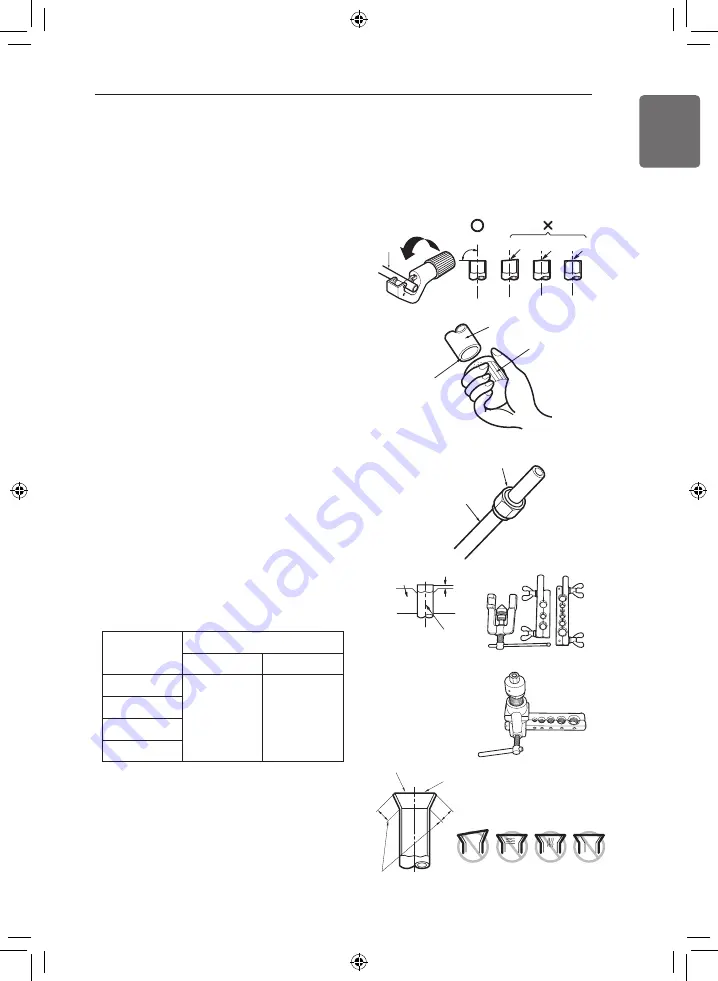
39
PIPING AND WIRING FOR OUTDOOR UNIT
ENGLISH
Step 1. Cut the pipes and the cable.
- Use the accessory piping kit or the pipes
purchased locally.
- Measure the distance between the indoor
unit and the outdoor unit.
- Cut the pipes a little longer than measured
distance.
- Cut the cable 1.5 m longer than the pipe
length.
Step 2. Burrs removal
- Completely remove all burrs from the cut
cross section of pipe/tube.
- Put the end of the copper tube/pipe to
downward direction as you remove burrs in
order to avoid to let burrs drop in the tubing.
Step 3. Putting nut on
- Remove flare nuts attached to indoor and
outdoor units, than put them on pipe/tube
having completed burr removal. (Not
possible to put them on after flaring work)
Step 4. Flaring work.
- Carry out flaring work using dedicated flaring
tool for R-410A refrigerant as shown below.
- Firmly hold copper tube in a bar(or die) as
indicated dimension in the table above.
Step 5. Check
- Compare the flared work with right figure.
- If flare is seemed to be defective, cut off the
flared section and do flaring work again.
Preparation for Piping
- Main cause of gas leakage is defect in flaring work. Carry out correct flaring work in the
following procedure.
- Use the de-oxidised copper as piping materials to install.
Inclined
Inside is shiny without scratches
Smooth all round
Even length
all round
Surface
damaged
Cracked Uneven
thickness
= Improper flaring =
Bar
Copper pipe
"A"
<Wing nut type>
<Clutch type>
Copper
tube
90°
Slanted Uneven Rough
Pipe
Reamer
Point down
Flare nut
Copper tube
Pipe diameter
(mm)
A (mm)
Wing nut type Clutch type
Ø 6.35
1.1~1.8
0~0.5
Ø 9.52
Ø 12.7
Ø 15.88