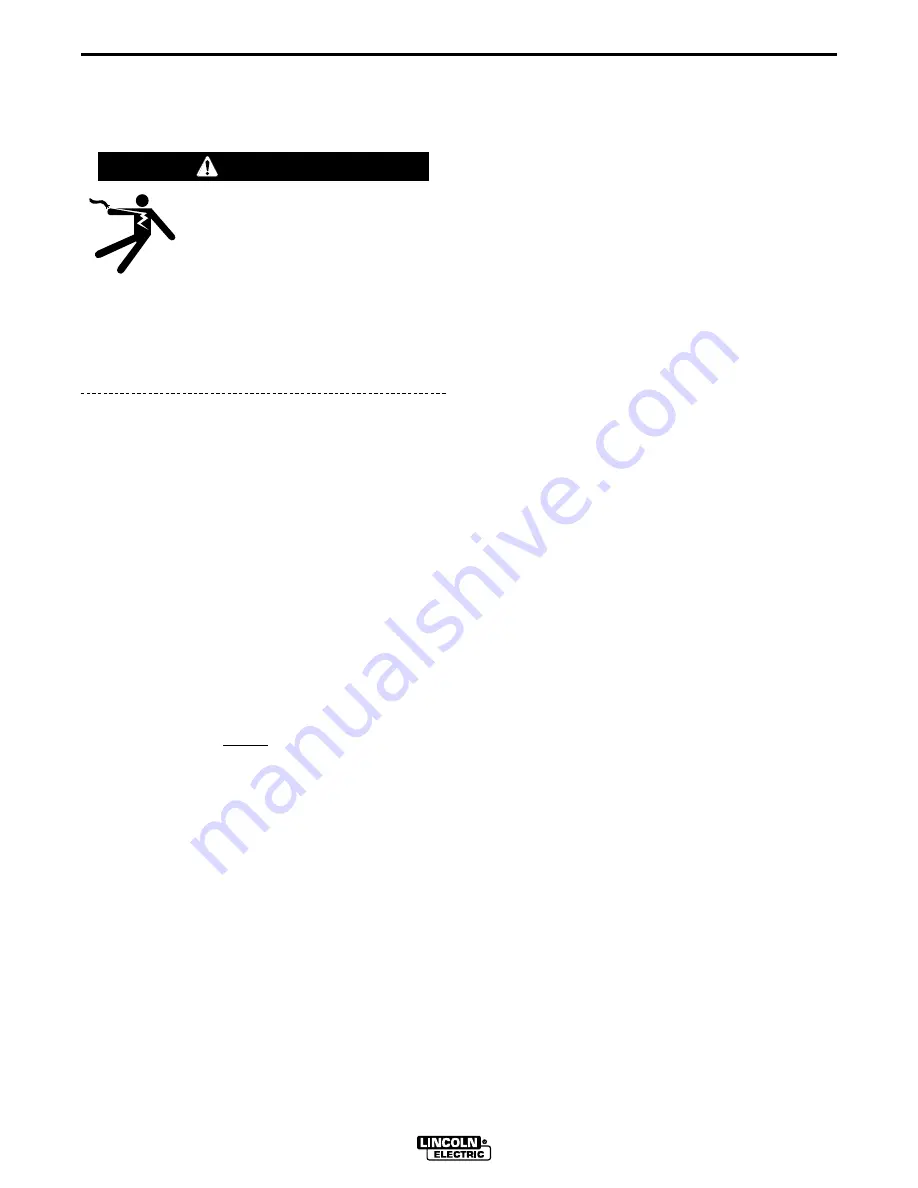
A-2
INSTALLATION
INVERTEC V200-T
A-2
MACHINE GROUNDING AND HIGH FRE-
QUENCY INTERFERENCE PROTECTION
The welder must be grounded. See your local and national
electrical codes for proper grounding methods.
The high frequency generator, being similar to a radio
transmitter, can be blamed for radio, TV and electron-
ic equipment interference problems. These problems
may be the result of radiated interference. Proper
grounding methods can reduce or eliminate radiated
interference.
Radiated interference can develop in the following
four ways:
1. Direct interference radiated from the welder.
2. Direct interference radiated from the welding leads.
3. Direct interference radiated from feedback into the
power lines.
4. Interference from re-radiation of “pickup” by
ungrounded metallic objects.
Keeping these contributing factors in mind, installing
equipment per the following instructions should mini-
mize problems.
1. Keep the welder power supply lines as short as
possible and enclose as much of them as possible
in rigid metallic conduit or equivalent shielding for a
distance of 50 feet (15.2m). There should be good
electrical contact between this conduit and the
welder case ground. Both ends of the conduit
should be connected to a driven ground and the
entire length should be continuous.
2. Keep the work and electrode leads as short as
possible and as close together as possible.
Lengths should not exceed 25 ft (7.6m). Tape the
leads together when practical.
3. Be sure the torch and work cable rubber coverings
are free of cuts and cracks that allow high frequen-
cy leakage.
4. Keep the torch in good repair and all connections
tight to reduce high frequency leakage.
5. The work piece must be connected to an earth
ground close to the work clamp, using one of the
following methods:
Read entire installation section before starting
installation.
Safety Precautions
SELECT SUITABLE LOCATION
The Invertec will operate in harsh environments. Even
so, it is important that simple preventative measures
are followed in order to assure long life and reliable
operation.
• The machine must be located where there is free cir-
culation of clean air such that air movement in the
back and out the sides will not be restricted.
• Dirt and dust that can be drawn into the machine
should be kept to a minimum. Failure to observe
these precautions can result in excessive operating
temperatures and nuisance shutdown.
STACKING
The Invertec V200-T cannot be stacked.
LIFTING AND MOVING
The Invertec V200-T
has a lift handle on the top of the
case and also comes with a lift-carrying strap for con-
vience.
TILTING
Place the machine directly on a secure, level surface.
The machine may topple over if this procedure is not
followed.
ENVIRONMENTAL RATING
• The machine has a protection rating of IP23. Keep
the machine dry when possible. Do not place it on
wet ground or in puddles.
ELECTRIC SHOCK can kill.
• Only qualified personnel should
perform this installation.
• Turn the input power OFF at the
disconnect switch or fuse box
before working on this
equipment.
• Do not touch electrically hot
parts.
• Always connect the V200-T to a power sup-
ply grounded per the National Electrical
Code and any local codes.
WARNING