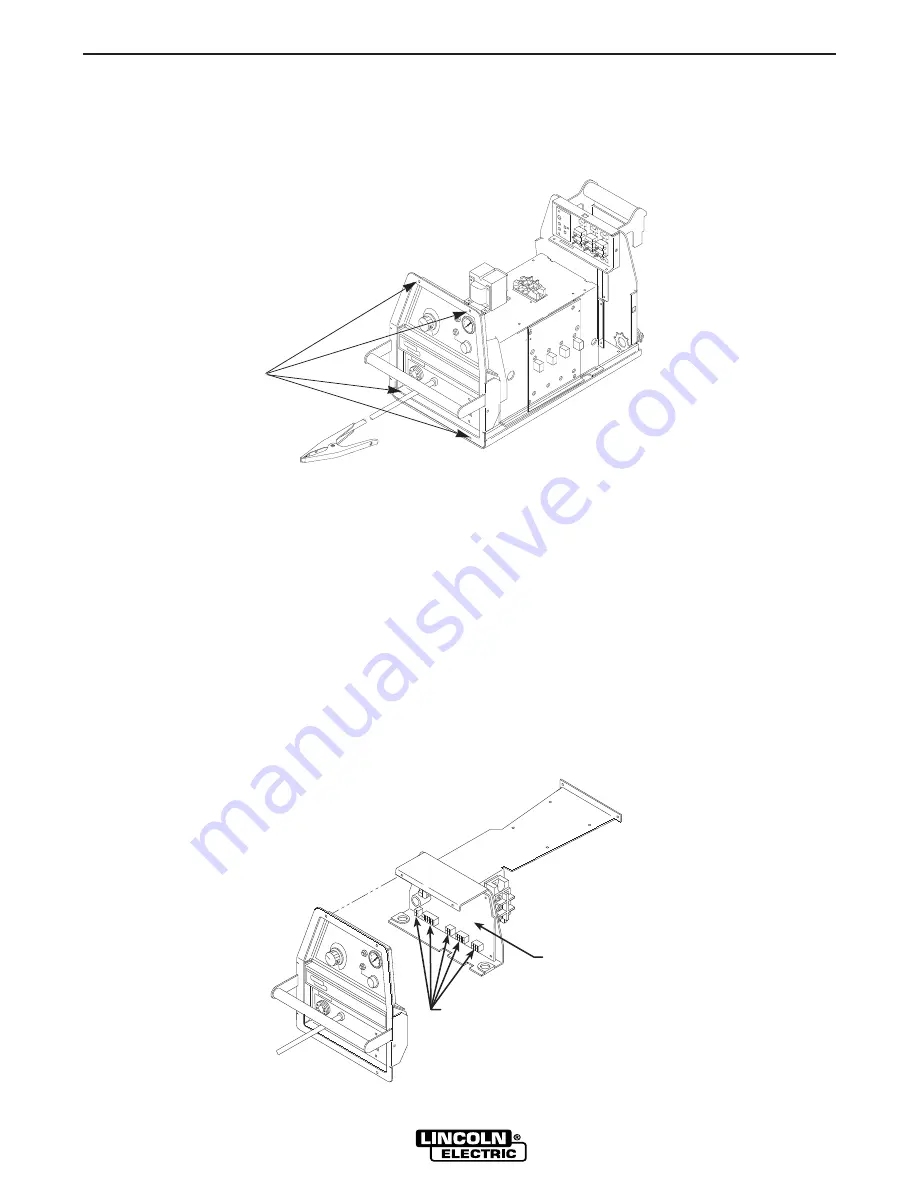
TROUBLESHOOTING & REPAIR
F-41
F-41
PRO-CUT 80
PROCEDURE
1. Remove input power to the PRO-CUT 80
machine.
2. Remove the wraparound cover and perform
the
Input Filter Discharge Procedure
detailed earlier in this section.
3. Using the 5/16” nut driver, remove the four
screws holding the front assembly to the top
and base of the machine. See Figure F.16.
4. Carefully slide (do not force) the front away
from the rest of the machine about one inch.
This will allow more “working” room to
remove the control board.
CONTROL BOARD REMOVAL AND REPLACEMENT
(continued)
CONTROL
BOARD
MOLEX PLUGS (5)
FIGURE F.16 - CASE FRONT SCREW REMOVAL
FIGURE F.17 - CONTROL BOARD MOLEX PLUG REMOVAL
4 Screws
Summary of Contents for PRO-CUT 80
Page 24: ...NOTES B 10 B 10 PRO CUT 80...
Page 40: ...NOTES E 10 E 10 PRO CUT 80...
Page 98: ...NOTES F 58 F 58 PRO CUT 80...