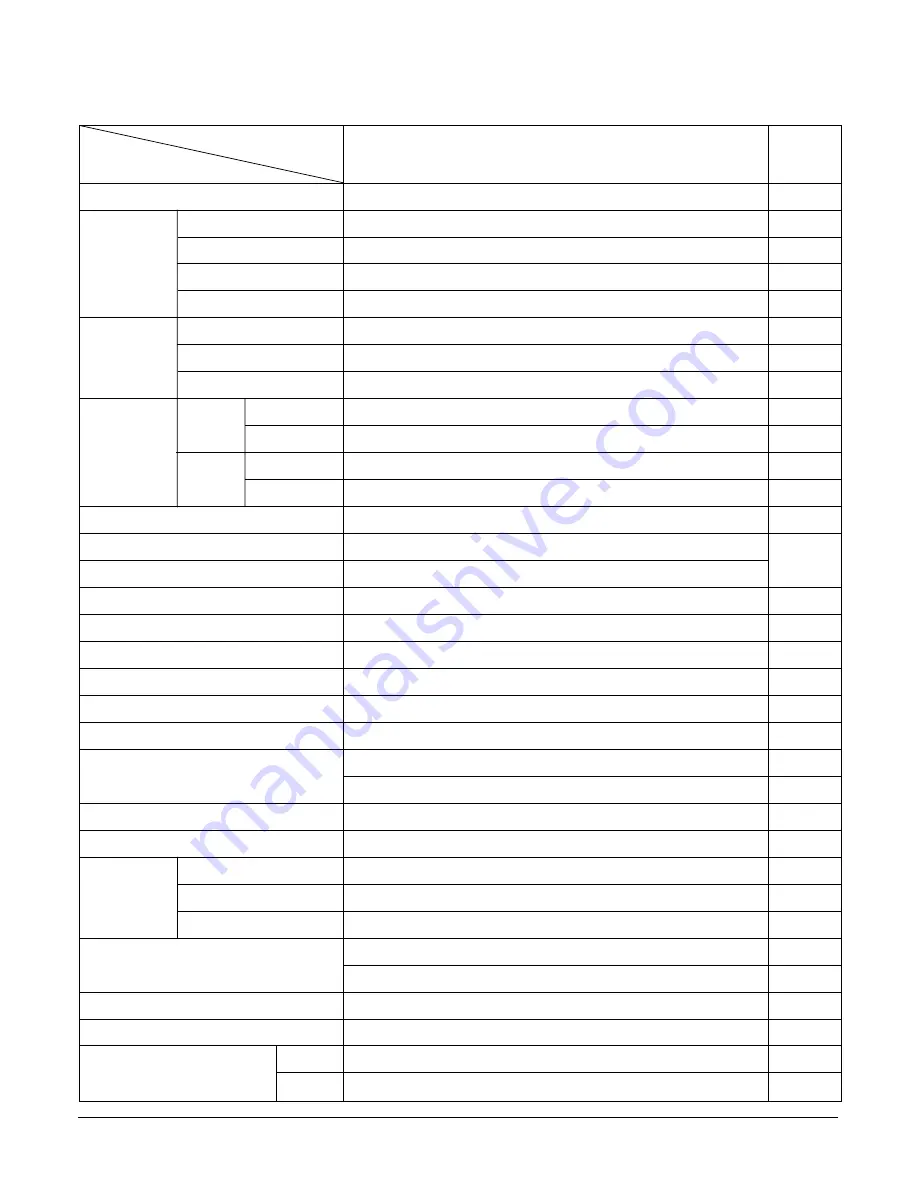
- 4 -
Copyright ©2008 LG Electronics. Inc. All right reserved.
Only for training and service purposes
LGE Internal Use Only
1.3.2 FOR R1801H
R1801H
REMARK
POWER SUPPLY
CAPACITY
(Btu/h)
INPUT
(W)
RUNNING CURRENT (A)
E.E.R.
(Btu/W.h)
CAPACITY
(Btu/h)
INPUT
(W)
RUNNING CURRENT (A)
INDOOR (°C)
OUTDOOR (°C)
INDOOR (°C)
OUTDOOR (°C)
REFRIGERANT (R-22) CHARGE(g)
EVAPORATOR
CONDENSER
FAN, INDOOR
FAN, OUTDOOR
FAN SPEEDS (FAN/COOLING/HEATING)
FAN MOTOR
OPERATION CONTROL
ROOM TEMP. CONTROL
CONSTRUCTION
ELECTRIC HEATER
COMPRESSOR
FAN MOTOR
ELECTRIC HEATER
DRAIN SYSTEM
NET WEIGHT
(lbs/kg)
OUTSIDE DIMENSION
(inch)
(W x H x D)
(mm)
1Ø, 208/ 230V, 60Hz
17,500/ 18,000
1,940/ 2,000
9.6/ 9.0
9.0
9,800/ 12,000
3,100/ 3,670
15.0/ 16.0
26.7 (DB) 19.4 (WB)
35 (DB) 23.9 (WB)
21.1 (DB) 15.6 (WB)
8.3 (DB) 6.1 (WB)
740 (26.1 OZ)
3 ROW 15 STACKS
2 ROW 19 STACKS, L-BENDED TYPE
BLOWER
PROPELLER TYPE FAN WITH SLINGER-RING
1/ 2/ 2
6 POLES
ROTARY SWITCH
THERMOSTAT
VERTICAL LOUVER (RIGHT & LEFT)
HORIZONTAL LOUVER (UP & DOWN)
SLIDE IN-OUT CHASSIS
3.5 KW, 230V
INTERNAL OVERLOAD PROTECTOR
INTERANL THERMAL PROTECTOR
FUSE LINK, BIMETAL THERMOSTAT
1.6m (3 WIRE WITH GROUDING)
ATTACHMENT PLUG (CORD-CONNECTED TYPE)
DRAIN PIPE OR SPLASHED BY FAN SLINGER
123/ 56
26 x 16
27
/
32
x 26
9
/
16
660 x 428 x 675
MODELS
ITEMS
OPERATING
TEMPERA-
TURE
AIR DIRECTION CONTROL
POWER CORD
PROTECTOR
HEATING
COOLING
COOLING
HEATING
LOUVERED-
FIN TYPE
Summary of Contents for WR-1820
Page 30: ...P NO 3828AR3735R MARCH 2008 ...