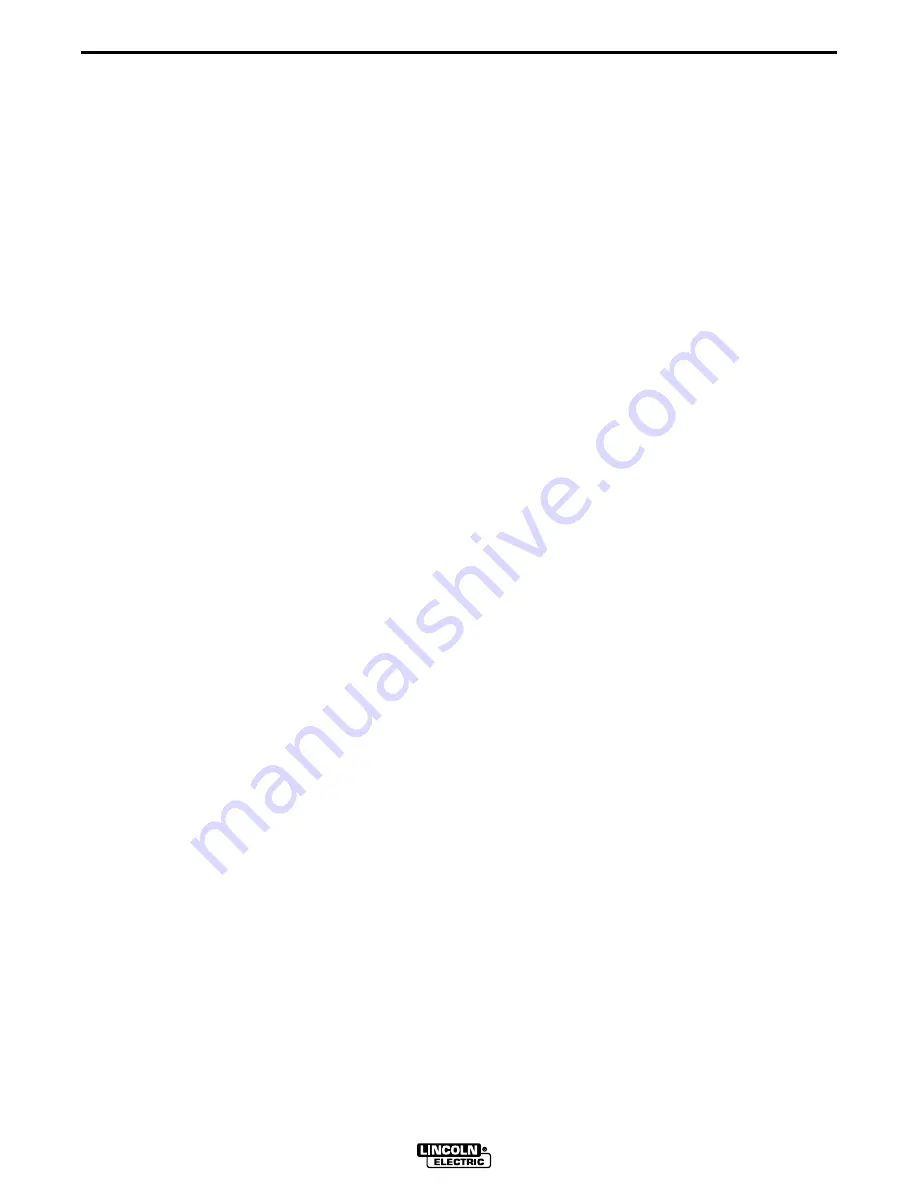
OPERATING INSTRUCTIONS
B-13
B-13
NA-3 AND NA-4
AC-1200 (or Discontinued AC-1000 or
AC-750)
a. Set the current with the “Current
Control” on the NA-4. For initial
test welds with the AC-1200, set
the control to “5”. Be sure to
choose the correct current range
stud on the AC-1200. The
discontinued AC-1000 or AC-750
output is indicated on the dial on
the front of the power source.
b. Set the voltage with the “Voltage
Control” on the NA-4. For initial
test welds, set the control to “6”.
The power source OCV is fixed.
2. Unless previously instructed, set the
“Inch Speed” for good arc striking as
follows:
a. When “hot” starting, set the “Inch
Speed” to one or two dial
numbers lower than the setting
on the “Voltage Control” on the
front panel. This provides an inch
speed slower than the
welding feed speed usually
recommended.
b. When “cold” starting, set the
“Inch Speed” at about “2” for a
slow inching speed to prevent
jamming the electrode against the
work before striking.
3. If using a motor-generator type power
source, set the “Voltage Range”
switch on the power source to “High.”
If using a motor-generator power
source with the discontinued solid
state remote field control installed,
the OCV is controlled by the “Open
Circuit Voltage” control on the inner
panel of the NA-3. Set the “OCV
Control” for good striking at about
3 to 8 volts higher than the welding
voltage. To read OCVs under 50 volts
on the NA-3 voltmeter, inch the
electrode up from the work and press
the “Start” button. Press the “Stop”
button before the electrode reaches
the work.
4. If installed, set the “Start Controls”
and “Crater Controls” on the inner
panel. For initial test welds, set both
“Time in Seconds” to “1” and the
“Current” and “Voltage” controls to the
same dial numbers (to produce about
the same output) as the “Current
Control” and “Voltage Control” on the
front panel.
5. The setting on the “Contactor and
Electrode Back Up Time Delay” on
the inner control panel is not
generally critical to submerged arc
welding. For initial test welds, set it
to “5”.
6. Straighten the first 6 in. (152.40 mm)
of the electrode and push it through
the wire straightener to the drive rolls.
Press the “Inch Down” button and
feed the electrode down through the
nozzle. Adjust the wire straightener
hand wheel. With contact nozzles
installed, except for the K231 Contact
Nozzle, adjust the hand wheel until
the electrode is straight as it comes
out of the nozzle. Do not
completely
straighten the wire when using the
K231 Contact Nozzle because the
nozzle relies on the small curvature
of the electrode for proper electrical
contact within the contact tip.
7. Set the travel speed as specified by
the procedures. With the wire speed
“Travel” switch set to “Hand Travel,”
the travel runs without welding,
permitting accurate measurements of
travel speed. When using a Lincoln
Electric travel carriage, adjust the
speed with the rheostat and the
direction with the toggle switch on the
carriage control panel.
8. Mount and properly connect the work
lead to the work or a suitable piece of
scrap. Clip the end of the electrode to
a sharp point.
Summary of Contents for NA-3S
Page 6: ...NOTES v v NA 3 AND NA 4 ...
Page 47: ...NOTES B 18 B 18 NA 3 AND NA 4 ...
Page 53: ...NOTES C 6 C 6 NA 3 AND NA 4 ...
Page 91: ...NOTES F 26 F 26 NA 3 AND NA 4 ...
Page 101: ...NOTES NA 3 AND NA 4 ...