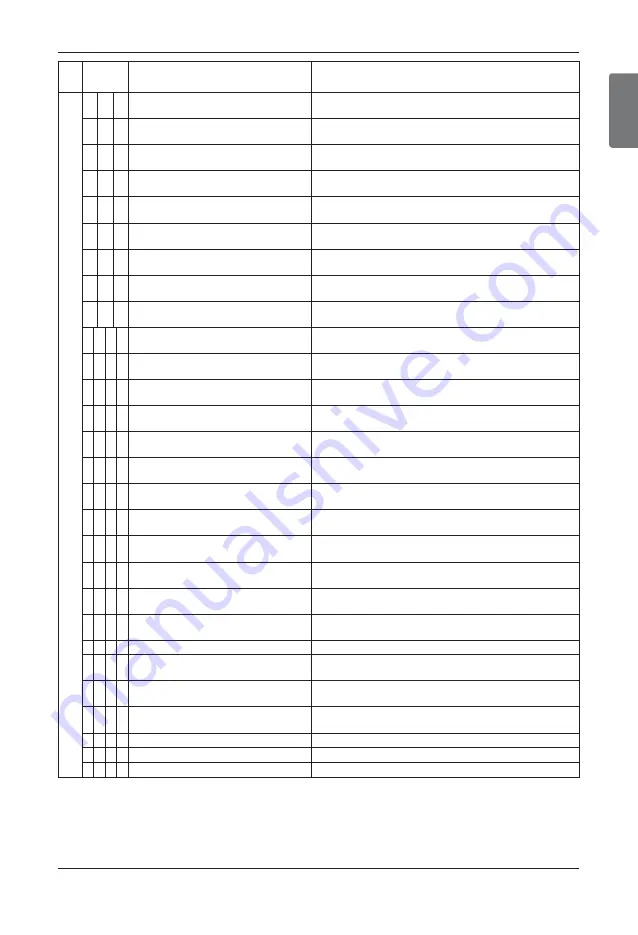
Test Run
Installation Manual
75
ENGLISH
Display
Error item
Root cause of error
number
When the master outside unit inverter PCB input current is different
When the slave1 outside unit inverter PCB input current is different
When the slave2 outside unit inverter PCB input current is different
Communication error between master outside unit master MICOM and
EEPROM or EEPROM missing
Communication error between slave1 outside unit master MICOM and
EEPROM or EEPROM missing
Communication error between slave2 outside unit master MICOM and
EEPROM or EEPROM missing
Master Communication error between master outside unit master PFC
and EEPROM or EEPROM missing
Slave1 Communication error between master outside unit master PFC
and EEPROM or EEPROM missing
Slave2 Communication error between master outside unit master PFC
and EEPROM or EEPROM missing
Master Failing to receive Slave Unit signal at main PCB of Master
Outdoor Unit
Slave1 Failing to receive Slave Unit signal at main PCB of Master
Outdoor Unit
Slave2 Failing to receive Slave Unit signal at main PCB of Master
Outdoor Unit
Master Liquid pipe temperature sensor of Master Outdoor Unit is open
or short
Slave1 Liquid pipe temperature sensor of Master Outdoor Unit is open
or short
Slave2 Liquid pipe temperature sensor of Master Outdoor Unit is open
or short
Master Outdoor Unit Subcooling Inlet Temperature Sensor open or
short
Slave1 Outdoor Unit Subcooling Inlet Temperature Sensor open or
short
Slave2 Outdoor Unit Subcooling Inlet Temperature Sensor open or
short
Master outside unit over-cooling outlet temperature sensor disconnec-
tion or short circuit
Slave1 outside unit over-cooling outlet temperature sensor disconnec-
tion or short circuit
Slave2 outside unit over-cooling outlet temperature sensor disconnec-
tion or short circuit
Outside unit 4 way valve switch error
Master outside unit static speed compressor burn, locking and over-
current
Slave1 outside unit static speed compressor burn, locking and over-
current
Slave2 outside unit static speed compressor burn, locking and over-
current
Plate type heat exchanger freeze prevention error
Water temperature sensor open/short
Communication error between main MICOM and sub MICOM
7
4
1
Master outside unit inverter PCB phase imbal-
ance
7
4
2
Slave1 outside unit inverter PCB phase imbal-
ance
7
4
3
Slave2 outside unit inverter PCB phase imbal-
ance
8
6
1
Master outside unit master PCB EEPROM
error
8
6
2
Slave1 outside unit master PCB EEPROM
error
8
6
3
Slave2 outside unit master PCB EEPROM
error
8
8
1
Master PFC PCB EEPROM error
8
8
2
Slave1 PFC PCB EEPROM error
8
8
3
Slave2 PFC PCB EEPROM error
1 0 4 1
Master Communication Error Between Master
Outdoor Unit and Other Outdoor Unit
1 0 4 2
Slave1 Communication Error Between Master
Outdoor Unit and Other Outdoor Unit
1 0 4 3
Slave2 Communication Error Between Master
Outdoor Unit and Other Outdoor Unit
1 1 3 1
Master Outdoor Unit Liquid pipe Temperature
Sensor Error
1 1 3 2
Slave1 Outdoor Unit Liquid pipe Temperature
Sensor Error
1 1 3 3
Slave2 Outdoor Unit Liquid pipe Temperature
Sensor Error
1 1 4 1
Master Outdoor Unit Subcooling Inlet
Temperature Sensor Error
1 1 4 2
Slave1 Outdoor Unit Subcooling Inlet
Temperature Sensor Error
1 1 4 3
Slave2 Outdoor Unit Subcooling Inlet
Temperature Sensor Error
1 1 5 1
Master outside unit over-cooling outlet temper-
ature sensor error
1 1 5 2
Slave1 outside unit over-cooling outlet temper-
ature sensor error
1 1 5 3
Slave2 outside unit over-cooling outlet temper-
ature sensor error
1 5 1 - Outside unit 4 way valve switch failure
1 7 3 1
Master outside unit static speed compressor
error
1 7 3 2
Slave1 outside unit static speed compressor
error
1 7 3 3
Slave2 outside unit static speed compressor
error
1 8 0 - Plate type heat exchanger freeze prevention
1 8 1 - Water temperature sensor error
1 8 2 - Communication error between MICOMs
Outside unit
n
Refer to the troubleshooting guide of service technical manual for each error.
Summary of Contents for MULTI V WATER II ARWN Series
Page 81: ......