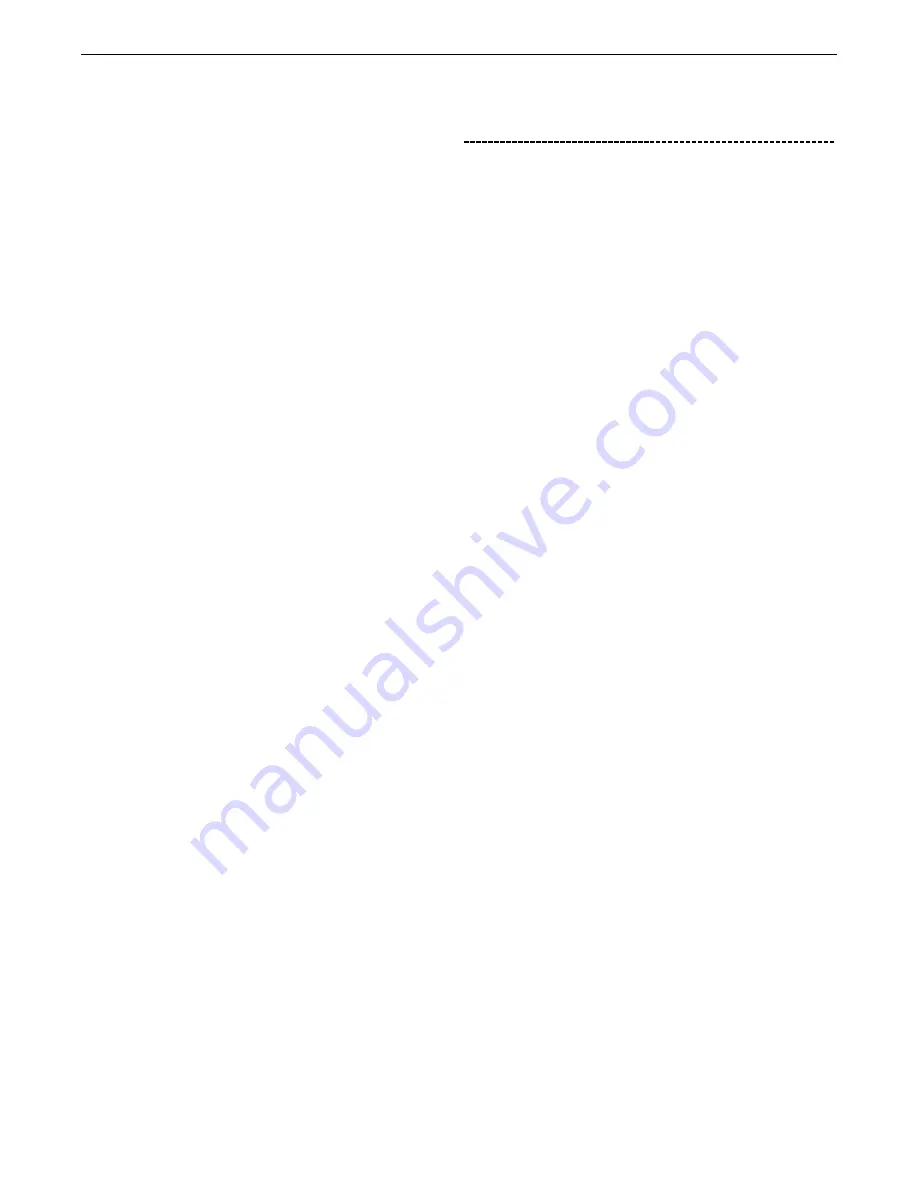
2
SAFETY
STATIFLEX
®
800
As a rule of thumb, for many mild steel electrode, if the air is
visibly clear and you are comfortable, then the ventilation is
generally adequate for your work. The most accurate way to
determine if the worker exposure does not exceed the applicable
exposure limit for compounds in the fumes and gases is to have
an industrial hygienist take and analyze a sample of the air you
are breathing. This is particularly important if you are welding with
stainless, hardfacing or Special Ventilation products. All Lincoln
MSDS have a maximum fume guideline number. If exposure to
total fume is kept below that number, exposure to all fume from
the electrode (not coatings or plating on the work) will be below
the TLV.
