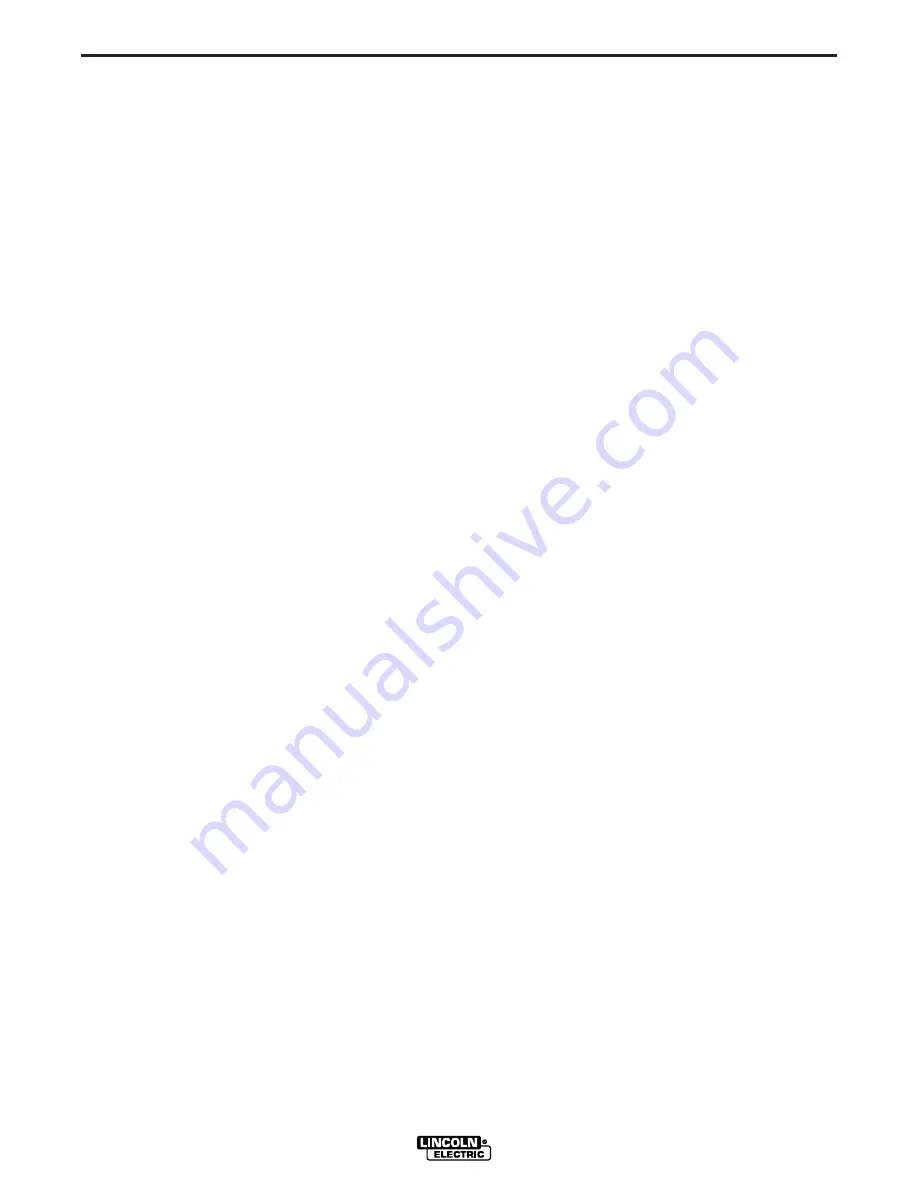
D-3
MAINTENANCE
D-3
Disinfect the cooling system:
• Prepare the disinfectant: Make a quantity of only is
needed to avoid an excess.
• Bulk preparation (for coolers serviced in quantity):
2.325 gals. (8.775 liters) of pure, fresh water per
cooler 1.625 ml of additive per cooler
• Example: for 100 coolers, add 162.5 ml to 232.5
gals. of pure fresh water Pour 2.0 gals. (7.55 liters)
of disinfectant into the empty reservoir
• Recap the reservoir, tape over the air vent in the
cap, roll disinfectant around the inside the reservoir
to thoroughly coat all of its surfaces.
• Remove the tape from the reservoir cap. Prime the
cooling system and circulate disinfectant through it
for 10 to 15 minutes.
• Drain disinfectant from the cooling system. Do not
reuse this solution.
• Add new, fresh coolant to the cooling system. Add
0.325 gals. (1.225 liters) of fresh disinfectant to the
system by pouring it into the reservoir, then reduce
the concentration to the nominal 30 ppm:
• Add the balance 1.675 gals. (6.325 liters) of fresh,
pure water to the reservoir to create the treated
coolant concentration
• Prime the cooling system
• Check coolant level. Add more fresh, pure water if
required, without adding more than 0.125 gal. (0.475
liters) of pure water to prevent diluting the coolant
additive.
Additive:
The recommended additive can be purchased at local
pool supply stores. An example is "Maintain Pool Pro
30% Non-Foam Algaecide".
PUMP INLET FILTER
Poor cooler performance can usually be traced to a
partially or completely blocked pump inlet filter. This is
a user-serviceable item and can be cleaned and
reused, or replaced. Continued pump operation with a
blocked filter can cause:
• Voiding of cooler service warranty
• Cavitation damage to the pump heads inlet areas
• Welding accessory damage from overheating due to
insufficient coolant flow rate.
A new or properly cleaned pump inlet filter should
restore the cooler’s performance.
For additional service and periodic maintenance
details and for recommended coolants, follow the rec-
ommendations listed in the following paragraphs.
PROCEDURE
Preparation:
• Always switch off the Precision TIG machine power
• Always disconnect the Under-Cooler cart from the
Tig machine receptacle.
• Always allow the coolant in the system to cool
enough to avoid burn injuries.
• Avoid contact with contaminated coolant. Wear
waterproof gloves and protective eyewear.
• Do not remove the pump relief valves 3/4 in. acorn
hex nut or attempt to adjust the relief valve setting.
Inspect condition of coolant:
a. If coolant is contaminated or old:
• Drain the system of coolant and dispose of it in an
environmentally responsible manner.
• Flush system of old coolant.
• Fill with fresh tap or distilled water, run for ten min-
utes, and drain.
• Proceed to adding coolant.
b. If coolant is clean and fresh:
• If clean, dedicated coolant handling equipment,
including a clean siphon pump and a clean holding
tank are available then proceed to servicing the
pump inlet strainer.
Removing Coolant:
a. Drain coolant from the reservoir using clean
siphoning equipment.
b. Coolant level should be drained below the filter’s
pressure fitting:
• This prevents coolant from streaming out of unit
when filter nut is removed.
UNDER-COOLER CART
Summary of Contents for IM723-A
Page 24: ...NOTES UNDER COOLER CART...
Page 25: ...NOTES UNDER COOLER CART...
Page 26: ...NOTES UNDER COOLER CART...