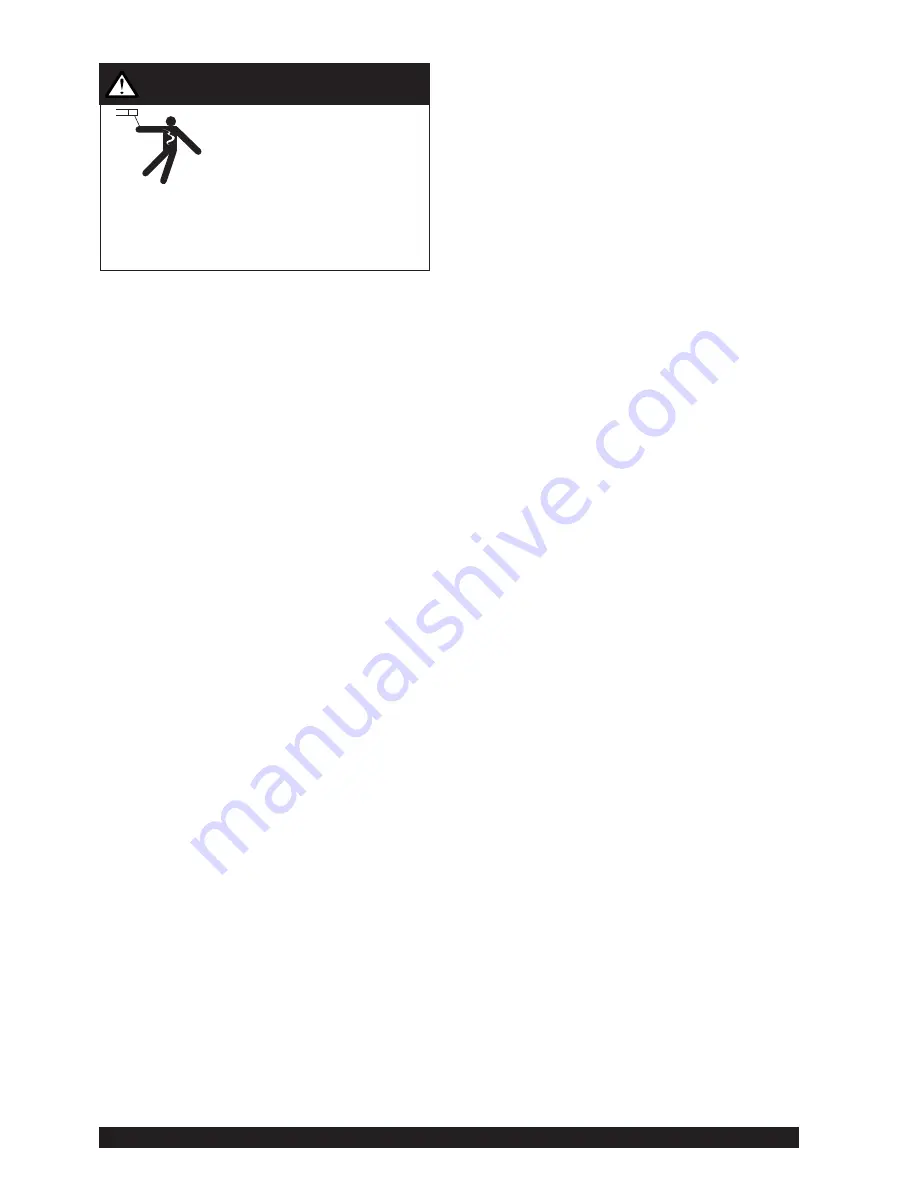
PROCEDURE FOR REPLACING PC BOARDS
When a PC Board is suspected to be defective, the
following procedure must be followed:
1. Visually inspect the PC Board. If the board has fuses,
check to see if any are blown. Are any of the
components damaged? Is a conductor on the back
side of the board damaged? If electrical damage is
visible on the PC Board, inspect the machine wiring for
grounds or shorts to avoid damaging a new PC Board,
Install a new PC Board only after a visual inspection of
the PC Board and machine wiring is satisfactory.
2. If the problem is remedied by a new PC Board, install
the old PC Board and see if the problem still exists. If
the problem does not return with the old board:
a)
Check the PC Board harness plug and PC Board
plug for contamination, corrosion or oversize.
b)
Check leads in the harness for loose connections.
CONNECTING THE REMOTE CONTROL TO THE
MACHINE
Extreme caution must be observed when installing or
extending the wiring of a remote control. Improper
connection of this unit can lead to failure of the output
control rheostat or the control circuit. Only the green/yellow
lead can and should be grounded to the machine case.
When extending the standard remote control, make sure
the leads are the same size and the splice is waterproof.
Be very careful not to ground the cable when in use and
don’t let the lugs touch against the case.
OUTPUT VOLTAGE
The output circuit voltage of the machine should be
adjustable from 10 to 46 volts in CV. In the CC mode, the
open circuit voltage should be approximately 57 volts
except at near minimum settings of the output control
where it may be lower. If any other condition exists, refer to
the Troubleshooting Guide.
FAULT PROTECTION OPERATION
The overload protection circuit, in the Control PC Board will
limit the welding current (heat) to 150 amps if a short or
overload is applied to the machine. (Refer to the Machine
and Circuit Protection section).
CHECKING SNUBBER CIRCUIT
In case of an SCR malfunction or failure the snubber
assembly should be checked. Turn the machine off and
remove the sides of the machine.
(See the instruction
manual parts list for the exact location).
Visually inspect the snubber assembly for overheated
components or damaged components.
CHECKING OUTPUT CONTROL RHEOSTAT ON
MACHINE
Turn machine off (“0” position).
Remove the control panel screws and open the control
panel (see the section on Terminal Strip Connections for
screw locations).
Turn the OUTPUT CONTROL switch to “REMOTE”.
Disconnect the harness plug from the Control PC Board.
With an ohmmeter on X1K, connect it to lead 210 and 75
on R4 and rotate the rheostat. The resistance reading
should go from zero to 10K ohms.
Repeat with ohmmeter across 210 + 211 with same result.
Connect across 75 + 211. The reading should be 10K
ohms. A lower reading will indicate a shorted or partially
shorted rheostat. A very high reading will indicate an open
rheostat. In either of the last two cases, replace rheostat.
Exercise caution to avoid damaging POT taps.
POWER “I/0” SWITCH CHECK
1. Turn off the machine power input (“0” position). S1 has
115V across it when the input power is connected.
2. Isolate the switch to be tested by removing all
connecting leads.
3. Check to make sure the switch is making connections
with an ohmmeter.
The meter should read zero
resistance.
4. Put the ohmmeter on X1K scale and measure the
resistance between the terminal and the case of the
machine (touch a self-tapping screw). Reading should
be infinite.
5. If either step (3) or step (4) fails, replace the switch.
REMOTE CONTROL CHECK
Disconnect the remote output control and connect an
ohmmeter across 75 to 76 and rotate the rheostat in the
remote control. The resistance reading should go from
zero to 10K ohms. Repeat with ohmmeter across 75 and
76 with same results. Connect ohmmeter across 75 and
77. The reading should be 10K ohms. A lower reading will
indicate a shorted or partially shorted rheostat. A very high
reading will indicate an open rheostat. In either of the last
two cases, replace rheostat. Check cable for any physical
damage.
Page 24
DC-400
IMA 474
ELECTRIC SHOCK can kill
•
Have an electrician install and service this equipment.
•
Turn the input power off at the fuse box before working
on equipment.
•
Do not touch electrically hot parts.
WARNING
ARC WELDING SUPPLIES - 07 847 7870