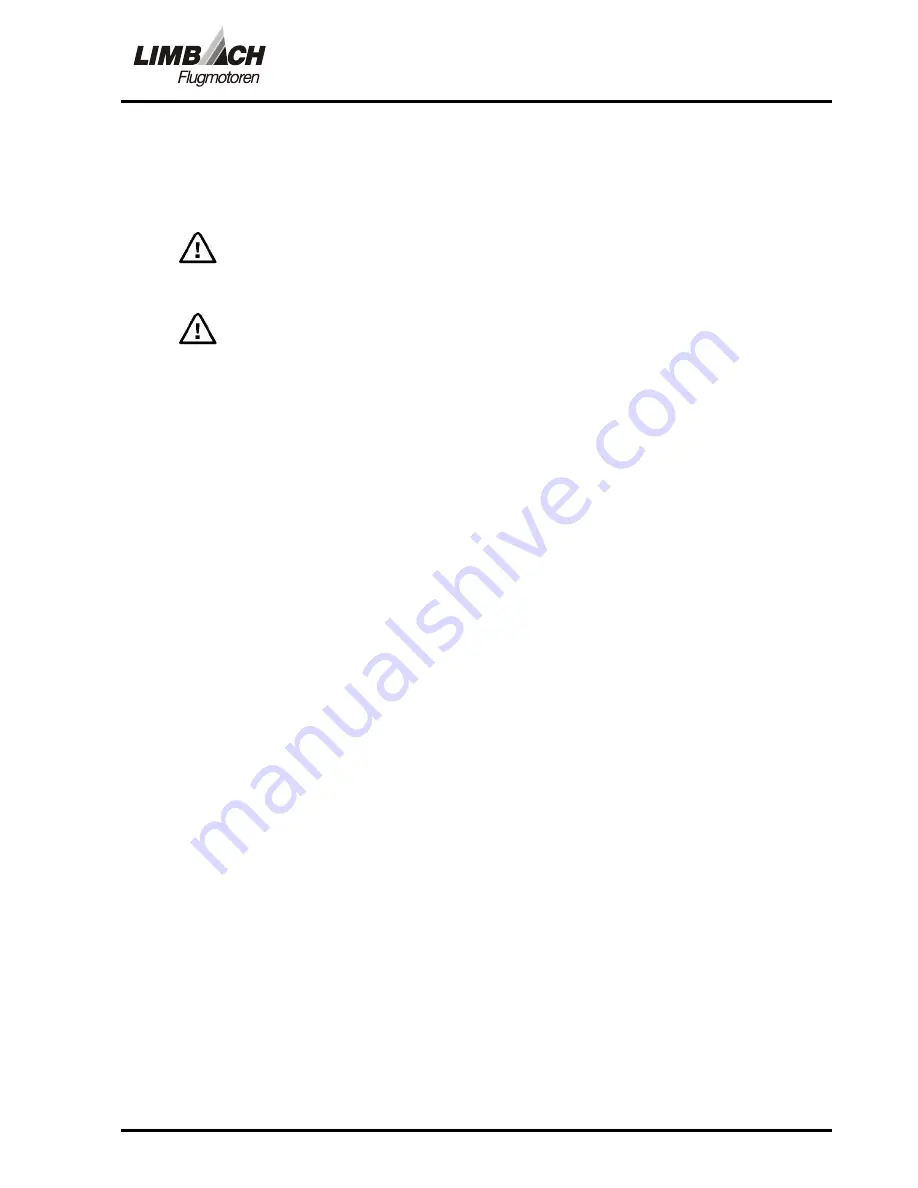
Page: 28/48
Operating Manual L 2000
Edition: 01.03.2016
201
.2
5
3
.9
0
5
.0
0
0
8
Maintenence Instructions
This chapter describes the performance of maintenance work. In addition, the preservation of
engines as well as winter and tropical operation is covered.
Repair activities during engine maintenance may only be performed by authorized persons.
Caution:
Disconnect spark plug connectors before performing any work on the engine.
Unscrew connectors on shielded spark plugs.
Caution:
When starting the engine, the propeller area must be clear. Secure the aircraft from
rolling. No persons may be present in the propeller area.
Note:
Vacuum pump equipped aircraft engines must never be turned opposite to the engine rotation
because the vacuum pump might be damaged.
Check with your airworthiness inspector if inspection is mandatory before starting work.
It is recommended to mark the position of parts to be removed before commencing disassembly
work in order to facilitate assembly later on. This is only applicable to parts which might
be installed in different positions. During assembly, pay attention to markings provided by the
manufacturer (e.g. magneto timing markings).
The ignition harness is marked by the manufacturer. The coupling nuts are bearing letters and
numbers. The letter "T" refers to upper, the letter "B" to lower spark plugs (dual ignition only).
The figure behind the letter is representing the cylinder number.
In addition, the distributor blocks of engines with dual ignition are marked with the letter
"L"= left magneto or "R" = right magneto (view from back to the engine).
8.1
Oil Change
Warm up engine.
Drain oil.
Remove five cap nuts from the oil screen cover and unfasten the sixth. Lift oil screen
cover from the case by means of a screwdriver and drain oil. The engine must be
horizontally orientated.
Clean oil screen.
Wash oil screen in gasoline used for cleaning purposes and clean it off by
using compressed air.
Mount oil screen.
Replace sealings, gaskets and self-locking cap nuts!
Refill engine oil.
The oil charge is 2.5 l. Check oil level by means of the oil-measuring stick. The MAX marking
must not be exceeded. The engine must be horizontally orientated. This is especially important
for so called “taildragger” Aircraft.
See section 10.1 for oil specifications.