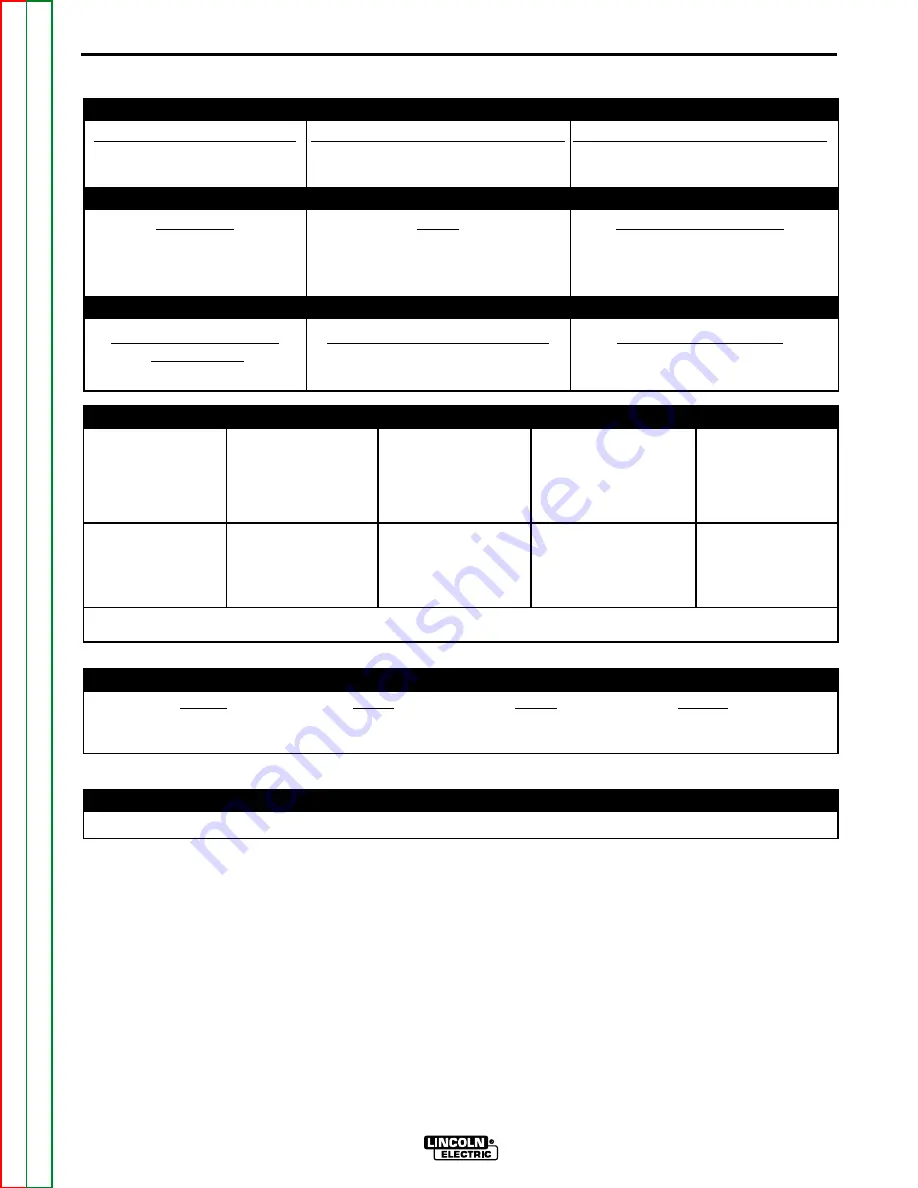
POWER MIG 255
Retur
n to Section TOC
Retur
n to Section TOC
Retur
n to Section TOC
Retur
n to Section TOC
Retur
n to Master TOC
Retur
n to Master TOC
Retur
n to Master TOC
Retur
n to Master TOC
A-2
INSTALLATION
A-2
75°C Copper Wire
75°C Copper Wire
in Conduit
in Conduit
Input Ampere
AWG (IEC) Sizes
AWG (IEC) Sizes
Input Voltage/
Fuse or Breaker
Rating On
(For lengths
(For lengths
Frequency (Hz)
Size (Super Lag)
Nameplate
up to 100 ft)
exceeding 100 ft)
208/60
60
50
8 (10 mm2)
6 (16 mm2)
230/60
60
46
10 (6 mm2)
8 (10 mm2)
460/60
30
24
14 (2.5 mm2)
12 (4 mm2)
575/60
25
19
14 (2.5 mm2)
12 (4 mm2)
NOTE: Use #10 AWG Grounding Wire
TECHNICAL SPECIFICATIONS – POWER MIG 255
INPUT – SINGLE PHASE ONLY
RATED OUTPUT
OUTPUT
RECOMMENDED INPUT WIRE AND FUSE SIZES
Height
Width
Depth
Weight
31.79 in.
18.88 in.
38.78 in.
220 Ibs
808 mm
480 mm
985 mm
100 kg
PHYSICAL DIMENSIONS
Wire Speed
50 – 700 IPM (1.27 – 17.8 m/minute)
WIRE SPEED RANGE
Standard Voltage/Frequency
Input Current @ 200 Amp Rated Output Input Current @ 250 Amp Rated Output
208/230/60 Hz
41/37 Amps
50/46
230/460/575/60 Hz
41/20/16 Amps
50/24/19
Duty Cycle
Amps
Volts at Rated Amperes
40%
250 Amps
26 Volts
60%
200 Amps
28 Volts
100%
145 Amps
26 Volts
Welding Current Range
Maximum Open Circuit Voltage
Welding Voltage Range
(Continuous)
30 – 300 Amps
40 Volts
10-28 Volts