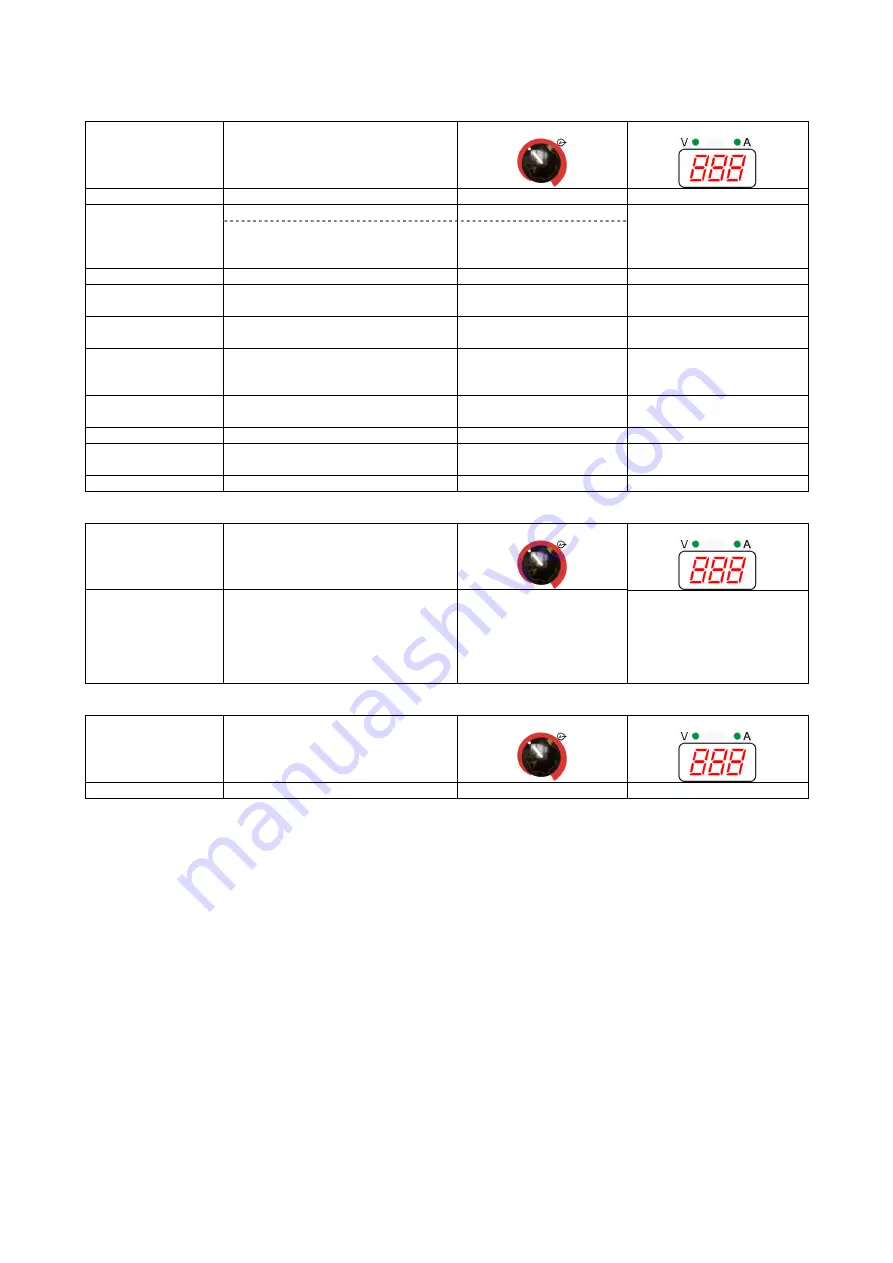
English 18
English
List of parameters and Factory stored programs
List of parameters and Factory Configuration program:
Parameter Factory
Configuration
Selectable Value Range
Displayed value
Preflow
0.3s
0 - 5s (step 0.1s)
Current selected value (s)
Start Current
Lift TIG 2-step: 22A
Not adjustable
Current selected value
(% of set current)
Lift TIG 4-step: 30%
HF TIG 2-step: 30%
HF TIG 4-step: 30%
5 - 200%
Upslope
0.1s
0 - 5s (step 0.1s)
Current selected value (s)
Set Current
1
50A
5 - 160A (Stick)
5 - 160A (TIG))
Current selected value (A)
Duty Cycle
50%
10 - 90% (step 5%)
(f>300Hz Duty=50%)
Current selected value (%)
Frequency (f)
50Hz
0.1 - 10Hz (step 0.1Hz)
10 - 300Hz (step 1Hz)
300 - 500Hz (step 10Hz)
Current selected value (Hz)
Background
30%
10 - 90% (step 1%)
Current selected value
(% of set current)
Downslope
0s
0 - 20s (step 0.1s)
Current selected value (s)
Crater
30%
5 - 100% (step 1%)
Current selected value
(% of set current)
Postflow
5s
0 - 30s (step 1s)
Current selected value (s)
TIG SPOT WELDING (to previously enable with option 10 in Setup menu)
Parameter Features
Selectable Value Range
Displayed value
Spot Current
Trigger = 2-step
No restart function enabled
Preflow time = 0s
Upslope time = 0s
Downslope time = 0s
Postflow time = 0s
5 - 160A
Current selected value (A)
TIG SPOT FIXED TIME (to previously enable with option 11 in Setup menu)
Parameter Features
Selectable Value Range
Displayed value
Spot Time
0 (manual trigger)
0 - 5s (step 0.1s)
Welding time (s)
1
It's possible change the maximum and mimimum selectable current with “Option 51” and "Option 52" in the Setup
Menu. If [Off] the set current are the “factory default”, otherwise it is possible set another current.