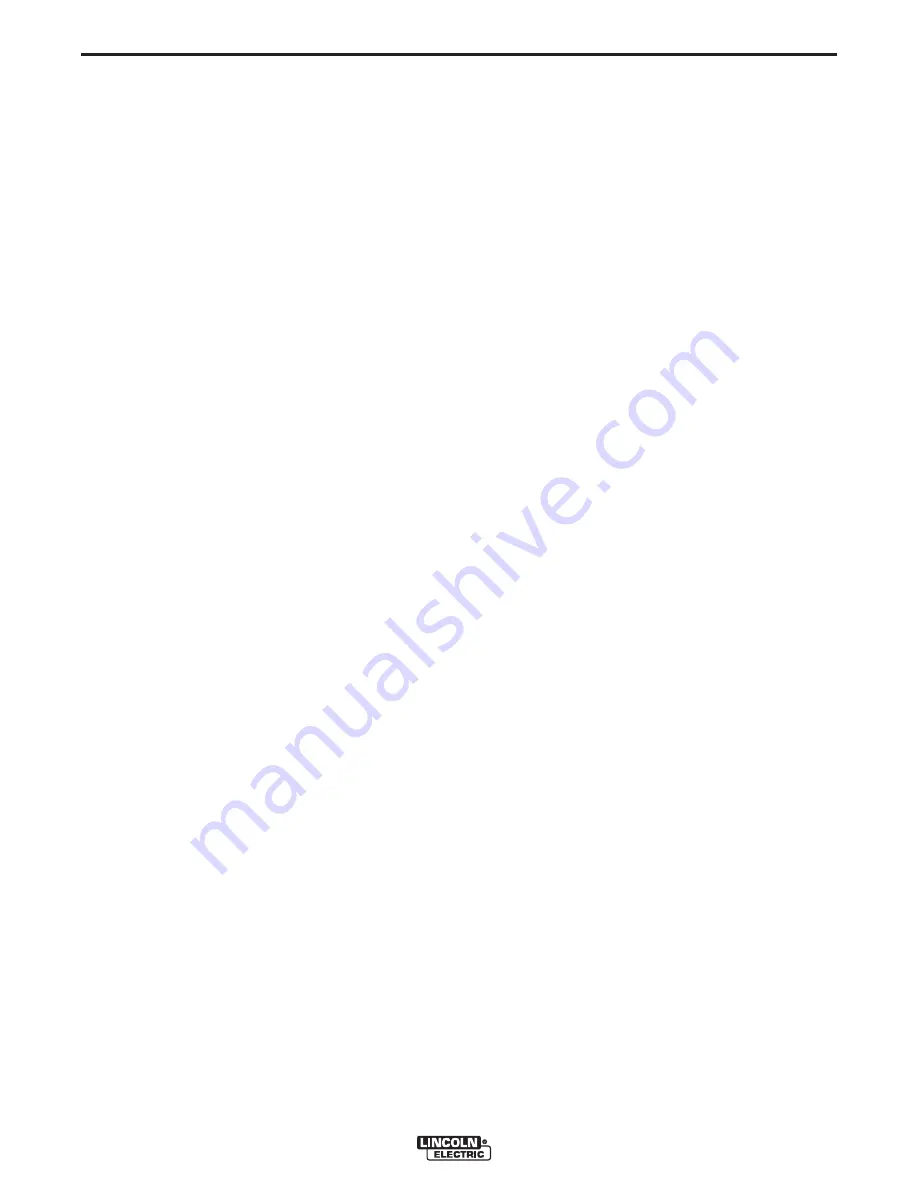
A-7
INSTALLATION
VANTAGE® 580
A-7
CONNECTION OF LINCOLN ELECTRIC
WIRE FEEDERS
Connection of LN-7 or LN-8 to the VANTAGE® 580
1. Shut the welder off.
2. Connect the LN-7 or LN-8 per instructions on the
appropriate connection diagram in Section F.
3. Set the "WIRE FEEDER VOLTMETER" switch to
either "+" or "-" as required by the electrode being
used.
4. Set the "MODE" switch to the "CV WIRE " posi-
tion.
5. Set the "ARC CONTROL" knob to "0" initially and
adjust to suit.
6. Set the "WELD TERMINALS" switch to the
"REMOTELY CONTROLLED" position.
7. Set the "IDLE" switch to the "HIGH" position.
Connection of LN-15 to the VANTAGE® 580
1. Shut the welder off.
2.
For electrode Positive, connect the electrode
cable to the "+" terminal of the welder and work
cable to the "-" terminal of the welder. For elec-
trode Negative, connect the electrode cable to the
"-" terminal of the welder and work cable to the "+"
terminal of the welder.
3. Across The-Arc Model:
• Attach the single lead from the front of the LN-15
to work using the spring clip at the end of the
lead. This is a control lead to supply current to
the wire feeder motor; it does not carry welding
current.
• Set the "WELD TERMINALS" switch to "WELD
TERMINALS ON".
• When the gun trigger is closed, the current sens-
ing circuit will cause the VANTAGE® 580 engine
to go to the high idle speed, the wire will begin to
feed and the welding process started. When
welding is stopped, the engine will revert to low
idle speed after approximately 12 seconds
unless welding is resumed.
4. Control Cable Model:
• Connect Control Cable between Engine Welder
and Feeder.
• Set the "WELD TERMINALS" switch to
"REMOTELY CONTROLLED"
• Set the MODE switch to the "CV-WIRE " position.
• Set the "WIRE FEEDER VOLTMETER" switch to
either "+" or "-" as required by the electrode polar-
ity being used.
• Set the "ARC CONTROL" knob to "0" initially and
adjust to suit.
• Set the "IDLE" switch to the "AUTO" position.
• When the gun trigger is closed, the current sens-
ing circuit will cause the VANTAGE® 580 engine
to go to the high idle speed, the wire will begin to
feed and the welding process started. When
welding is stopped, the engine will revert to low
idle speed after approximately 12 seconds unless
welding is resumed.
Summary of Contents for VANTAGE 580
Page 40: ...F 1 DIAGRAMS F 1 VANTAGE 580...
Page 41: ...F 2 DIAGRAMS F 2 VANTAGE 580...
Page 42: ...F 3 DIAGRAMS F 3 VANTAGE 580...
Page 43: ...F 4 DIAGRAMS F 4 VANTAGE 580...
Page 44: ...F 5 DIAGRAMS F 5 VANTAGE 580...
Page 45: ...F 6 DIAGRAMS F 6 VANTAGE 580...
Page 46: ...F 7 DIAGRAMS F 7 VANTAGE 580...
Page 47: ...F 8 DIAGRAMS F 8 VANTAGE 580 2 9 0 3 2 9 03...
Page 48: ...F 9 DIAGRAMS F 9 VANTAGE 580...