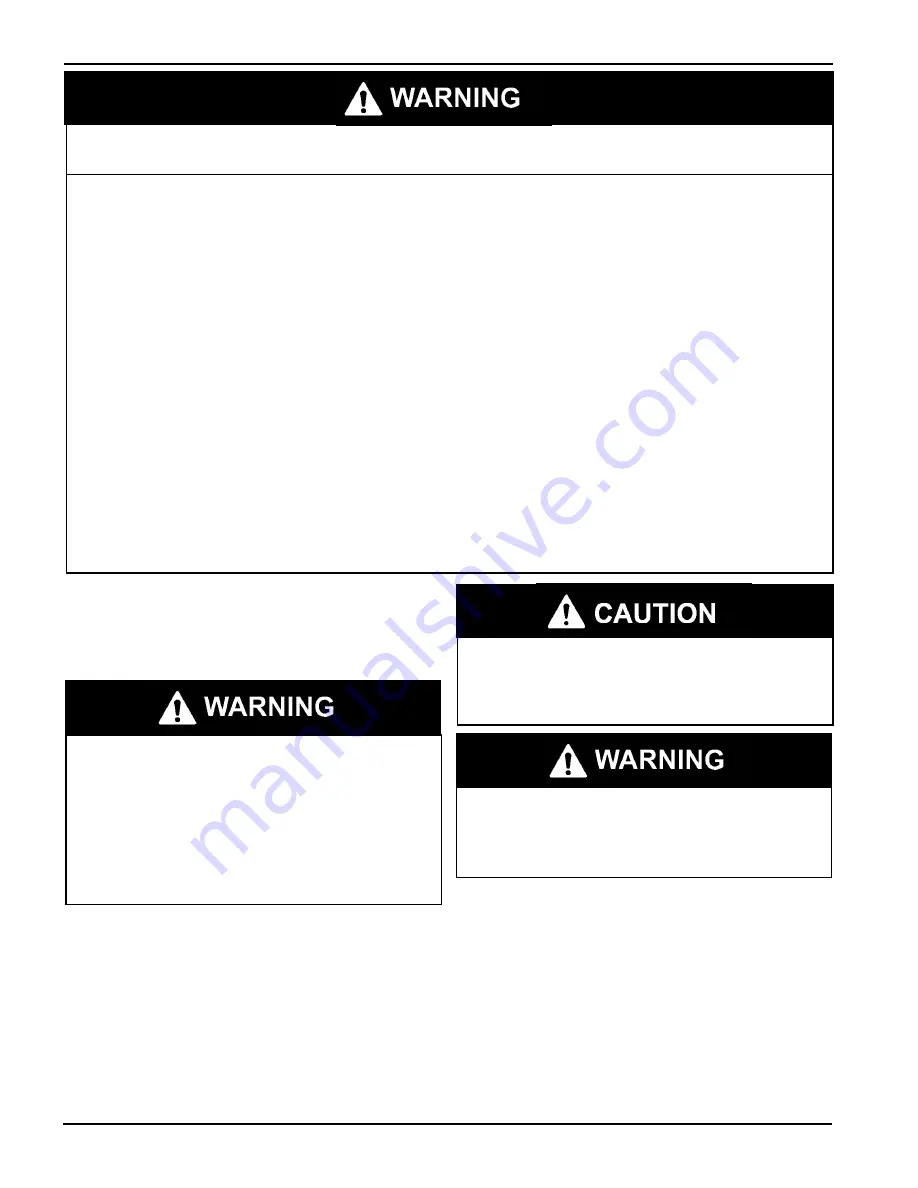
Page Number - 2
Form 403230
FAILURE TO HEED THE FOLLOWING WARNINGS INCLUDING MISUSE, OVER PRESSURIZING, MODIFYING PARTS,
USING INCOMPATIBLE CHEMICALS AND FLUIDS, OR USING WORN OR DAMAGED PARTS, MAY RESULT IN EQUIPMENT
DAMAGE AND/OR SERIOUS PERSONAL INJURY, FIRE, EXPLOSION, OR PROPERTY DAMAGE.
·
Do not exceed the stated maximum working pressure of the pump, or of the lowest rated component in your system.
·
Do not alter or modify any part of this equipment.
·
Do not operate this equipment with combustible gas.
·
Do not attempt to repair or disassemble the equipment while the system is pressurized.
·
Make sure all grease connections are securely tightened before using this equipment.
·
Always read and follow the grease manufacturers recommendations regarding grease compatibility, and the use of
protective clothing and equipment.
·
Check all equipment regularly and repair or replace worn or damaged parts immediately.
·
Never point the dispensing valve at any part of the body or at another person.
·
Never try to stop or deflect material from dispensing valve or leading connection or component with your hand or body.
·
Always check equipment for proper operation before each use, making sure safety devices are in place and operating
properly.
·
Always follow the pressure relief procedure after shutting off the pump, when checking or servicing any part of the system,
and when installing, cleaning or changing any part of the system.
INSTALLATION
Typical drum and pail hookups are described as follows
only as a guide in selecting and installing a system.
Contact a Lincoln factory representative for assistance in
designing a system for a specific requirement.
This pump can develop 7500 PSI working pressure at
150 PSI maximum incoming air pressure. Be sure that all
system equipment and accessories are rated to with-
stand the maximum working pressure of this pump.
DO NOT exceed the maximum working pressure of the
lowest rated component in the system.
IMPORTANT: Accessory item whip hoses for dispensing
valve are rated 4500 PSI. DO NOT exceed 90 PSI air
pressure to pump when using whip hoses.
TYPICAL SYSTEM HOOKUP
Determine the drum or pail system for your requirement.
Obtain an air line filter/regulator/lubricator to use with the
inlet air supply and the correct sized air and grease lines
hoses with any required reducers, connectors and accesso-
ries.
Clean/flush the supply lines, hoses, reducers, connectors
and accessories with mineral spirits or oil based solvent to
purge any contaminants such as dirt, moisture, or metal
shavings that could damage the pump or system
components. Blow dry with air.
The pump was tested in lightweight oil which was left in
to protect the pump from corrosion. Flushing the pump
before connecting it to the system might be desired to
prevent possible contamination of the grease you are
pumping.
To reduce the risk of injury from splashing or static
sparking when flushing the pump with solvents, always
hold a metal part of the dispensing valve firmly to the
side of a grounded metal pail and operate pump at
lowest possible fluid pressure.
Clean/flush the pump with mineral spirits or oil based sol-
vents if necessary.
Assemble the cleaned pump and supply line together with
any required accessory.
Mount the assembled pump to the drum or pail.
Connect the material output line/hose to the pump.
Connect the air regulator to the pump.
Make sure all connections are securely tightened.