There are steps that you can take to identify hazardous
substances in your welding environment. Read the product label
and material safety data sheet for the electrode posted in the work
place or in the electrode or flux container to see what fumes can
be reasonably expected from use of the product and to determine
if special ventilation is needed. Secondly, know what the base
metal is and determine if there is any paint, plating, or coating that
could expose you to toxic fumes and/or gases. Remove it from the
metal being welded, if possible. If you start to feel uncomfortable,
dizzy or nauseous, there is a possibility that you are being
overexposed to fumes and gases, or suffering from oxygen
deficiency. Stop welding and get some fresh air immediately.
Notify your supervisor and co-workers so the situation can be
corrected and other workers can avoid the hazard. Be sure you
are following these safe practices, the consumable labeling and
MSDS to improve the ventilation in your area. Do not continue
welding until the situation has been corrected.
NOTE: The MSDS for all Lincoln consumables is available on Lincoln’s web-
site: www.lincolnelectric.com
Before we turn to the methods available to control welding fume
exposure, you should understand a few basic terms:
Natural Ventilation
is the movement of air through the
workplace caused by natural forces. Outside, this is usually the
wind. Inside, this may be the flow of air through open windows
and doors.
Mechanical Ventilation
is the movement of air through the
workplace caused by an electrical device such as a portable fan
or permanently mounted fan in the ceiling or wall.
Source Extraction
(Local Exhaust) is a mechanical device used
to capture welding fume at or near the arc and filter conta-
minants out of the air.
The ventilation or exhaust needed for your application depends
upon many factors such as:
• Workspace volume
• Workspace configuration
• Number of welders
• Welding process and current
• Consumables used (mild steel, hardfacing, stainless, etc.)
• Allowable levels (TLV, PEL, etc.)
• Material welded (including paint or plating)
• Natural airflow
Your work area has adequate ventilation when there is enough
ventilation and/or exhaust to control worker exposure to
hazardous materials in the welding fumes and gases so the
applicable limits for those materials is not exceeded. See chart of
TLV and PEL for Typical Electrode Ingredients, the OSHA PEL
(Permissible Exposure Limit), and the recommended guideline, the
ACGIH TLV (Threshold Limit Value), for many compounds found in
welding fume.
Ventilation
There are many methods which can be selected by the user to
provide adequate ventilation for the specific application. The
following section provides general information which may be
helpful in evaluating what type of ventilation equipment may be
suitable for your application. When ventilation equipment is
installed, you should confirm worker exposure is controlled within
applicable OSHA PEL and/or ACGIH TLV. According to OSHA
regulations, when welding and cutting (mild steels), natural
ventilation is usually considered sufficient to meet requirements,
provided that:
1. The room or welding area contains at least 10,000 cubic feet
(about 22' x 22' x 22') for each welder.
2. The ceiling height is not less than 16 feet.
3. Cross ventilation is not blocked by partitions, equipment, or
other structural barriers.
4. Welding is not done in a confined space.
Spaces that do not meet these requirements should be equipped
with mechanical ventilating equipment that exhausts at least 2000
CFM of air for each welder, except where local exhaust hoods or
booths, or air-line respirators are used.
Important Safety Note:
When welding with electrodes which require special
ventilation such as stainless or hardfacing (see
instructions on container or MSDS) or on lead or
cadmium plated steel and other metals or coatings which
produce hazardous fumes, keep exposure as low as
possible and below exposure limit values (PEL and TLV)
for materials in the fume using local exhaust or
mechanical ventilation. In con ned spaces or in some
circumstances, for example outdoors, a respirator may
be required if exposure cannot be controlled to the PEL
or TLV. (See MSDS and chart of TLV and PEL for Typical
Electrode Ingredients.) Additional precautions are also
required when welding on galvanized steel.