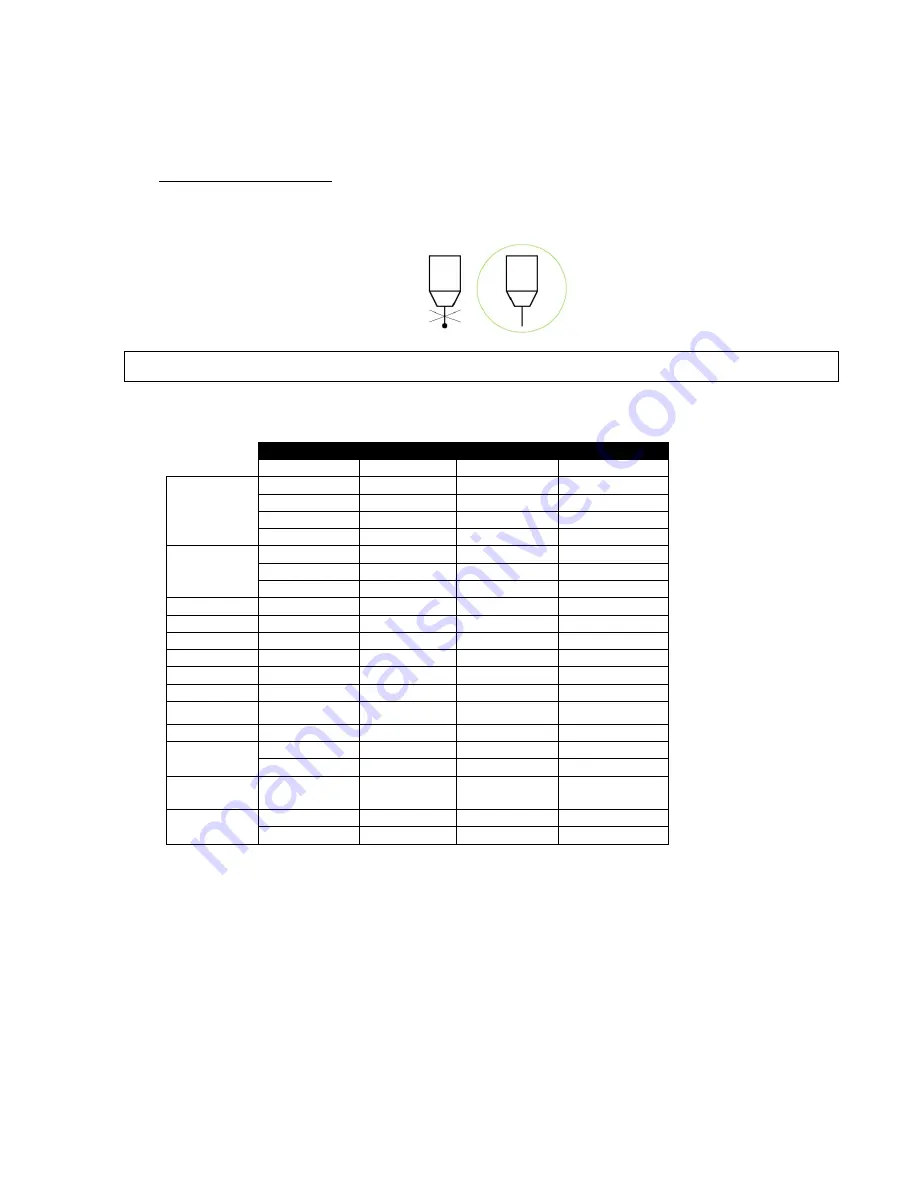
English 17 English
In Smooth mode (short arc), lowering the fine-tune setting enables achieving a more dynamic transfer mode and the
possibility of welding while reducing the energy carried to the weld pool by shortening the arc length.
A higher fine-tune setting causes an increase in arc length. A more dynamic arc facilitates welding in all positions, but has
the disadvantage of causing more spatters.
PR-spray or wire sharpening
The end of welding cycles can be modified to prevent the formation of a ball at the end of the wire. This wire operation
produces almost
perfect restriking. The selected solution consists in injecting a current peak at end of cycle, which causes the wire end to
become pointed.
Note:
This current peak at end of cycle is not always desirable. For instance, when welding thin sheet metal, such this
mechanism can cause a crater.
List of synergies
SHORT ARC
0.6 mm
0.8 mm
1 mm
1.2 mm
Steel
M21 M21 M21 M21
M14 M14 M14 M14
M20 M20 M20 M20
/ C1 C1 C1
CrNi
/ M11
M11 M11
/ M12
M12 M12
/ M12
M12 M12
AlSi / / I1 I1
Al / / / I1
AlMg3 /
/
I1
I1
AlMg4,5 Mn
/
/
I1
I1
AlMg5 /
/
I1
I1
Cupro SI
/
I1
I1
I1
Cupro Alu
/ / I1 I1
F CAW
/
/
M21
M21
RCW
SD 100
/ /
M21
M21
/ / C1 C1
MCW :
SD 200
/ /
M21
M21
BCW :
SD 400
/ / / M21
/ / / C1