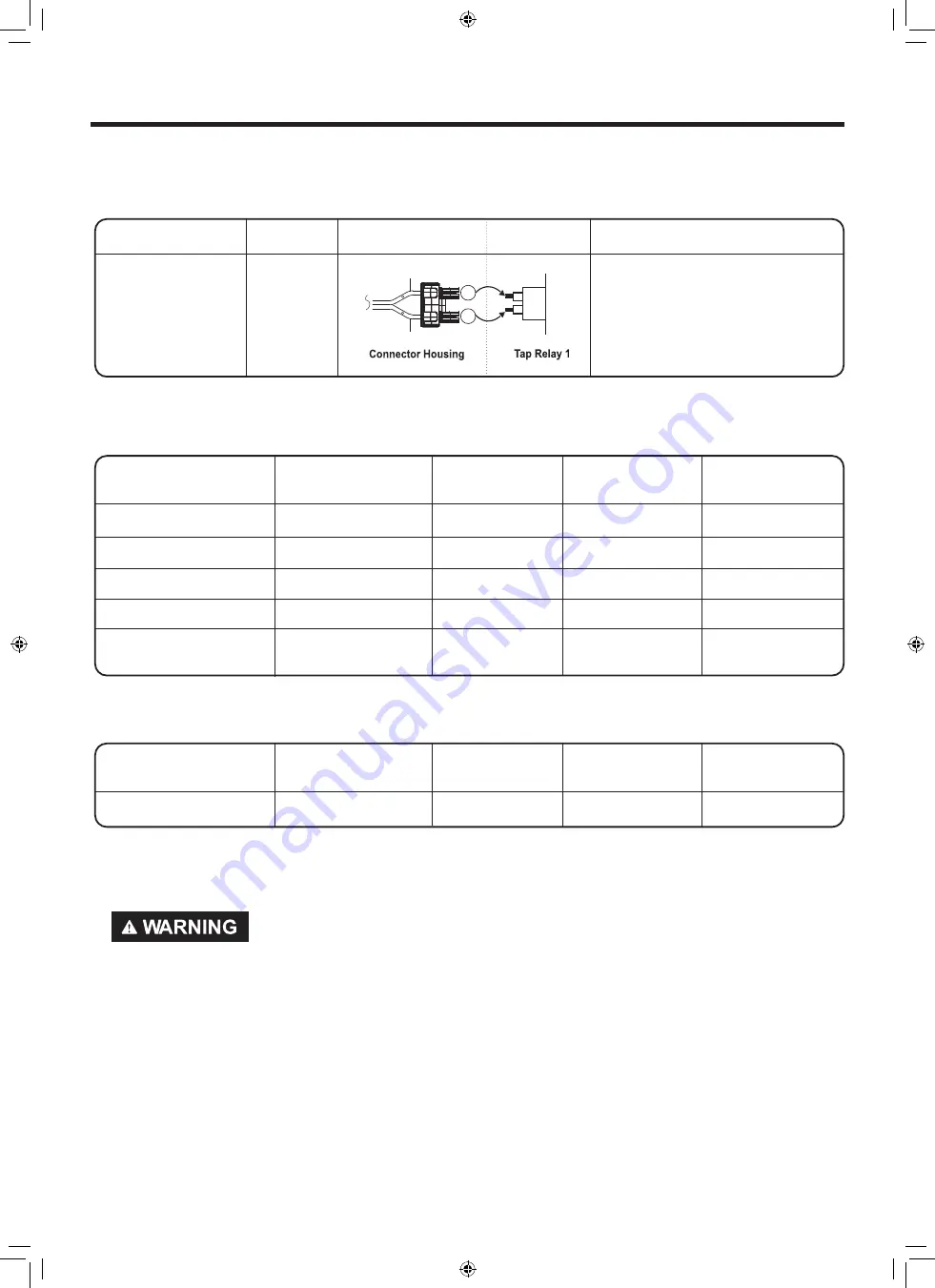
- 24 -
1
2
Blue Wire
Black Wire
< Table 2 > : Connection of Tap Relay with PCB ASSEMBLY (Gas)
< Table2 > : Incorrect connection of the tap relay and connector housing (Gas)
Color
Harness
PCB
Remark
Connector Housing
Black
Check the matching color between
harness wire and tap relay.
(Black housing – black tap relay)
3. Status Mode Of Wrong Connection
< Table1 > : Incorrect connection of the tap relay and connector housing (Electric)
Items
Case
Heater1
Operation(black)
Heater2
operation(White)
PCB condition
of operation
1.Black and White Housing
Wire
①
,
②
CROSS
Off
Off
Power Off
2.Black Housing
Wire
①
,
②
CROSS
Off
Off
Power Off
3.White Housing
Wire
①
,
②
CROSS
Normal
Normal
Power Off
*4.Black and White Housing
Housing CROSS
Heater 2
Heater 1
Power Off
5.Black and White Housing
Housing and Wire
①
,
②
CROSS
Off
Off
Power Off
Items
Case
Heater1
Operation(black)
Heater2
operation(White)
PCB condition
of operation
1. Black and white housing
Wire
①
,
②
CROSS
Off
Off
Power Off
CAUTION! Improper connection of the heater can damage the heater or the main board.
Summary of Contents for W3S1 Series
Page 13: ... 13 5 OPERATION 5 1 Control Panel Features WASHER W3S1CVK2 DRYER ...
Page 112: ...EXPLODED VIEW FULL ASSEMBLY WASHER DRYER DRYER WASHER Control Panel F1100 F112 F210 F113 EV ...
Page 121: ... 123 ELECTRIC DRYER GAS DRYER ...
Page 122: ... 124 ELECTRIC DRYER GAS DRYER ...
Page 123: ......
Page 124: ...P No MFL68588942 ...