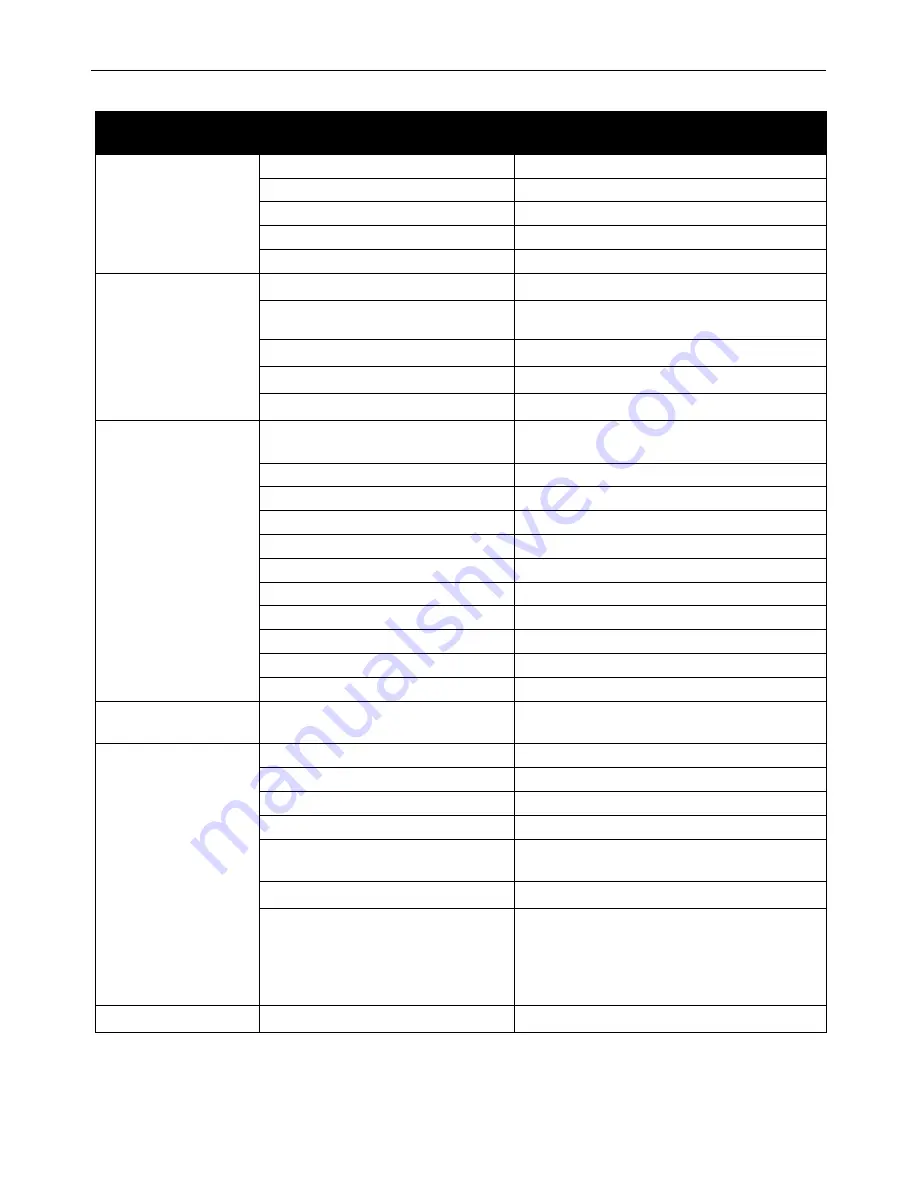
11
TROUBLESHOOTING
MAGNUM PRO 250 LX & LX GT SPOOL GUN
Observe all Safety Guidelines detailed throughout this manual
If for any reason you do not understand the test procedures or are unable to perform the tests/repairs safely, contact your
Lincoln Authorized Service Facility for technical troubleshooting assistance before you proceed.
WWW.LINCOLNELECTRIC.COM/LOCATOR
PROBLEM
(SYMPTOMS)
POSSIBLE AREAS OF
MISADJUSTMENT(S)
RECOMMENDED COURSE OF ACTION
No arc, wire feed, or gas
flow.
1. Cable connections loose.
1. Check all power connections.
2. Trigger switch loose or defective.
2. Fix switch or replace.
3. Welder not turned on.
3. Turn on welder power.
4. Welder not plugged in.
4. Plug in.
5. Cable or adapter cable damaged.
5. Inspect and replace
No arc, weak arc.
1. Poor ground connection to work.
1. Check ground connection.
2. Power cable connection loose.
2. Check connections; if defective, replace cable or
connectors.
3. Voltage set too low.
3. Adjust to proper voltage
4. Tip too large for wire size.
4. Change tip size.
5. Wire feed speed too slow.
5. Increase wire feed speed.
No wire feed.
1. Feeding small diameter wire with large
groove on drive roller.
1. Change position of wire drive roller.
2. Wire drive release open.
2. Close wire drive release.
3. Wire welded to tip.
3. Peel wire off tip or use new tip.
4. Wire spool empty.
4. Insert new spool.
5. Tip too small for wire.
5. Insert correct tip.
6. Kink or bend in wire.
6. Pull wire through tip or start new wire end.
7. Spool cover binding.
7. Rotate spool cover slot to proper position.
8. Control cable loose.
8. Check all connections.
9. Drive roller worn.
9. Replace.
10. Pressure roller stuck.
10. Replace or lubricate.
11. Roller spring loose or broken.
11. Replace.
Wire feed too fast or too
slow.
1. Wrong wire speed set for work.
1. Adjust wire feed speed.
Low or no gas flow.
Oxidation of work.
1. Gas flow not set right.
1. Set proper flow rate.
2. Cylinder out of gas.
2. Get new cylinder of gas.
3. Cylinder valve closed.
3. Open cylinder valve.
4. Leak in gas line.
4. Inspect and replace.
5. Leak in gun.
5. Check for missing gun tubes and/or missing gun
body cover.
6.Gas diffuser clogged
6. Blow out gas diffuser openings.
7. Clogged internal valve (only for K3569-2)
7. Remove neck and check if gas is flowing from
mechanical valve by pressing the trigger. If no gas
flow is detected, adjust first the trigger set screw
as shown in the manual page 13- replace
mechanical valve if no gas is detected.
Oxidized work, arc unstable. 1. Wrong welding polarity.
1. Check polarity.