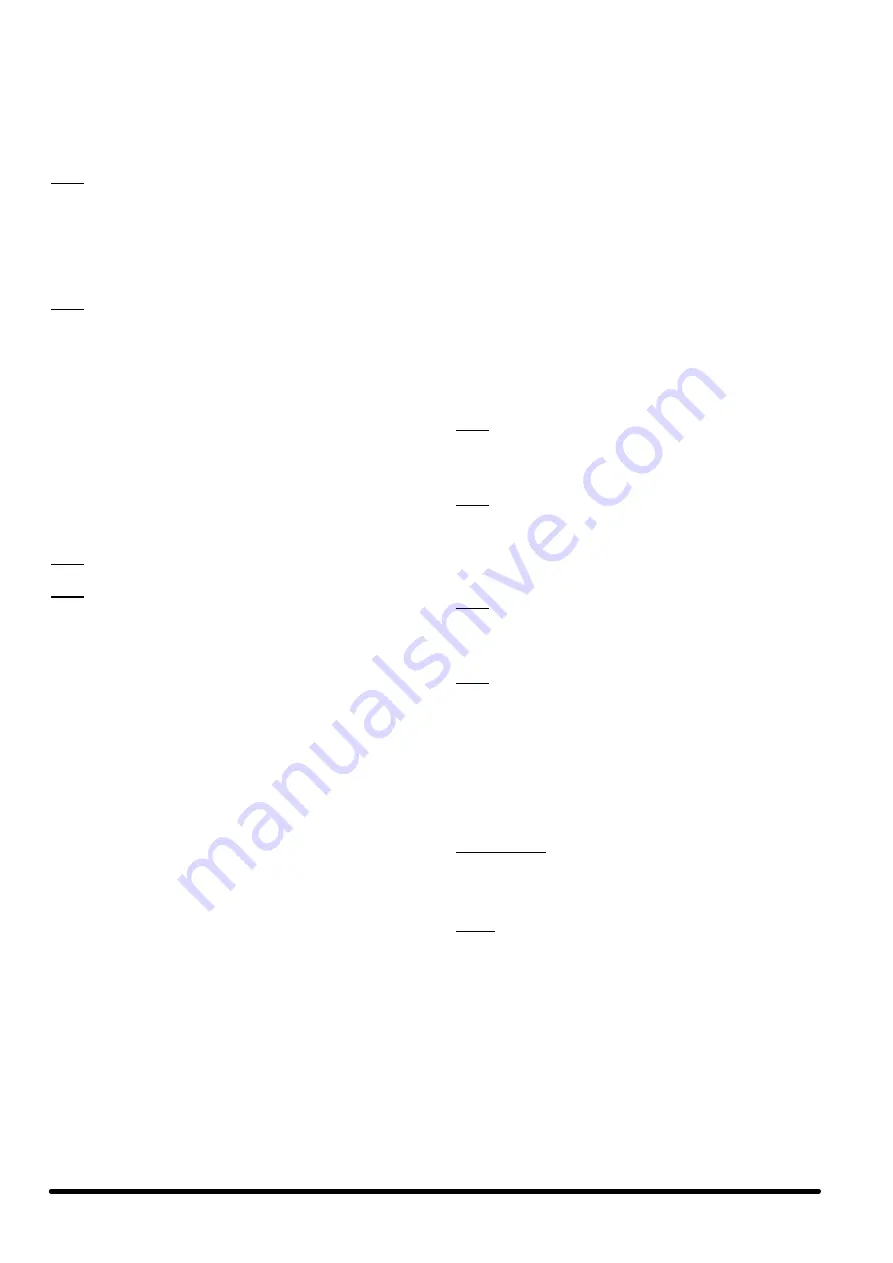
2
2.2 --- Sound pressure levels
The Tab. 4 shows the noise data for the units in standard config-
uration (without pumps), operating continuously and measured
according to the ISO 3744 norm, in free field conditions.
The highestnoise levelsare detected on the condenser coilside.
Note:
Avoid positioning in areas with possible reverberation of the
sound waves, which can adversely effect the noise levels.
2.3 --- Transport
S
Handle the unit by lifting it with a crane from above;
S
The lifting holes are positioned in the frame’s base (when lift-
ing, use spreader bars to protect the sides, see Fig. 2).
Note:
Place the lifting tubes in the holes in the base indicated by ”LIFT
HERE”. Lock the ends of the tubes with the locking pins and
splits pins as shown in Fig. 2.
The capacity of the lifting gear must be adequate to lift the load
in question. Check the weight of the units, the capacity of the lift-
ing gear and ropes and the condition and suitability of the afore-
mentioned equipment.
