s instead of mechanical contactors, providing extra
long life for highly repetitive welding applications.
SOLID STATE CONTROL SYSTEM
The control circuitry consists of six basic circuits: (1) the
SCR snubber network, (2) the SCR firing circuit, (3) the
control/fault protection circuit, (4) the starting circuit, (5) the
power-up delay circuit, and (6) the power circuit.
The SCR snubber board consists of a capacitor and
resistor connected across each SCR and across the entire
bridge and MOV’s to protect the control circuitry and SCR’s
from transient voltages. The snubber board is mounted on
the back of the case front.
The SCR firing circuit, the control fault protection circuit, the
power-up delay circuit, and the power circuit are mounted
on the control PC board located behind the front control
panel.
(The front control panel hinges down for easy
access to the board.) The starting circuit board is located
on the back of the control box.
MACHINE COOLING
The fan pulls air in through the louvered front of the
machine over the internal parts and exhausts out the
louvred rear of the machine.
The fan motor is fully
enclosed, has sealed ball bearings, requires no lubrication,
and operates when the power switch is turned on.
CASE FEATURES
The machine uses a 815mm long base. The low profile
case facilitates installation of the machine under a
workbench and stacking the machines three high to
conserve floor space.
The case front incorporates a recessed control panel
where all the machine controls are mounted. This recessed
panel protects the controls and minimises the possibilities
of accidental contact.
This control panel can be easily
opened to permit access to the enclosed control section
which contains the terminal strips, PC board, etc.
The output lead terminals are also recessed to avoid any
object or person accidentally coming in contact with an
output terminal. Strain relief is provided by holes in the
front of the base. The leads are routed up through these
holes to the output terminals. This prevents any damage of
the output studs or insulation of same in the event the
cables are pulled excessively.
An output stud cover
protects against accidental contact with the output studs.
Cover hinges upward for access to the studs.
The individual case sides are removable for easy access
for internal service or inspection. These are removable
even though the machines are stacked three high.
The case rear, top section, is equipped with a removable
access panel.
This provides easy access to the input
contactor, easy connection and reconnection of input
leads, and easy access for service or inspection.
The total construction of the machine permits outdoor
operation.
The enclosure is designed with air intake
louvres that keep dripping water from being drawn into the
unit. The transformer, SCR bridge assembly, and choke
are double-dipped in a special corrosion resistant coating.
A permanent lifting hook is located at the top of the
machine and is positioned so that it acts as nearly as
possible through the centre of gravity. This lift hook is so
positioned that it fits without interference under the base of
the second machine when stacking.
ARC FORCE SELECTOR
(Effective only on CC for Stick and TIG Processes)
An ARC FORCE selector is provided similar to that used on
the R3R. This control allows the user to select the ideal arc
force for the procedure and electrode being used.
ARC CONTROL
(Effective Only When Using CVI Mode)
The ARC CONTROL is a five-position switch that changes
the pinch effect of the arc. This results in the control of
spatter, fluidity, and bead shape. The ARC CONTROL is
set to provide optimum welding depending on the process
being used, position, electrode, etc. The pinch effect is
increased by turning the control clockwise and may be
adjusted while the machine is in operation.
MODE SWITCH
A MODE SWITCH selects between Constant Voltage
(FCAW/GMAW), Constant Voltage (Submerged Arc) and
Constant Current (Stick/TIG).
STICK WELDING
When the DC-400 is used for stick welding or air carbon
arc, the control leads and welding cables to any
semiautomatic or automatic wire feeders must be
disconnected from the DC-400 for maximum safety (unless
the Multi-Process switch option is installed).
PARALLELING
There are no provisions on the DC-400 to permit
paralleling.
DIODE OPTION
The DC-400 Diode option is required to utilise the cold start
and cold electrode sensing features of the NA-3, NA-5 or
NA-5R. When this option is not used with an NA-3, NA-5
or NA-5R, see the DC-400/NA-3, DC-400/NA-5 or DC-
400/NA-5R connection diagram for instructions on how to
disable this circuit. If the circuit is not disabled, the wire
cannot be inched down.
ARC WELDING SUPPLIES - 07 847 7870