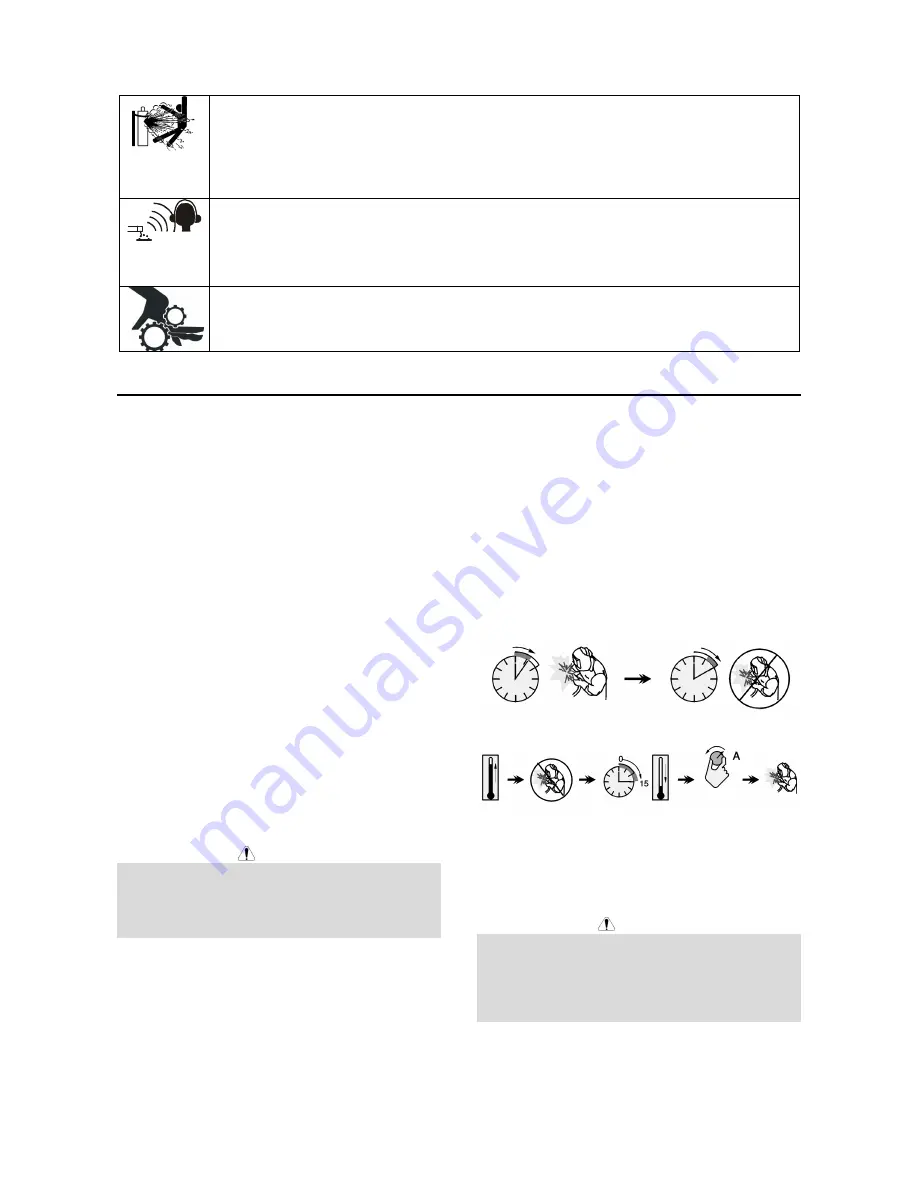
English
English
2
CYLINDER MAY EXPLODE IF DAMAGED: Use only compressed gas cylinders containing the
correct shielding gas for the process used and properly operating regulators designed for the gas and
pressure used. Always keep cylinders in an upright position securely chained to a fixed support. Do
not move or transport gas cylinders with the protection cap removed. Do not allow the electrode,
electrode holder, work clamp or any other electrically live part to touch a gas cylinder. Gas cylinders
must be located away from areas where they may be subjected to physical damage or the welding
process including sparks and heat sources.
NOISE APPEARES DURING WELDING CAN BE HARMFUL: Welding arc can cause noise with high
level of 85dB for 8-hour week day. Welders operating welding machines are obligated to wear the
proper ear protectors /appendix No. 2 for the Decree of the Secretary of Labor and Social Policy from
17.06 1998 – Dz.U. No. 79 pos. 513/. According to the Decree the Secretary of Health and Social
Welfare from 09.07.1996 /Dz.U. No. 68 pos. 194/, employers are obligated to carry examinations and
measurements of health harmful factors.
MOVING PARTS ARE DANGEROUS: There are moving mechanical parts in this machine, which
can cause serious injury. Keep your hands, body and clothing away from those parts during machine
starting, operating and servicing.
Installation and Operator Instructions
Read this entire section before installation or operation
of the machine.
Location and Environment
THE POWER WAVE
®
C300CE will operate in harsh
environments. Even so, it is important that simple
preventative measures are followed in order to assure
long life and reliable operation.
•
The machine must be located where there is free
circulation of clean air such that air movement in the
back, out the sides and bottom will not be restricted.
•
Dirt and dust that can be drawn into the machine
should be kept to a minimum. The use of air filters
on the air intake is not recommended because
normal air flow may be restricted. Failure to
observe these precautions can result in excessive
operating temperatures and nuisance shutdown.
•
Keep machine dry. Shelter from rain and snow. Do
not place on wet ground or in puddles.
•
Do not mount the POWER WAVE
®
C300 CE over
combustible surfaces. Where there is a combustible
surface directly under stationary or fixed electrical
equipment, that surface shall be covered with a
steel plate at least 1.6mm thick, which shall extend
not less than 150mm beyond the equipment on all
sides.
Lifting
WARNING
FALLING EQUIPMENT can cause injury.
Lift only with equipment of adequate lifting capacity.
•
Be sure machine is stable when lifting.
•
Do not operate machine while suspended when
lifting.
Both handles should be used when lifting POWER
WAVE
®
C300 CE. When using a crane or overhead
device a lifting strap should be connected to both
handles. Do not attempt to lift the POWER WAVE
®
C300 CE with accessories attached to it.
Stacking
The POWER WAVE
®
C300 CE cannot be stacked.
Tilting
Place the machine directly on a secure, level surface or
on a recommended undercarriage. The machine may
topple over if this procedure is not followed.
Duty Cycle and Overheating
The POWER WAVE
®
C300 CE is rated at 250A - 26.5V
@ 100% duty cycle. It is further rated to provide 300A –
29V @ 40% duty cycle.
The duty cycle is based on a ten-minute period. A 40%
duty cycle represents 6 minutes of welding and 4
minutes of idling in a 10-minute period.
Example: 40% Duty Cycle:
Welding for 4 minutes.
Break for 6 minutes.
Minutes
or decrease
Duty Cycle
Preparation for Work
Input and Ground Connections
WARNING
Only a qualified electrician should connect the input
leads to the POWER WAVE
®
C300 CE. Connections
should be made in accordance with all local and national
electrical codes and the connection diagram located on
the inside of the reconnect access door of the machine.
Failure to do so may result in bodily injury or death.
Machine Grounding
The frame of the welder must be grounded. A ground
terminal marked with a ground symbol is located next to
the input power connection block. See your local and