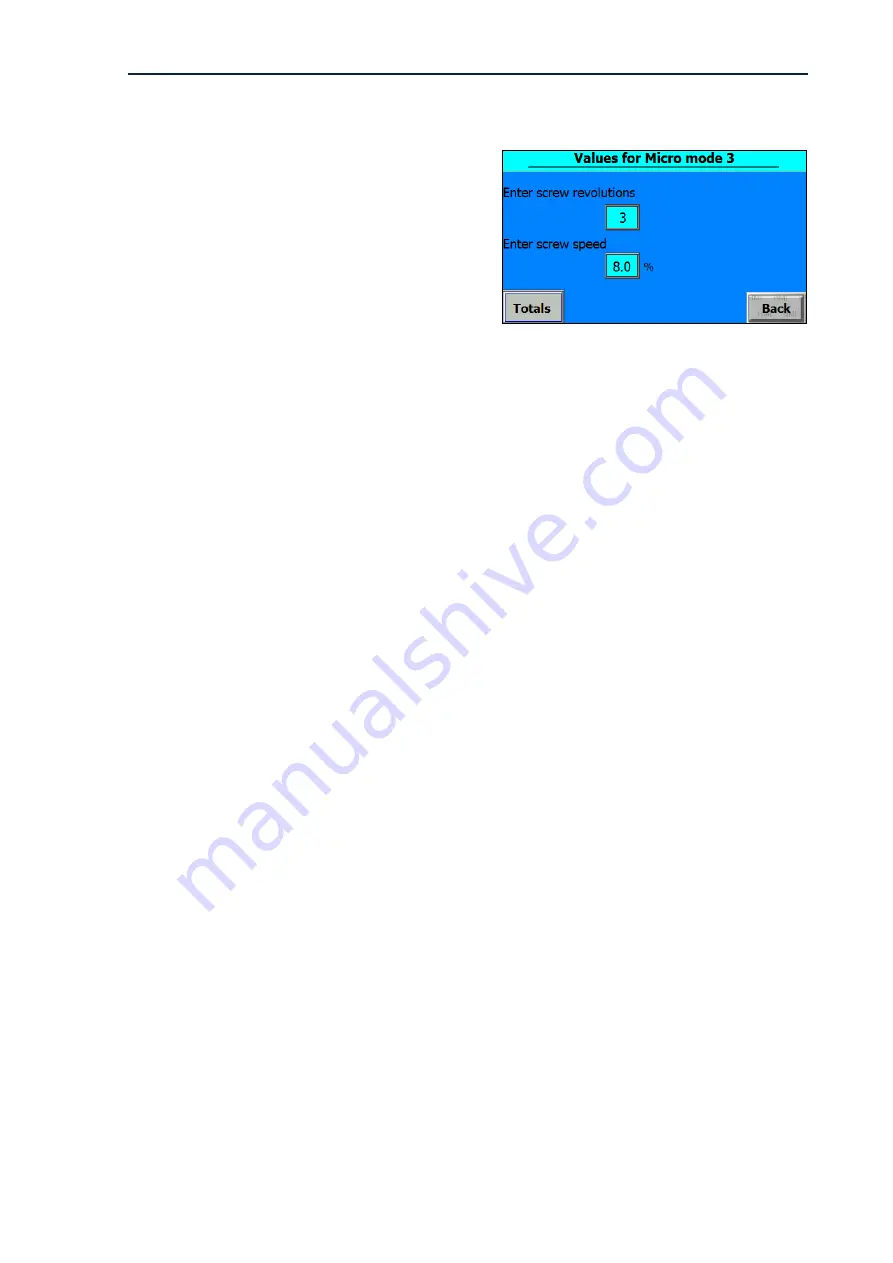
ColorSave 1000ST-INJ user manual
21
4.2.4.2 Changing Screw Revolutions And Speed In Micro Mode "3"
Press the Enter screw revolutions value to
activate new revolutions value
Press the Enter screw speed value to activate
new speed value
Press Totals button to enter Totals screen
(see section 4.4 Accumulated Data Display)
Press Back button to return to Main Screen