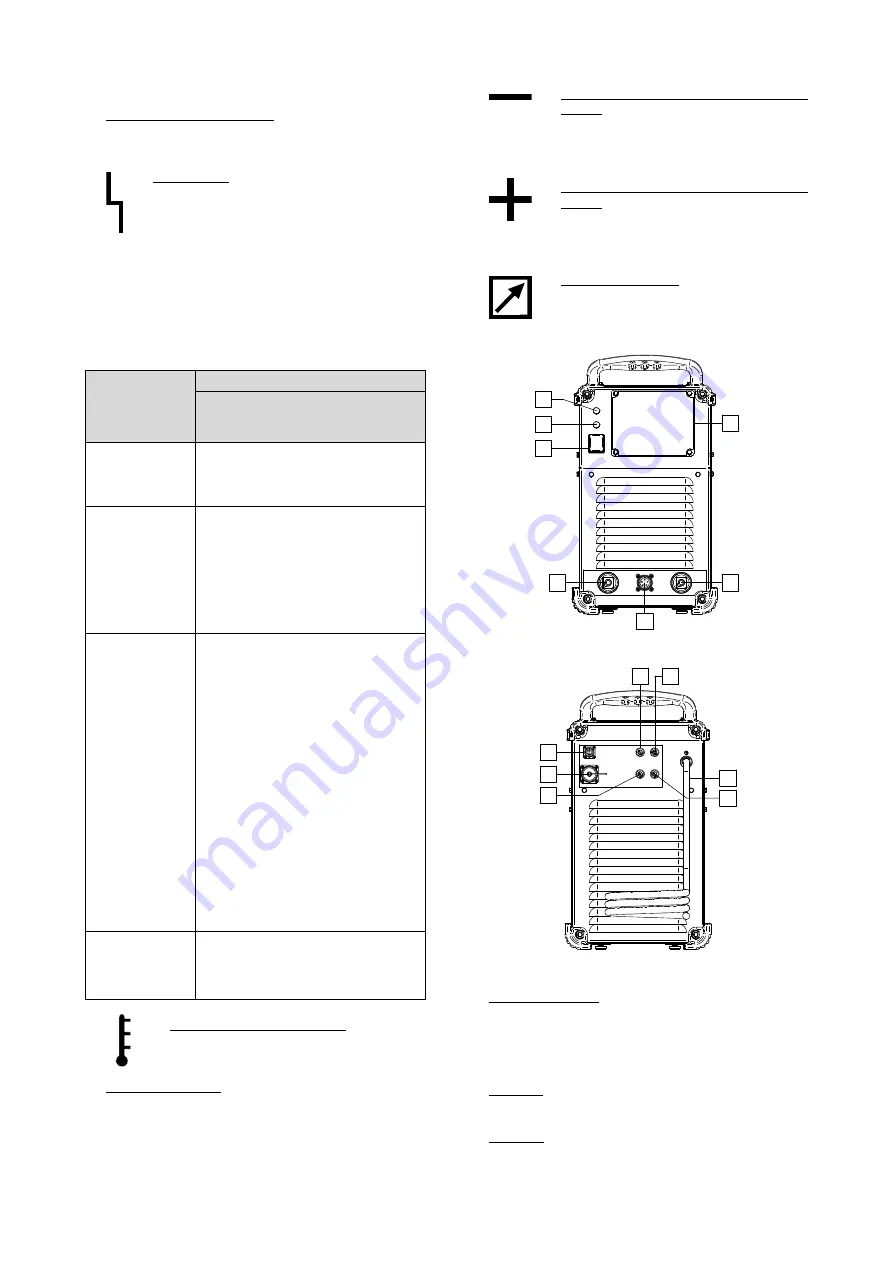
English 9 English
Controls and Operational Features
1. Power Switch ON/OFF (I/O): Controls the input power.
Be sure the power source is properly connected to the
mains supply before turning power on ("I").
2. Status Light: A two color light that indicates
system errors. Normal operation is steady
green light. Error conditions are indicated, per
Table 1.
NOTE:
The status light will flash green, and sometimes
red and green, for up to one minute when the machine is
first turned on. When the power source is powered it can
take as long as 60 seconds for the machine to be ready to
weld. This is a normal situation as the machine goes
through initialization.
Table 1.
LED Light
Condition
Meaning
Only machines which using
ArcLink
®
protocol for
communication
Steady Green
System OK. Power source is
operational, and is communicating
normally with all healthy peripheral
equipment.
Blinking Green
Occurs during power up or a system
reset, and indicates the power source
is mapping (identifying)
each component in the system.
Normal for first 1-10 seconds after
power is turned on, or if the system
configuration is changed during
operation.
Alternating Green
and Red
If the status lights are flashing any
combination of red and green, errors
are present in the power source.
Individual code digits are flashed in
red with a long pause between digits.
If more than one code is present, the
codes will be separated by green light.
Read the error code before the
machine is turned off.
If occurs, to clear the error try to turn
Off the machine, wait for a few
seconds, then turn ON again. If the
error remains, a maintenance is
required. Please contact the nearest
authorized technical service center or
Lincoln Electric and report the error
code read.
Steady Red
Indicate no communication between
the power source and device which
has been connected to this power
source.
3. Thermal Overload Indicator: It indicates
that the machine is overloaded or that the
cooling is not sufficient.
4. Replaceable Panel: User Interface can be installed, in
place of the replaceable panel, which allows to adjust
the welding parameters from the power source. Panel
with User Interface Kit can be purchased separately
(see "Accessories" chapter).
5. Negative Output Socket for the Welding
Circuit: Depending on the configuration of
power source, for connecting a work lead,
the electrode holder with lead or the source/wire
feeder welding cable.
6. Positive Output Socket for the Welding
Circuit: Depending on the configuration of
power source, for connecting a work lead,
the electrode holder with lead or the source/wire
feeder welding cable..
7. Control Receptacle: 5 pins receptacle for
wire feeder or remote controller
connection. To communication wire
feeder or remote controller with power
source is used ArcLink
®
protocol.
1
3
4
5
6
7
2
Figure 1.
8
14
9
10
13
12
11
Figure 2.
8. Power lead (5m): Connect the supply plug to the
existing input cable that is rated for the machine as
indicated in this manual, and conforms to all applicable
standards. This connection shall be performed by a
qualified person only.
9. Fuse F3: Use the 12,5A/400V (6,3x32mm) slow-blow
fuse. See "Spare Parts" chapter.
10. Fuse F4: Use the 6,3A/400V (6,3x32mm) slow-blow
fuse. See "Spare Parts" chapter.