2.4 --- Foundations
S
The unit must be placed on a level surface which will support
its weight.
S
If necessary, position the unit on suitable anti---vibration sup-
ports that can be supplied as an option (in rubber or spring---
type). Refer to the manual ”Installation of the spring anti---
vibration supports” for their correct positioning.
S
When positioned, level the unit.
Note:
For weight distribution see Fig. 3.
Note:
The weights and their distribution refer to standard units without
options; if the pump assembly, or other options are installed on
the machine, add the weights of the installed accessories to
those of the standard units (see Tab. 8).
2.5 --- Service area
S
In order to allow free air flow and maintenance of the unit, a
minimum area must be left free of obstructions around the
unit (see Fig. 1).
S
The hot air expelled by the fans mustbe allowed to rise unim-
peded by obstacles for a minimum height of 2.5 m.
S
Avoid recirculation of hot air between the suction and dis-
charge, otherwise the unit performance may be impaired or
the standard operation can be interrupted.
3 --- Installation
3.1 --- Hydraulic connections
3.1.1 -- Hydraulic circuit construction (Fig. a)
The piping must be connected to the chiller. Construct a chilled
water circuit as described below, see Fig. a:
1) Place shut---off valves within the circuit to allow servicing;
2) Install a pump system suitable for the flow rate required at
a pressure head equal to the sum of all the pressure drops
(see project data).
Matrix S chillers can be equipped, upon request, with
pumps having performance as indicated in Tab. 8;
3) Install manometers at the chiller inlet/outlet;
4) Install thermometers at the chiller inlet/outlet;
5) Connect the pipes to the chiller by flexible joints to avoid
transmitting vibrations and to balance the thermal expan-
sion; proceed in the same way even if the pump set is out-
side the chiller;
6) It is useful to include a water pressure switch to give an early
warning of low water pressure;
7) Place a mesh filter at the inlets of the pump and water chiller
(Can be supplied as an optional accessory ---Not fitted);
8) Install, at the highest points in the circuit, apparatus which
allows the bleeding of air and possibly the filling of glycol;
9) Place a drain valve at the lowest point in the circuit and im-
mediately at the outlet of the water chiller;
10) Install a water filling set including the following:
a) filling water meter;
b) manometer;
c) non---return valve;
d) air separator;
e) removable supply tube,
which must be disconnected
after each charge/top---up;
11) For maximum protection ensure that all tubing exposed to
low outdoor temperatures is fitted with anti---freeze heaters
and insulated using closed cell synthetic rubber (elasto-
mer);
12) The circuit must include an expansion vessel (with safety
valve) of suitable capacity;
13) Connect the lines avoiding stresses on the machine inner
parts.
Note:
If the water chiller is complete with an expansion vessel (sup-
plied as an option), check if the capacity is enough, and install
a second vessel in the circuit, if required (see par. 8.4).
Follow the indications in Fig. c for the correct sizing.
Note:
The whole circuit must contain a water volume suitable for the
capacity of the installed chiller. Check if the inertial capacity giv-
en by the sum of the hydraulic volume inside the machine (in-
cluding the volume of the optional interna tank, if fitted) and the
system volume issufficient, or possibly installa tank in the circuit.
Follow the indications in Fig. b for the correct sizing.
Note:
The hydraulic circuit must ensure a constant water supply to the
evaporator in every operating condition. Otherwise, the com-
pressors may be damaged by repeated returnsof liquid refriger-
ant on their suction.
Note:
The water flow switch is a compulsory safety component that
must be installed and correctly wired to the Matrix S chillers,
otherwise the guarantee will be invalidated.
It is installed, as standard, on units with the optional on---board
pump set, and is available as a option for units without pumps
on board: in the latter case the flow switch, if not installed on the
machine, can be installed on the hydraulic circuit by the installer,
but it is compulsory that it is wired to the electric panel terminal
board, as indicated on the wiring diagram.
3.1.2 -- Addition of water and ethylene glycol
Very important:
Add water and ethylene glycol to the circuit with a % depending
on the minimum temperature of the outside air expected at the
installation site. Do not exceed the nominal operating pressure
of the circuit’s components.
Notes:
S
To avoid stratification run the circulation pump for at least 30
minutes after adding any glycol.
S
After adding water to the hydraulic circuit
always discon-
nect the water supply coming from the sanitary supply;
this avoids the danger of glycol entering the sanitary water
system.
S
After any topping---up of the water check the concentration
and add glycol if necessary.
3.1.3 -- Water--glycol mixture
Water---glycol mixtures are used as the thermal carrier fluid in
very cold climatesor with temperatures below zero degreescen-
tigrade. Determine the ethylene glycol % which must be added
to the water, with the assistance of Tab. a.